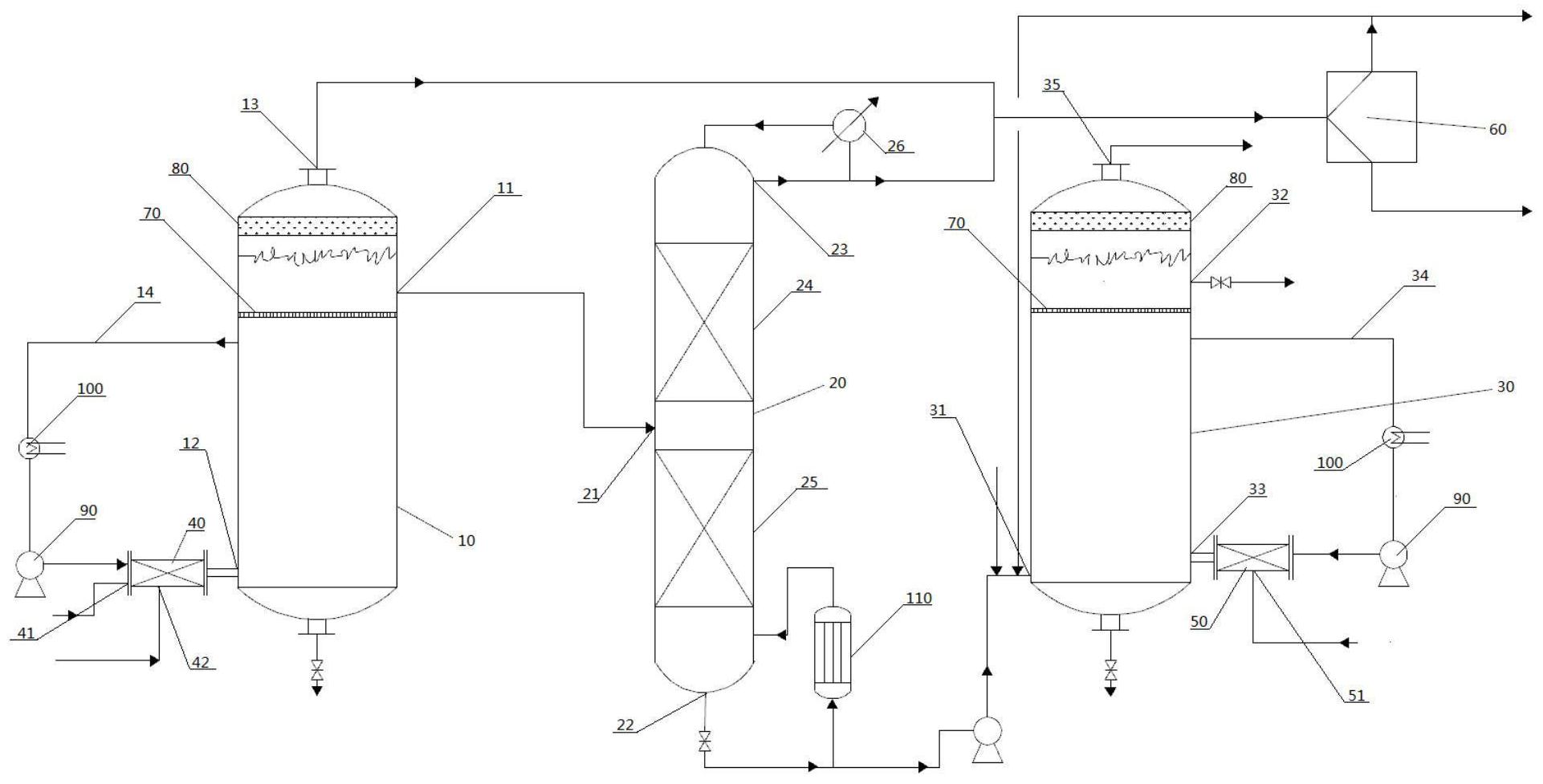
技术摘要:
本发明提供了一种对二甲苯制备对苯二甲酸的外置微界面氧化系统。该氧化系统包括:依次连接的第一反应器、精馏塔、第二反应器,第一反应器的侧壁设置有第一出口,第二反应器的侧壁设置有第一进口,精馏塔的侧壁设置有物料进口,精馏塔底部设置有物料出口;第一出口与精 全部
背景技术:
对苯二甲酸是一种重要的化工原料,通常由对二甲苯与含氧气体通过氧化反应制 得,主要包括4个步骤,对二甲苯(PX)→对甲基苯甲醛(TALD)→对甲基苯甲酸(p-TA)→对羧 基苯甲醛(4-CBA)→对苯二甲酸(TA),其中4个步骤反应过程非常复杂,涉及到气液的传热 传质,现有技术中的反应装置普遍传质效率较低,反应混合原料和空气无法得到充分混合, 相界面积有限,导致原料转化率低下,降低了对苯二甲酸的产率,因此工艺上不得不采用高 温高压操作,通过增加气液相的溶解度来提高传质面积及传质效率,然而前两个反应步骤 要以醋酸为溶剂,不宜采用高温高压,现有技术采用混合的反应工艺,同时伴随着大量的副 反应,导致醋酸消耗量大,能耗高,杂质含量高,产品质量无法得到保证。 有鉴于此,特提出本发明。
技术实现要素:
本发明的第一目的在于提供一种对二甲苯制备对苯二甲酸的外置微界面氧化系 统。该外置微界面氧化系统在反应器外部设置微界面发生器,通过设置了微界面发生器后, 可以增加空气和液相物料之间的相界面积,使得空气和液相物料在进入反应器之前充分破 碎混合,传质空间充分满足,增加了空气在液相中的停留时间,从而大幅提高反应速度、有 效控制副反应和提高产品收率,显著降低反应过程的能耗,同时降低了操作温度以及压力, 提高了反应的安全性,而且采用了分段式工艺,解决了醋酸溶剂不能承受高温氧化条件的 矛盾,提高了反应效率。 本发明的第二目的在于提供一种采用上述外置微界面氧化系统的对二甲苯制备 对苯二甲酸的方法,该方法有利于减少能耗,达到比现有工艺更佳的反应效果。 为了实现本发明的上述目的,特采用以下技术方案: 本发明提供了一种对二甲苯制备对苯二甲酸的外置微界面氧化系统,包括:依次 连接的第一反应器、精馏塔、第二反应器,所述第一反应器的侧壁设置有第一出口,所述第 二反应器的侧壁设置有第一进口,所述精馏塔的侧壁设置有物料进口,所述精馏塔底部设 置有物料出口; 所述第一出口与所述精馏塔的物料进口连接,所述第一进口与所述精馏塔的物料 出口连接; 所述第一反应器的外部设置有第一微界面发生器,所述第二反应器的外部设置有 第二微界面发生器; 所述第一微界面发生器的侧壁连接有第一空气进口,底部连接有原料进口,;所述 第二微界面发生器的底部连接有第二空气进口; 3 CN 111569788 A 说 明 书 2/7 页 所述第一反应器的外侧设置有第一循环管道,所述第一循环管道的一端与所述第 一微界面发生器的侧壁连接,另一端与所述第一反应器的侧壁连接。 所述第二反应器的外侧设置有第二循环管道,所述第二循环管道的一端与所述第 二微界面发生器的侧壁连接,另一端与所述第二反应器的侧壁连接。 现有技术中,对二甲苯制备对苯二甲酸的反应步骤如下: 即对二甲苯(PX)→对甲基苯甲醛(TALD)→对甲基苯甲酸(p-TA)→对羧基苯甲醛 (4-CBA)→对苯二甲酸(TA) 其中氧化反应过程非常复杂,涉及到气液的传热传质,现有技术中的反应装置普 遍传质效率较低,反应混合原料和空气无法得到充分混合,影响了反应效率和原料转化率。 本发明的外置微界面氧化系统通过在反应器外部设置微界面发生器后,空气和原料通入微 界面发生器后,内部实现强化传质、分散破碎,破碎形成了微气泡后进入反应器内,使得传 质空间充分满足,从而降低了空气的耗量,即使温度和压力不需要太高的条件下,也可以保 证反应本身的高反应效率。而且本发明采用分段式工艺,解决了醋酸溶剂不能承受高温氧 化条件的矛盾,提高了反应效率。 进一步的,所述第一微界面发生器和第二微界面发生器的设置方式不限、设置位 置不限,数量不限;所述第一微界面发生器与所述第二微界面发生器均可通过焊接或者法 兰形式与反应器的进口连接;此外,更优选的,所述第一反应器和第二反应器均可通过串联 或者并联的方式设置多个微界面发生器,所述多个微界面发生器均可连接反应器的进口。 进一步的,所述第一微界面发生器的设置数量至少为1个;所述第二微界面发生器 的设置数量至少为1个。 本领域所属技术人员可以理解的是,本发明所采用的微界面发生器在本发明人在 先专利中体现,如公开号106215730A的专利,微界面发生器其核心在于气泡破碎,气泡破碎 器的原理是高速射流所携带的气体相互撞击进行能量传递,使气泡破碎,关于微界面发生 器的结构在上述专利中公开其中一实施例,此不再赘述。关于微界面发生器与第一、第二反 应器、以及其他设备的连接,包括连接结构、连接位置,根据微界面发生器的结构而定,此不 作限定。关于微界面发生器的反应机理及控制方法,在本发明人在先专利CN107563051B中 已经公开,此不再赘述。 进一步的,所述第一循环管道通过循环物流(包括反应得到的对甲基苯甲醛、醋 酸、水、少量未反应完全的对二甲苯、中间产物等),所述循环物流和反应混合原料和空气一 起通入所述第一微界面发生器中进行分散破碎,破碎后形成了微气泡后进入所述第一反应 器内部进行氧化反应。 进一步的,所述第二循环管道通过循环物流(包括反应得到的对羧基苯甲醛、水、 中间产物等),所述循环物流和空气一起通入所述第二微界面发生器中进行分散破碎,破碎 后形成了的微气泡后进入所述第二反应器内部,与所述第一进口进来的物料(包括对甲基 苯甲酸,氢溴酸等)混合后继续二次氧化反应。 4 CN 111569788 A 说 明 书 3/7 页 此外,所述第一循环管道和第二循环管道均设置有提供动力的循环泵,所述循环 泵泵壳内壁设有金属传感探头,金属传感探头一侧的泵壳外壁设有温度传感器,金属传感 探头和温度传感器通过导线连接,可以随时监控循环泵中通液相物料的温度。更优选的,所 述第一循环管道和第二循环管道均设置有换热器,用来控制循环物料的温度,从而使得第 一反应器和第二反应器内部保持恒温,优选板式换热器,相比其他换热器,板式换热器具有 换热效率高,热损失小,高效节能,容易清洗拆装方便等特点。 第一反应器的第一出口设置在侧壁中上部,通过溢流管道,产出中间产物(主要成 分为对甲基苯甲酸,还包括醋酸、水、少量未反应完全的对二甲苯、中间产物等)进入精馏塔 的中部,在精馏塔中进行纯化分离。 第二反应器的第一进口设置在侧壁中下部,精馏塔塔底产出的物料(对甲基苯甲 酸和水)、补充的催化剂(氢溴酸)以及从酸水分离器中分离的水一起从第一进口进入第二 反应器中继续反应,空气从第二空气进口进入,循环物流从第二微界面发生器的侧壁进入, 所述空气和循环物流在所述第二微界面发生器内进行分散破碎后进入第二反应器中,与第 一进口进来的液相物料混合后进行二次氧化反应,生成的产物对苯二甲酸溶液从第二反应 器的侧壁上部的第三出口采出。 更进一步的,所述第一反应器和第二反应器内部上方均设置有防浪格栅,防浪格 栅主要起滤除泡沫的作用,除去气流中夹带的雾沫,以保证传质效率,降低有价值的物料损 失,所述防浪格栅可采用国产进口优质材质,如:Q235、304、304L、321、316L、F46、NS-80、镍 丝、钛丝及合金等材质。 进一步的,所述第一反应器和第二反应器内部上方均设置有除滤网,反应器的上 方积聚了大量中间产物等杂质,设置除滤网可过滤这些杂质,提高生成产物的纯度,所述除 滤网材料可采用金属或者塑料,优选不锈钢和尼龙材质。 进一步的,所述第一反应器顶部还设置有第二出口,所述第二出口连接有酸水分 离器。精馏塔塔顶采出的部分醋酸和水,与第一反应器顶部采出的尾气共同汇合后进入到 酸水分离器中,分离出的醋酸重新回到第一反应器内部循环使用,分离出的水一部分排出, 一部分进入第二反应器内部循环使用。 进一步的,本发明所采用的精馏塔,主要有轻组分分离段和重组分分离段组成,所 述轻组分分离段和重组分分离段之间的塔节上设置有物料进口,用于将第一反应器中的氧 化产物通入所述精馏塔中,从精馏塔的物料进口进来的物料主要有对甲基苯甲酸,还包括 醋酸、水、少量未反应完全的对二甲苯、中间产物等,对甲基苯甲酸和少量水经过位于物料 进口下方的重组分分离段被精馏分离到塔底,醋酸和大部分水经过轻组分分离段后朝着塔 顶方向被精馏分离,从馏出物出口引出的醋酸和水蒸汽经过冷凝器,一部分作为回流液从 塔顶返回精馏塔,其余部分通过管道与第一反应器中的尾气混合后进入酸水分离器,塔底 产物对甲基苯甲酸和少量水等液相物料采出后,一部分经过塔釜再沸器后作为回流液返回 重组分分离段继续精馏,另一部分经过第一进口进入第二反应器内后继续进行反应。 精馏塔中的轻组分分离段和重组分分离段可由若干塔板、填料任意组合而成,优 选地靠近塔釜位置采用塔板的结构,靠近塔顶位置采用填料的结构,因为塔板本身压降比 较大,填料压降比较小。 进一步的,所述精馏塔的塔顶设置有塔顶冷凝器,塔釜设置有塔釜再沸器,所述塔 5 CN 111569788 A 说 明 书 4/7 页 釜再沸器的类型为降膜式再沸器,这种类型的再沸器与普通的再沸器类型相比,在管壁上 成膜,换热效率很高,滞留时间短,不容易结焦,避免了塔釜的物质发生聚合有副产物生成。 除此之外,本发明还提供了一种采用上述外置微界面氧化系统的对二甲苯制备对 苯二甲酸的方法,其特征在于,包括如下步骤: 空气和混合原料通过第一反应器外置的微界面发生器进行分散破碎后进入第一 反应器内部进行氧化反应; 通过氧化反应得到的液相物料进入到精馏塔中进行分离; 精馏塔分离出的液相物料进入第二反应器中; 空气通过第二反应器外置的微界面发生器进行分散破碎后进入第二反应器内部, 与精馏塔分离出的液相物料混合后进行二次氧化反应得到对苯二甲酸。 进一步的,所述第一反应器内温度为120-155℃,压强为0.20-0.66MPa。 进一步的,所述第二反应器内温度为135-180℃,压强为0.56-0.82MPa。 与现有技术相比,本发明的有益效果在于: (1)本发明通过在反应器外部设置微界面发生器,可以增加空气和液相物料之间 的相界面积,使得空气和液相物料在进入反应器之前充分破碎混合,传质空间充分满足,增 加了空气在液相中的停留时间,从而大幅提高反应速度、有效控制副反应和提高产品收率, 显著降低反应过程的能耗,同时降低了操作温度以及压力,提高了反应的安全性。 (2)本发明通过分段式工艺,针对不同反应给予不同的反应条件,解决了对二甲苯 制备对苯二甲酸过程中,醋酸作为溶剂不能承受高温氧化条件的矛盾,并且能及时取出产 物,这种分段氧化有利于减少投资和消耗,达到比现有工艺更佳的反应效果。 附图说明 通过阅读下文优选实施方式的详细描述,各种其他的优点和益处对于本领域普通 技术人员将变得清楚明了。附图仅用于示出优选实施方式的目的,而并不认为是对本发明 的限制。而且在整个附图中,用相同的参考符号表示相同的部件。在附图中: 图1为本发明实施例提供的对二甲苯制备对苯二甲酸的外置微界面氧化系统的结 构示意图。 附图说明: 10-第一反应器; 11-第一出口; 12-第二进口; 13-第二出口; 14-第一循环管道; 15-第一残液出口; 20-精馏塔; 21-物料进口; 22-物料出口; 23-馏出物出口; 24-轻组分分离段; 25-重组分分离段; 26-冷凝器; 30-第二反应器; 31-第一进口; 32-第三出口; 33-第三进口; 34-第二循环管道; 35-废气出口; 36-第二残液出口; 6 CN 111569788 A 说 明 书 5/7 页 40-第一微界面发生器; 41-第一空气进口; 42-原料进口; 50-第二微界面发生器; 51-第二空气进口; 60-酸水分离器; 70-防浪格栅; 80-除滤网; 90-循环泵; 100-换热器; 110-塔釜再沸器。