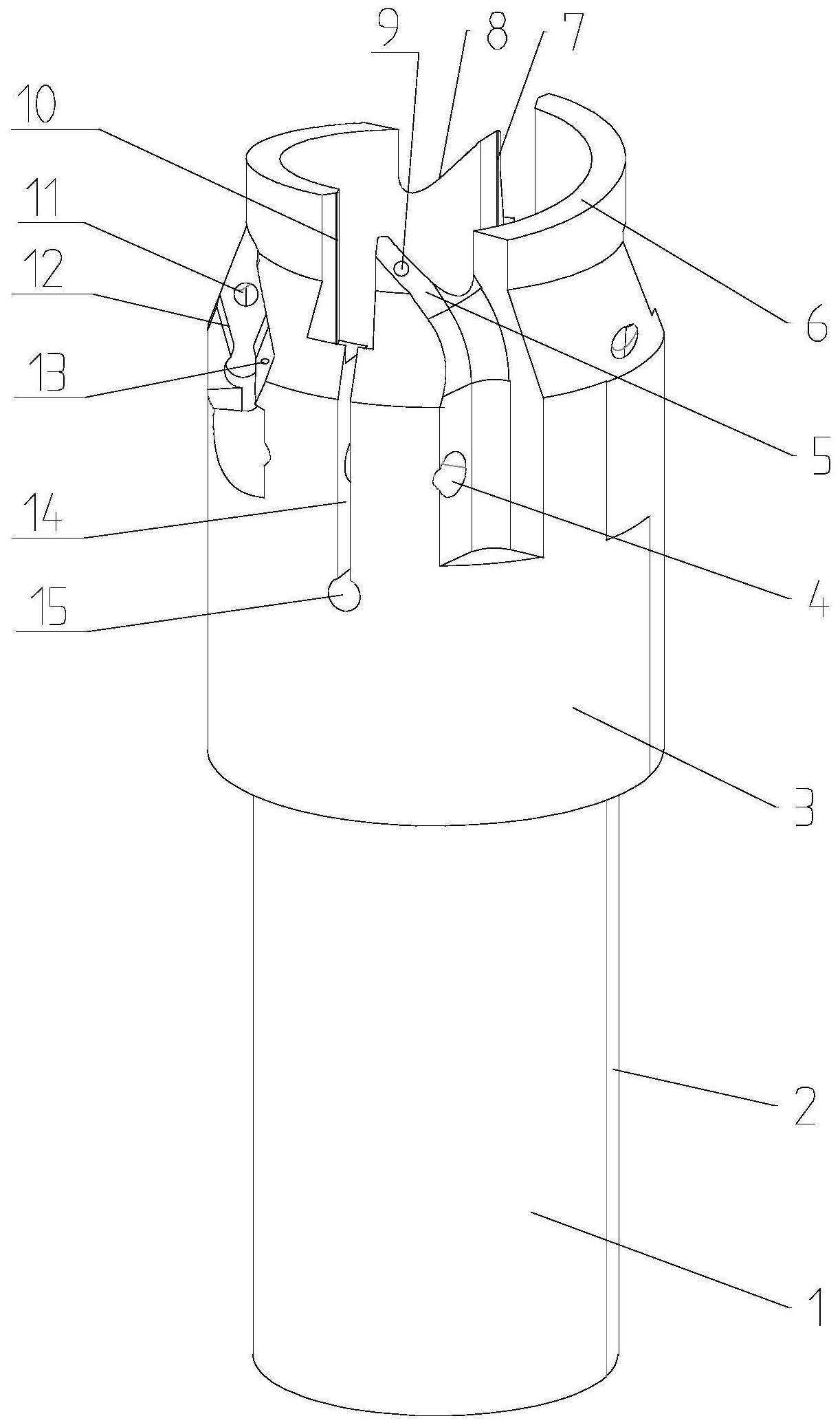
技术摘要:
本发明公开了一种不锈钢深槽加工的组合刀具,其主要由刀柄和刀头两部分组成。刀头装有4个刀片,其中用于车深槽的两个HFPR3003刀片装在刀头前端,另外两个用于加工倒角的VCMT110304刀片装在刀头中部,刀头为圆柱形,刀片16外侧刀尖用于加工槽大径尺寸,刀片17内侧刀尖用 全部
背景技术:
众所周知,不锈钢材料加工的难点是:1、 切削力大,切削温度高;2、 加工硬化严 重;3、 容易粘刀;4、 刀具磨损快。针对上述难点,加工过程中换刀频繁,从而影响了生产效 率,同时也增加了刀具使用成本。尤其是不锈钢深槽的加工,成了业界的难题。在槽加工领 域,公认为“伊斯卡”刀具最为好用,尤其是加工不锈钢材料的槽刀,该公司的IC354材质加 工不锈钢涂层刀片,不容易崩刀,使用寿命长,所以下述文件用“伊斯卡”刀具做对比说明。 一批316不锈钢工件订单,为硅溶胶精密铸造后加工,见图1和图2。分析图纸,此产品难点是 加工图2中端面深槽部位。槽大径为φ42.6mm,小径为φ35.4mm,经计算,槽宽为:(42.6- 35.4)/2=3.6 mm,槽的深度要求为22mm,从工件右端面到槽的底部槽深度为44mm。槽大径为 42.6mm,按图中要求槽直径和槽宽度查阅“伊斯卡”说明书,只有HFHR/L 25-38-3T12刀具接 近所需的槽直径,但槽深T只能加工12mm;而能加工22mm槽深的刀片,刀片的宽度和加工直 径范围又不能满足图纸要求。在槽的外部,还有加工6*20.14°倒角要求。如果此工件为单件 或小批量生产,可以考虑磨刀或用焊接刀片的方法解决,但此产品是批量订单,如果自己磨 刀具或用焊接刀具,刀具的尺寸精度、刀具寿命都不能满足要求,加工精度也不能保证,加 工的效率也会相应降低,所以磨刀或用焊接刀具都不能满足批量生产要求。针对上述分析, 加工不锈钢深槽,最好的办法是利用现有刀具厂家已研制成功的可转位成型刀片,设计一 种不锈钢深槽加工的组合刀具,刀片磨损后直接更换刀片的方法,来满足工件深槽的加工 需求。
技术实现要素:
本发明目的是利用现有可转位成型刀片,设计一种不锈钢深槽加工的组合刀具, 刀片磨损后直接更换刀片,满足不锈钢深槽产品批量生产的需求。 本发明的构思是,工件主要加工M52外螺纹、端面槽、倒角和内孔,属于回转体加 工,适合在数控车床上加工此产品,所以刀具设计也应以数控车床为基础进行,设计一把适 合数控车床用的端面槽刀具,来满足此工件深槽加工的要求。此工件的典型特点是槽窄且 深,在设计刀具时,重点要解决刀具的刚性问题。 具体的,一种不锈钢深槽加工的组合刀具,主要由刀柄和刀头两部分组成,为提高 刀具的刚性,本发明的刀具由弹簧钢棒料整体制造,中间没有焊接。槽尺寸要求为:大径φ 42.6mm,小径φ35.4mm,为了提高刀具的强度,刀头部分应尽量厚实,所以最理想的方式是 做成圆柱形,利用整个圆柱支撑刀片,大径φ42.6mm,小径φ35.4 mm,这样设计会使强度最 高。具体的,考虑到车削时排屑和实际使用情况,刀头顶端直径尺寸应稍小于槽刀片直径, 需留有一定间隙,所以新刀具刀头顶端大径尺寸设计为φ42.2 mm,小径φ35.8 mm。从图8 3 CN 111604510 A 说 明 书 2/4 页 中可以看出,刀具厂家设计的刀具只装一个刀片,但为了提高加工效率,按180°对称原则, 本发明设计的刀具上装有2个槽刀刀片。其中零件16, HFPR 3003外侧刀尖加工直径按大径 φ42.6mm设计;零件17, HFPR 3003内侧刀尖按槽小径φ35.4 mm设计,这样就能保证槽直 径一次加工合格。提前测绘HFPR刀片尺寸,HFPR刀托和HFPR压板按刀片定位槽形状尺寸铣 出,以保证准确定位,同时HFPR刀托直接做出5~7°前角。这样在设计的时候, 2个刀片的刀 尖过刀柄中心并且最高点在同一平面,来满足两个刀片同时参与车削,槽宽一次成型,比一 个刀片车削效率提高50%。为了将刀片夹持牢固,刀头上用线切割割出缓冲槽,以保证螺丝 能完全彻底的压紧HFPR 3003刀片。此工件为深槽加工,加工过程中容易积屑,为了保证加 工过程中顺利排屑,本发明设计了“Y”形排屑槽,“Y”形排屑槽前段模拟排屑形状,做成R曲 线,帮助排屑;后半部分为直段,帮助断屑,促使切屑及时排除,避免积屑造成刀具折断。为 帮助排屑,刀头顶端设计呈螺旋下降的状态。在槽的外侧,还要加工6*20.14°倒角。为了提 高加工效率,本发明设计成组合刀具,将这个倒角与槽一起加工,这样会提高加工效率。本 发明在上述刀头上,根据倒角角度要求,选用VCMT110304刀片,根据倒角尺寸要求,在与 HFPR 3003刀片垂直的截面,做出两个安放VCMT刀位,VCMT刀位尺寸对称坐中。这样,加工端 面槽与倒角,做成一支刀具,一次加工成形,大大提高了加工效率。为提高刀片使用寿命,在 4个刀片上方,都设计了出水孔,使冷却液能准确的喷到刀尖,达到及时冷却效果。 为了提高刀具的强度,刀柄部分依数控车床刀座最大内孔尺寸设计,直接装到数 控车床刀座内孔中。为保证压紧牢靠,刀柄上铣有定位面。 本发明的设计过程是这样的: 一种不锈钢深槽加工的组合刀具,主要由刀柄和刀头两部分组成。为提高刀具的刚 性,本发明的刀具由弹簧钢棒料整体制造,中间没有焊接。图中槽尺寸要求为:大径φ 42.6mm,小径φ35.4mm,为了提高刀具的强度,刀头部分应尽量厚实,所以最理想的方式是 做成圆柱形,利用整个圆柱支撑刀片,大径φ42.6mm,小径φ35.4 mm,这样设计会使强度最 高。具体的,考虑到车削时排屑和实际使用情况,刀头顶端直径尺寸应稍小于槽刀片直径, 需留有一定间隙,所以新刀具刀头顶端大径尺寸设计为φ42.2 mm,小径φ35.8 mm。从图8 中可以看出,刀具厂家设计的刀具只装一个刀片,但为了提高加工效率,按180°对称原则, 本发明设计的刀具上装有2个槽刀刀片。其中零件16, HFPR 3003外侧刀尖加工直径按大径 φ42.6mm设计;零件17, HFPR 3003内侧刀尖按槽小径φ35.4 mm设计,这样就能保证槽直 径一次加工合格。提前测绘HFPR刀片尺寸,HFPR刀托和HFPR压板按刀片定位槽形状尺寸铣 出,以保证准确定位,同时HFPR刀托直接做出5~7°前角。这样在设计的时候, 2个刀片的刀 尖过刀柄中心并且最高点在同一平面,来满足两个刀片同时参与车削,槽宽一次成型,比一 个刀片车削效率提高50%。为了将刀片夹持牢固,刀头上用线切割割出缓冲槽,以保证螺丝 能完全彻底的压紧HFPR 3003刀片。此工件为深槽加工,加工过程中容易积屑,为了保证加 工过程中顺利排屑,本发明设计了“Y”形排屑槽,“Y”形排屑槽前段模拟排屑形状,做成R曲 线,帮助排屑;后半部分为直段,帮助断屑,促使切屑及时排除,避免积屑造成刀具折断。为 帮助排屑,刀头顶端设计成螺旋下降的状态。 同理,分析工件加工图,在槽的外侧,图中还要加工6*20.14°倒角。为了提高加工 效率,本发明设计成组合刀具,将这个倒角与槽一起加工,这样会提高加工效率。本发明在 上述刀头上,根据倒角角度要求,选用VCMT110304刀片,根据倒角尺寸要求,在与HFPR 3003 4 CN 111604510 A 说 明 书 3/4 页 刀片垂直的截面,做出两个安放VCMT刀位,VCMT刀位尺寸对称坐中。这样,加工端面槽与倒 角,做成一支刀具,一次加工成形,大大提高了加工效率。 为提高刀片使用寿命,在4个刀片上方,都设计了出水孔,使冷却液能准确的喷到 刀尖,达到及时冷却效果。 为了提高刀具的强度,刀柄部分依数控车床刀座最大内孔尺寸设计,直接装到数 控车床刀座内孔中。为保证压紧牢靠,刀柄上铣有定位面。 本发明取得的有益效果如下: 1、圆柱形刀具,刚性好,解决了端面深槽加工的问题。2、本发明利用现有成形机夹刀 片,设计成多刀片组合刀具,刀尖磨损后直接更换刀片,提高了工作效率。3、“Y”形排屑槽前 段模拟排屑形状,做成R曲线,帮助排屑;后半部分为直段,帮助断屑,促使切屑及时排除,避 免积屑造成刀具折断。 附图说明 图1、是加工零件毛坯外形尺寸示意图。 图2、是加工零件槽部位尺寸图。 图3、是本发明组合刀具外形结构示意图。 图4、是本发明组合刀具A-A剖面结构示意图。 图5、是本发明组合刀具B-B剖面结构示意图。 图6、是本发明组合刀具俯视图。 图7、是本发明组合刀具刀托局部放大图。 图8、是伊斯卡端面槽刀形状示意图。 图9、是本发明组合刀具安装刀片后示意图。 图中标号代表的含义如下: 1、刀柄 2、定位面 3、刀头 4、螺丝孔 5、Y形排屑槽 6、刀头顶端 7、HFPR压板 8、Y形排屑槽 9、出水孔 10、HFPR刀托 11、螺丝孔 12、VCMT刀位 13、出水孔 14、缓 冲槽 15、工艺孔 16、 HFPR 3003刀片 17、 HFPR 3003刀片 18、VCMT110304刀片 19、 VCMT110304刀片。