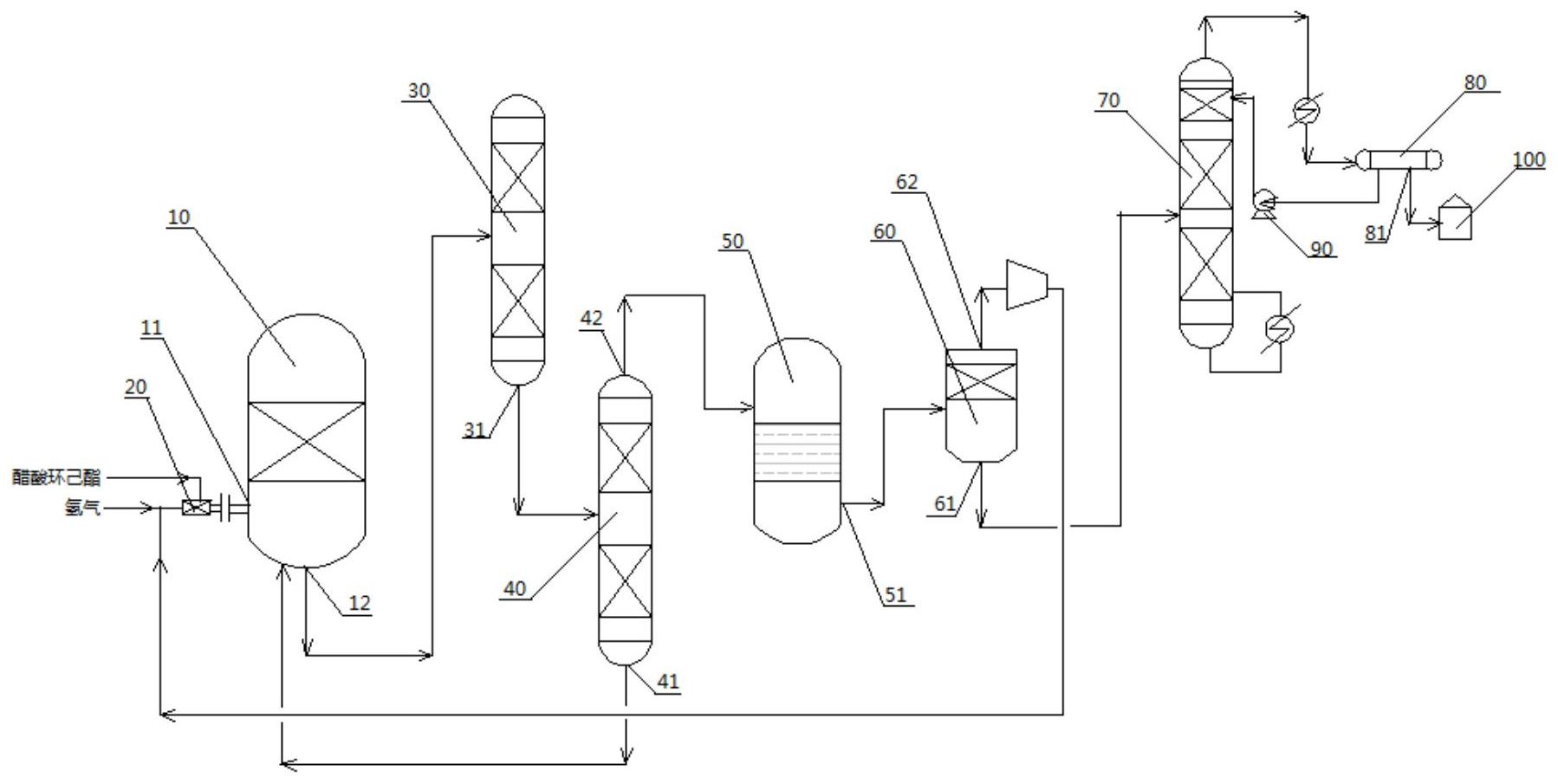
技术摘要:
本发明提供了一种酯化法制备环己酮的外置微界面强化系统,包括酯化反应器;酯化反应器的侧壁设置有原料进口,原料进口连接微界面发生器以用于分散破碎气体成气泡,反应物出口连接乙醇精馏塔以用于分离反应物中的乙醇;乙醇精馏塔塔底设置有重组分出口,重组分出口连接 全部
背景技术:
环己酮是一种重要的有机化工原料,在我国,65%的环己酮作为生产己内酰胺的 原料,20%的环己酮作为生产己二酸的原料,其余的环己酮作为相关化工原料;另外,环己 酮还是优良的溶剂,可用作油漆硝化纤维、氯乙烯聚合物和共聚物的溶剂。随着我国化纤工 业的迅速发展,己内酰胺、己二酸产量逐年增加,环己酮的需求量也日益俱增,开发利用前 景广阔。 酯化法是目前最新的环己酮生产工艺,主要由醋酸环己酯和氢气在酮系催化剂发 生加成反应,生成醋酸和环己醇,环己醇在脱氢催化剂作用下脱氢制得环己酮。该套工艺具 有较高的转化率和选择性,几乎没有三废产生,具有较高的原子经济性。同时相较于环己烯 水合法省去环己烷/环己烯的分离工艺,显著的降低了能耗。并且副产物乙醇可以用于其他 化工生产,增加了产品附加值,增加了效益。然而,酯化法制备环己酮虽然有着明显的工艺 优势,但也存在着一些缺陷:一方面,现有酯化反应器的气液相传质面积有限,反应过程中, 醋酸环己酯和氢气无法得到充分混合,气液相之间的传质效率低下,反应效率低下,另一方 面酯化反应的温度和压力较高,导致系统的安全性和稳定性大大的降低。 有鉴于此,特提出本发明。
技术实现要素:
鉴于此,本发明的第一目的在于提供一种酯化法制备环己酮的外置微界面强化系 统,该反应系统在原料进口设置微界面发生器,通过设置了微界面发生器后,一方面可以将 氢气分散破碎成直径微米级的微气泡,增大了氢气和醋酸环己酯之间的相界面积,使得传 质空间充分满足,提高了气液相之间的传质效率从而提高了反应效率,而且物耗、能耗低, 降低了企业的生产成本;同时还降低了酯化反应的温度和压力,增加了系统的安全性和稳 定性。 本发明的第二目的在于提供一种采用上述强化系统进行酯化法制备环己酮的方 法,该方法的操作条件更加温和,在保证反应效率的同时降低了反应的温度和压力,而且安 全性能高、能耗低,达到了比现有工艺更佳的反应效果。 为了实现本发明的上述目的,特采用以下技术方案: 本发明提供了一种酯化法制备环己酮的外置微界面强化系统,包括酯化反应器; 所述酯化反应器的侧壁设置有原料进口,底部设置有反应物出口,所述原料进口连接微界 面发生器以用于分散破碎气体成气泡,所述反应物出口连接乙醇精馏塔以用于分离反应物 中的乙醇; 所述乙醇精馏塔塔底设置有重组分出口,所述重组分出口连接环己醇精馏塔以用 3 CN 111574346 A 说 明 书 2/6 页 于分离出气相环己醇;所述环己醇精馏塔的顶部设置有气相出口,所述气相出口连接脱氢 反应器以用于进行环己醇脱氢反应;所述脱氢反应器的侧壁设置有产物出口,所述产物出 口连接气液分离器以用于分离氢气;所述气液分离器的底部设置有醇酮液出口,所述醇酮 液出口连接环己酮精馏塔以用于分离环己酮。 现有技术中,酯化法制备环己酮的反应工艺存在以下问题:现有酯化反应器的气 液相传质面积有限,反应过程中,醋酸环己酯和氢气无法得到充分混合,气液相之间的传质 效率低下,反应效率低下,另一方面酯化反应的温度和压力较高,导致系统的安全性和稳定 性大大的降低。本发明的酯化法制备环己酮的外置微界面强化系统,通过在原料口设置了 微界面发生器后,一方面可以将氢气分散破碎成直径微米级的微气泡,增大了氢气和醋酸 环己酯之间的相界面积,使得传质空间充分满足,提高了气液相之间的传质效率从而提高 了反应效率,而且物耗、能耗低,降低了企业的生产成本;同时还降低了酯化反应的温度和 压力,增加了系统的安全性和稳定性。 进一步的,所述气液分离器的顶部设置有氢气出口,所述氢气出口连接所述微界 面发生器以用于分离出的氢气重新返回利用。经过环己醇脱氢反应后的产物中会含有大量 的氢气,通过气液分离器可以回收这部分氢气,充分提高了氢气的利用率。优选地,所述氢 气出口设置有氢气压缩机以用于在氢气回收利用前先进行压缩。 进一步的,所述环己醇精馏塔的底部设置有釜液出口,所述釜液出口连接所述酯 化反应器以用于未反应的醋酸环己酯重新返回利用。经过酯化反应后的反应物中含有少量 的未反应的醋酸环己酯,在经过乙醇精馏和环己醇精馏后从釜液出口流出,回到酯化反应 器中重新参与酯化反应,充分提高了原料的利用率。 进一步的,所述微界面发生器为气动式微界面发生器,所述微界面发生器的设置 数量至少为一个以上。 进一步的,所述微界面发生器设置方式不限、设置位置不限,数量也不限;更优选 的,所述微界面发生器数量为一个以上,在酯化反应器之前由上到下依次并列设置,通过这 种多排并列设置的微界面发生器同时对进来的氢气进行分散破碎,更能够有效的提升后续 的反应效率。 本领域所属技术人员可以理解的是,本发明所采用的微界面发生器在本发明人在 先专利中已有体现,如申请号CN201610641119.6、201610641251 .7、CN201710766435 .0、 CN106187660、CN105903425A、CN109437390A、CN205833127U及CN207581700U的专利。在先专 利CN201610641119.6中详细介绍了微米气泡发生器(即微界面发生器)的具体产品结构和 工作原理,该申请文件中记载了“微米气泡发生器包括本体和二次破碎件、本体内具有空 腔,本体上设有与空腔连通的进口,空腔的相对的第一端和第二端均敞开,其中空腔的横截 面积从空腔的中部向空腔的第一端和第二端减小;二次破碎件设在空腔的第一端和第二端 中的至少一个处,二次破碎件的一部分设在空腔内,二次破碎件与空腔两端敞开的通孔之 间形成一个环形通道。微米气泡发生器还包括进气管和进液管。”从该申请文件中公开的具 体结构可以知晓其具体工作原理为:液体通过进液管切向进入微米气泡发生器内,超高速 旋转并切割气体,使气体气泡破碎成微米级别的微气泡,从而提高液相与气相之间的传质 面积,而且该专利中的微米气泡发生器属于气动式微界面发生器。 另外,在先专利201610641251 .7中有记载一次气泡破碎器具有循环液进口、循环 4 CN 111574346 A 说 明 书 3/6 页 气进口和气液混合物出口,二次气泡破碎器则是将进料口与气液混合物出口连通,说明气 泡破碎器都是需要气液混合进入,另外从后面的附图中可知,一次气泡破碎器主要是利用 循环液作为动力,所以其实一次气泡破碎器属于液动式微界面发生器,二次气泡破碎器是 将气液混合物同时通入到椭圆形的旋转球中进行旋转,从而在旋转的过程中实现气泡破 碎,所以二次气泡破碎器实际上是属于气液联动式微界面发生器。其实,无论是液动式微界 面发生器,还是气液联动式微界面发生器,都属于微界面发生器的一种具体形式,然而本发 明所采用的微界面发生器并不局限于上述几种形式,在先专利中所记载的气泡破碎器的具 体结构只是本发明微界面发生器可采用的其中一种形式而已。 此外,在先专利201710766435.0中记载到“气泡破碎器的原理就是高速射流以达 到气体相互碰撞”,并且也阐述了其可以用于微界面强化反应器,验证本身气泡破碎器与微 界面发生器之间的关联性;而且在先专利CN106187660中对于气泡破碎器的具体结构也有 相关的记载,具体见说明书中第-段,以及附图部分,其对气泡破碎器S-2的具 体工作原理有详细的阐述,气泡破碎器顶部是液相进口,侧面是气相进口,通过从顶部进来 的液相提供卷吸动力,从而达到粉碎成超细气泡的效果,附图中也可见气泡破碎器呈锥形 的结构,上部的直径比下部的直径要大,也是为了液相能够更好的提供卷吸动力。 由于在先专利申请的初期,微界面发生器才刚研发出来,所以早期命名为微米气 泡发生器(CN201610641119.6)、气泡破碎器(201710766435.0)等,随着不断技术改进,后期 更名为微界面发生器,现在本发明中的微界面发生器相当于之前的微米气泡发生器、气泡 破碎器等,只是名称不一样。 综上所述,本发明的微界面发生器属于现有技术,虽然有的气泡破碎器属于气动 式气泡破碎器类型,有的气泡破碎器属于液动式气泡破碎器类型,还有的属于气液联动式 气泡破碎器类型,但是类型之间的差别主要是根据具体工况的不同进行选择,另外关于微 界面发生器与反应器、以及其他设备的连接,包括连接结构、连接位置,根据微界面发生器 的结构而定,此不作限定。 进一步的,还包括环己酮回流罐,所述环己酮回流罐的底部设置有将部分环己酮 返回到环己酮精馏塔内的回流管路;所述回流管路上设置有回流泵。一部分环己酮回流罐 内的冷凝液经过回流泵加压后作为回流管路回流至所述环己酮精馏塔内,以用于摄取所述 环己酮精馏塔塔顶多余热量,维持全塔热平衡,经过多次回流,还可以提高环己酮的回收纯 度。相比自然回流,采用回流泵可调节回流量,使得回流量稳定,操作性好。 进一步的,所述环己酮回流罐的底部还设置有用于反应产物排出的环己酮出口。 所述环己酮出口连接有环己酮塔以用于回收环己酮。 进一步的,所述酯化反应器和脱氢反应器均为固定床催化反应器。由于固定床催 化反应器内部催化剂直接装填在固定床上,因此在床层内不易磨损,可长期使用,而且反应 器结构简单,操作方便。 除此之外,本发明还提供了一种采用上述强化系统进行酯化法制备环己酮的方 法,包括如下步骤: 氢气分散破碎成微气泡后与醋酸环己酯充分乳化后进行酯化反应,生成乙醇和环 己醇,环己醇经脱氢反应后制得环己酮。 进一步地,氢气经过微界面发生器分散破碎成微气泡后,与醋酸环己酯充分乳化 5 CN 111574346 A 说 明 书 4/6 页 后进行酯化反应生成乙醇和环己醇,反应产物进入乙醇精馏塔分离出乙醇后再进入环己醇 精馏塔中,气相环己醇从塔顶出来进入脱氢反应器中进行脱氢反应,脱氢后的产物再进入 气液分离器中,分离氢气后的醇酮液最后进入环己酮精馏塔内分离出环己酮并进行收集。 进一步的,所述酯化反应的温度为180-200℃;压力为2.0-3.0MPa。 与现有技术相比,本发明的有益效果在于: 本发明的酯化法制备环己酮的外置微界面强化系统,通过在酯化反应器的原料进 口设置微界面发生器后,一方面可以将氢气分散破碎成直径微米级的微气泡,增大了氢气 和醋酸环己酯之间的相界面积,使得传质空间充分满足,而且增加了氢气在液相中的停留 时间,降低了氢气的耗量,从而大幅提高反应效率、显著降低反应过程中的能耗,降低了企 业的生成成本;另一方面降低了酯化反应的温度和压力,增加了系统的安全性和稳定性。 附图说明 通过阅读下文优选实施方式的详细描述,各种其他的优点和益处对于本领域普通 技术人员将变得清楚明了。附图仅用于示出优选实施方式的目的,而并不认为是对本发明 的限制。而且在整个附图中,用相同的参考符号表示相同的部件。在附图中: 图1为本发明实施例提供的内置微界面氨肟化反应系统的结构示意图。 附图说明: 10-酯化反应器; 11-原料进口; 12-反应物出口; 20-微界面发生器; 30-乙醇精馏塔; 31-重组分出口; 40-环己醇精馏塔; 41-釜液出口; 42-气相出口; 50-脱氢反应器; 51-产物出口; 60-气液分离器; 61-醇酮液出口; 62-氢气出口; 70-环己酮精馏塔; 80-环己酮回流罐; 81-环己酮出口; 90-回流泵; 100-环己酮塔。