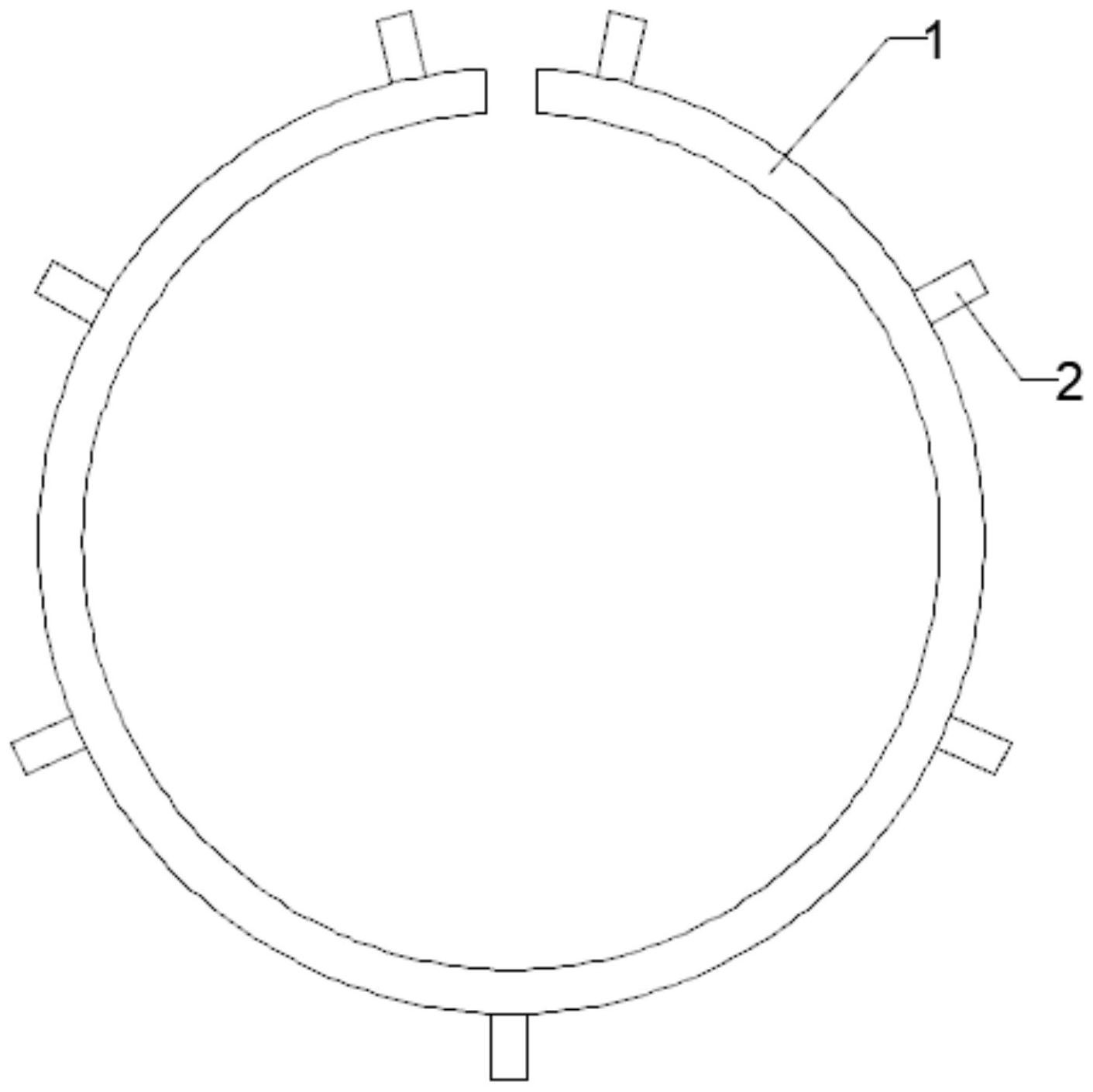
技术摘要:
本发明提供了一种磁控溅射环件及其配合孔的加工方法,所述的磁控溅射环件包括环件本体,所述环件本体的外侧环面上设置有至少一个配合孔,所述配合孔内固定有突出于环件本体外侧环面的连接结。使用四轴加工中心对环件本体配合孔进行加工,由于现有加工方案需要操作人员 全部
背景技术:
随着信息时代的来临,微电子和半导体技术在国民经济发展中扮演着举足轻重的 角色,磁控溅射技术则极大地推动着微电子和半导体行业的发展。磁控溅射的原理是利用 高能粒子轰击高纯靶材靶面,使靶材原子获得能量克服表面逸出功而从表面逸出沉积到基 板上形成薄膜层。但是高能粒子从各个方向轰击靶材使逸出的靶材原子方向不唯一。当不 同方向的靶材原子沿直线到达基板表面时会降低基板各部分沉积的薄膜层的均匀性,尤其 当基板特征尺寸小,填孔深宽比大的情况下,靶材原子仅有一部分能垂直沉积到基底上,而 大深宽比的台阶孔容易被堵住形成孔洞。 为解决上述问题,在靶材和和基板之间设置一个与靶材相同材质的环件。在环件 上施加射频电源后形成高密度等离子区,从靶材逸出的原子在等离子区被电离成带电粒 子,不同方向运动的带电粒子在靶材和基板之间的电场作用下都垂直方向沉积于基板上, 对深孔沉积效果良好。溅射环还可以吸附溅射过程中产生的颗粒物,防止基板被污染破坏。 CN204111859U公开了一种磁控溅射环装置和磁控溅射反应器,其中,磁控溅射环 装置包括:安装于磁控溅射腔室侧壁上,所述磁控溅射腔室侧壁具有定位销套,所述磁控溅 射环装置包括:磁控溅射环,所述磁控溅射环包括内环侧壁和与所述内环侧壁相对的外环 侧壁,所述外环侧壁具有凹槽;定位销,一端与凹槽底部连接,另一端套设在定位销套中,所 述内环侧壁与所述定位销套距离不变,所述磁控溅射环的外环侧壁与所述定位销套之间的 距离为大于0.01毫米且小于6毫米。 CN110670031A公开了一种钽环及制备方法、包含钽环的溅射装置及其应用,所述 钽环包括环件以及设置在环件表面的花纹,所述花纹呈锥形凹坑状;锥形凹坑状花纹具有 较大的比表面积,当在用于溅射过程中,能够附着较大量的溅射源,并且具有较好的附着 力,此外花纹呈现锥形凹坑状,锥形凹坑的顶部朝向环件内部,相邻两个锥形凹坑的底部相 连,呈现平面状的结构,而非带有尖端的结构。 在采用物理气相沉积镀膜的过程中,会使用磁控溅射环件配合钽靶材一起使用, 环件通过焊接在磁控溅射环件本体上的连接结与机台螺丝固定并发挥了导电作用。环件本 体与连接结在焊接过程中需要一个配合孔,此配合孔需要通过数控加工中心与手动分度头 配合加工,手动分度头是通过手动摇动控制角度,劳动强度大,且有摇错角度风险,不合适 大批量生产。
技术实现要素:
针对现有技术存在的不足,本发明的目的在于提供一种磁控溅射环件及其配合孔 的加工方法,使用四轴加工中心对环件本体配合孔进行加工,由于现有加工方案需要操作 人员手动旋转环件本体,不仅劳动强度大,且有摇错风险,不适合大批量生产。本发明采用 4 CN 111575663 A 说 明 书 2/8 页 先进的四轴加工替代传统的手动分度旋转,从而实现了对旋转角度的精确控制,有效降低 了摇错风险和操作人员的劳动强度。 为达此目的,本发明采用以下技术方案: 第一方面,本发明提供了一种磁控溅射环件所述的磁控溅射环件包括环件本体, 所述环件本体的外侧环面上设置有至少一个配合孔,所述配合孔内固定有突出于环件本体 外侧环面的连接结。 作为本发明一种优选的技术方案,所述的连接结为柱状结构。 优选地,所述的配合孔为盲孔或通孔。 优选地,所述的连接结焊接固定于配合孔内。 优选地,所述的配合孔为盲孔,所述盲孔的深度为1 .2~1 .5mm,例如可以是 1.20mm、1.22mm、1.24mm、1.26mm、1.28mm、1.30mm、1.32mm、1.34mm、1.36mm、1.38mm、1.40mm、 1.42mm、1.44mm、1.46mm、1.48mm或1.50mm,但并不仅限于所列举的数值,该数值范围内其他 未列举的数值同样适用。所述的盲孔的直径为25~26mm,例如可以是25 .0mm、25 .1mm、 25.2mm、25.3mm、25.4mm、25.5mm、25.6mm、25.7mm、25.8mm、25.9mm或26.0mm,但并不仅限于 所列举的数值,该数值范围内其他未列举的数值同样适用。 优选地,所述的配合孔为通孔,所述通孔的直径为5~10mm,例如可以是5mm、6mm、 7mm、8mm、9mm或10mm,但并不仅限于所列举的数值,该数值范围内其他未列举的数值同样适 用。 作为本发明一种优选的技术方案,所述的环件本体的外侧环面的直径为200~ 400mm,例如可以是200mm、210mm、220mm、230mm、240mm、250mm、260mm、270mm、280mm、290mm、 300mm、310mm、320mm、330mm、340mm、350mm、360mm、370mm、380mm、390mm或400mm,但并不仅限 于所列举的数值,该数值范围内其他未列举的数值同样适用。 作为本发明一种优选的技术方案,所述的环件本体所用材料为钽金属。 作为本发明一种优选的技术方案,所述的环件本体通过条形板材两端对接形成所 述的环形本体。 优选地,所述的条形板材的宽度为45~55mm,例如可以是45mm、46mm、47mm、48mm、 49mm、50mm、51mm、52mm、53mm、54mm或55mm,但并不仅限于所列举的数值,该数值范围内其他 未列举的数值同样适用。 优选地,所述的条形板材的厚度为3~6mm,例如可以是3 .0mm、3 .2mm、3 .4mm、 3.6mm、3.8mm、4.0mm、4.2mm、4.4mm、4.6mm、4.8mm、5.0mm、5.2mm、5.4mm、5.6mm、5.8mm或 6.0mm,但并不仅限于所列举的数值,该数值范围内其他未列举的数值同样适用。 优选地,所述的条形板材两端的对接处保留6~10mm的缺口,例如可以是6.0mm、 6.2mm、6.4mm、6.6mm、6.8mm、7.0mm、7.2mm、7.4mm、7.6mm、7.8mm、8.0mm、8.2mm、8.4mm、 8.6mm、8.8mm、9.0mm、9.2mm、9.4mm、9.6mm、9.8mm或10.0mm,但并不仅限于所列举的数值,该 数值范围内其他未列举的数值同样适用。 作为本发明一种优选的技术方案,所述的环件本体的外侧环面上设置有5~7个配 合孔,例如可以是5个、6个或7个。 优选地,缺口两侧的环件本体外侧环面上分别设置一个端配合孔,环件本体外侧 环面上两个端配合孔之间的区域上等距设置有3~5个的主体配合孔,例如可以是3个、4个 5 CN 111575663 A 说 明 书 3/8 页 或5个。 优选地,以缺口一侧的端配合孔和环件本体中心连线为旋转基线,沿同一方向每 旋转55~85°在环件本体的外侧环面上加工形成一个主体配合孔,例如可以是55°、60°、 65°、70°、75°、80°或85°,但并不仅限于所列举的数值,该数值范围内其他未列举的数值同 样适用。 优选的,端配合孔与其相邻的主体配合孔之间的圆周距离等于相邻的两个主体配 合孔之间的圆周距离。 优选地,两个端配合孔与环件本体中心连线所成圆心角为20~30°,例如可以是 20°、21°、22°、23°、24°、25°、26°、27°、28°、29°或30°,但并不仅限于所列举的数值,该数值 范围内其他未列举的数值同样适用。 需要说明的是,旋转角度需要根据主体配合孔的数量确定,要保证对环件本体外 侧环面上两个端配合孔之间的环形区域进行等分,再结合两个端配合孔与环件本体中心连 线所成圆心角即可算出旋转角度。以设置5个配合孔为例,除去两个端配合孔,还需要在环 件本体外侧面上设置三个主体配合孔,这三个主体配合孔要将环件本体外侧环面上两个端 配合孔之间的环形区域进行等分,若两个端配合孔与环件本体中心连线所成圆心角为20°, 旋转角度的计算过程为:(360°-20°)/4=85°,换言之,在实际加工过程中,以第一个加工成 型的端配合孔与环件本体中心连线作为旋转基线,旋转85°加工成型第一个主体配合孔,沿 同一旋转方向再旋转85°加工第二个主体配合孔,依次类推直至旋转到主体环件缺口的另 一侧加工成型第二个段配合孔,完成全部配合孔的加工过程。 可以理解的是,以此类推,两个端配合孔与环件本体中心连线所成圆心角确定为 20°时,若要加工6个配合孔,旋转角度为:(360°-20°)/5=68°;若要加工7个配合孔,旋转角 度为:(360°-20°)/6=56.7°。两个端配合孔与环件本体中心连线所成圆心角确定为30°时, 若要加工5个配合孔,旋转角度为:(360°-20°)/4=82.5°;若要加工6个配合孔,旋转角度 为:(360°-20°)/5=66°;若要加工7个配合孔,旋转角度为:(360°-20°)/6=55°。 作为本发明一种优选的技术方案,所述的环件本体的外表面设置有花纹。 优选地,所述的花纹呈倒锥形凹坑状。 第二方面,本发明提供了一种如第一方面所述的磁控溅射环件的配合孔的加工方 法,所述的配合孔的加工方法包括: 采用四轴加工方法在环件本体的外侧环面加工出至少一个配合孔。 作为本发明一种优选的技术方案,所述的配合孔的加工方法具体包括如下步骤: (Ⅰ)将环件本体竖直装夹在四轴加工中心的分度工作台上,刀具下移加工形成配 合孔,加工完成后刀具上移脱离加工面; (Ⅱ)分度工作台外移,分度工作台的齿盘脱离啮合状态,分度工作台旋转预设角 度后复位,齿盘重新啮合定位夹紧,刀具下移加工形成下一个配合孔; (Ⅲ)重复步骤(Ⅱ)直至完成全部配合孔的四轴加工过程。 需要说明的是,配合孔的加工过程是环件本体整个加工环节的最后一步,即在加 工配合孔之前需要先将条形板材卷环加工成两端相接的环件原坯,再在环件原坯的外表面 加工出花纹,最后再进行本发明限定的配合孔的加工过程。至于条形板材的卷环成型以及 花纹的加工过程均不属于本发明的保护范围,本领域技术人员可以参考现有技术中已公开 6 CN 111575663 A 说 明 书 4/8 页 的加工工艺,本发明对此不作具体要求和特殊限定。示例性地,本发明提供了钽条板材的卷 环加工方法,具体包括如下步骤: (1)提供高纯钽锭;(2)对高纯钽锭进行加工形成钽条;(3)对钽条进行整平处理; (4)对钽条进行切割形成钽条板材;(5)对钽条板材进行热处理;(6)对钽条板材进行卷环处 理使钽条板材的两端首尾对接形成钽环原坯。 本发明的主要发明点在于,使用四轴加工中心对环件本体配合孔进行加工,由于 现有加工方案需要操作人员手动旋转环件本体,不仅劳动强度大,且有摇错风险,不适合大 批量生产。本发明采用先进的四轴加工替代传统的手动分度旋转,从而实现了对旋转角度 的精确控制,有效降低了摇错风险和操作人员的劳动强度。 需要说明的是,四轴加工为本领域技术人员所公知的一种加工手段,市面比较常 见的是三轴加工,其具有X轴、Y轴和Z轴三个线性位移轴,所谓的四轴加工一般是在三轴加 工的基础上增加了一个旋转轴,通常称为第四轴。相应的加工中心就是四轴加工中心。也正 是依托第四轴的旋转运动实现了本发明对环件本体外侧环面的周向加工目的。 此外,本发明对四轴加工中心的具体结构不作具体要求和特殊限定,现有的四轴 加工中心均可用于对环件本体的配合孔进行加工。常用的四轴加工中心包括数控机床以及 与数控机床配合使用的分度工作台,分度工作台主要完成旋转运动,目前常用的分度工作 台为鼠牙盘式分度工作台,鼠牙盘式分度工作台由工作台面、底座、压紧液压缸、鼠牙盘、伺 服电动机、同步带轮和齿轮转动装置等零件组成,鼠牙盘是保证分度精度的关键零件,每个 齿盘的端面带有数目相同的三角形齿,当两个齿盘啮合时,能够自动确定轴向和径向的相 对位置。 数控机床需要分度工作时,数控装置发出指令,电磁铁控制液压阀,使压力油经油 孔进入到工作台中央的夹紧液压缸下腔,推动活塞向上移动,经推力轴承将工作台抬起,上 下两个鼠牙轮盘脱离啮合,与此同时,在工作台向上移动过程中带动内齿轮向上套入齿轮, 完成分度前的准备工作。 当工作台上升时,推杆在弹簧力的作用下向上移动使推杆能在弹簧力的作用下向 右移动,离开微动开关,使微动开关复位,控制电磁阀使压力油经油孔进入分度油缸左腔, 推动齿条活塞向右移动,带动与齿条相啮合的齿轮沿逆时针方向转动。由于齿轮已经与内 齿轮相啮合,所以分度工作台也将随之转过相应的角度。回转角度的近似值将由微动开关 和挡块控制,开始回转时,挡块离开推杆使微动开关复位,通过电路互锁,始终保持工作台 处于上升位置。 当工作台转到预定位置附近,挡块通过推杆使微动开关工作。控制电磁阀开启使 压力油经油孔进入到压紧液压缸上腔,活塞带动工作台下降,上鼠牙盘与下鼠牙盘在新的 位置重新啮合,并定位压紧。夹紧液压缸下腔的回油经节流阀可限制工作台的下降速度,使 上下鼠牙盘平稳啮合,保持齿面不受冲击。 当分度工作台下降时,通过推杆的作用启动微动开关,分度液压缸右腔通过油孔 进压力油,齿条活塞退回。带动齿轮沿顺时针方向转动时,挡块回到原处为下一次分度工作 做好准备。此时内齿轮已同齿轮脱开,工作台保持静止状态。 总结以上鼠牙盘式分度工作台作分度运动,其具体工作过程可分为以下三个步 骤: 7 CN 111575663 A 说 明 书 5/8 页 (1)分度工作台抬起:数控装置发出分度指令,工作台中央的压紧液压缸下腔通过 油孔进压力油,活塞向上移动,通过钢球将分度工作台抬起,两齿盘脱开,抬起开关发出抬 起完成信号。 (2)工作台回转分度:当数控装置接收到工作台抬起完成信号后,立即发出指令让 伺服电动机旋转,通过同步齿形带及齿轮带动工作台旋转分度,直到工作台完成指令规定 的旋转角度后,电动机停止旋转。 (3)分度工作台下降定位夹紧:当工作台旋转到位后,指令控制液压电磁阀换向使 压紧液压缸上腔通过油孔进入压力油。活塞带动工作台下降,鼠牙盘在新的位置重新啮合, 并定位夹紧。夹紧开关发出夹紧完成信号。液压缸下腔的回油经过节流阀,以限制工作台下 降的速度。保护齿面不受冲击。 需要说明的是,以上工艺流程仅为帮助本领域技术人员理解四轴加工过程的示例 性描述内容,不作为对本发明的具体限定,进一步强调的是,本发明的主要发明点在于,采 用四轴加工中心对环件本体的配合孔进行加工,至于四轴加工中心本身如何运行如何操控 不属于本发明的保护范围。 作为本发明一种优选的技术方案,步骤(Ⅰ)中,刀具对准环件本体缺口一侧的外侧 环面,加工形成第一个端配合孔。 优选地,步骤(Ⅱ)中,沿环件本体外侧环面,分度工作台旋转55~85°加工形成第 一个主体配合孔。 优选地,在步骤(Ⅲ)中,沿同一方向等角度旋转逐一加工形成所有的主体配合孔, 分度工作台旋转一周后,刀具位于环件本体缺口另一侧的外侧环面上方,刀具下移加工形 成第二个端配合孔,至此完成全部配合孔的四轴加工过程。 优选地,所述的配合孔为盲孔。 优选地,所述的配合孔的加工深度为1.2~1.5mm。 需要说明的是,在本发明中首个加工形成的配合孔可以是端配合孔也可以是某个 主体配合孔,只要控制分度工作台的旋转角度,确保旋转和定位准确,配合孔的加工顺序没 有具体限定和特殊要求。 与现有技术相比,本发明的有益效果为: 使用四轴加工中心对环件本体配合孔进行加工,由于现有加工方案需要操作人员 手动旋转环件本体,不仅劳动强度大,且有摇错风险,不适合大批量生产。本发明采用先进 的四轴加工替代传统的手动分度旋转,从而实现了对旋转角度的精确控制,有效降低了摇 错风险和操作人员的劳动强度。 附图说明 图1为本发明一个