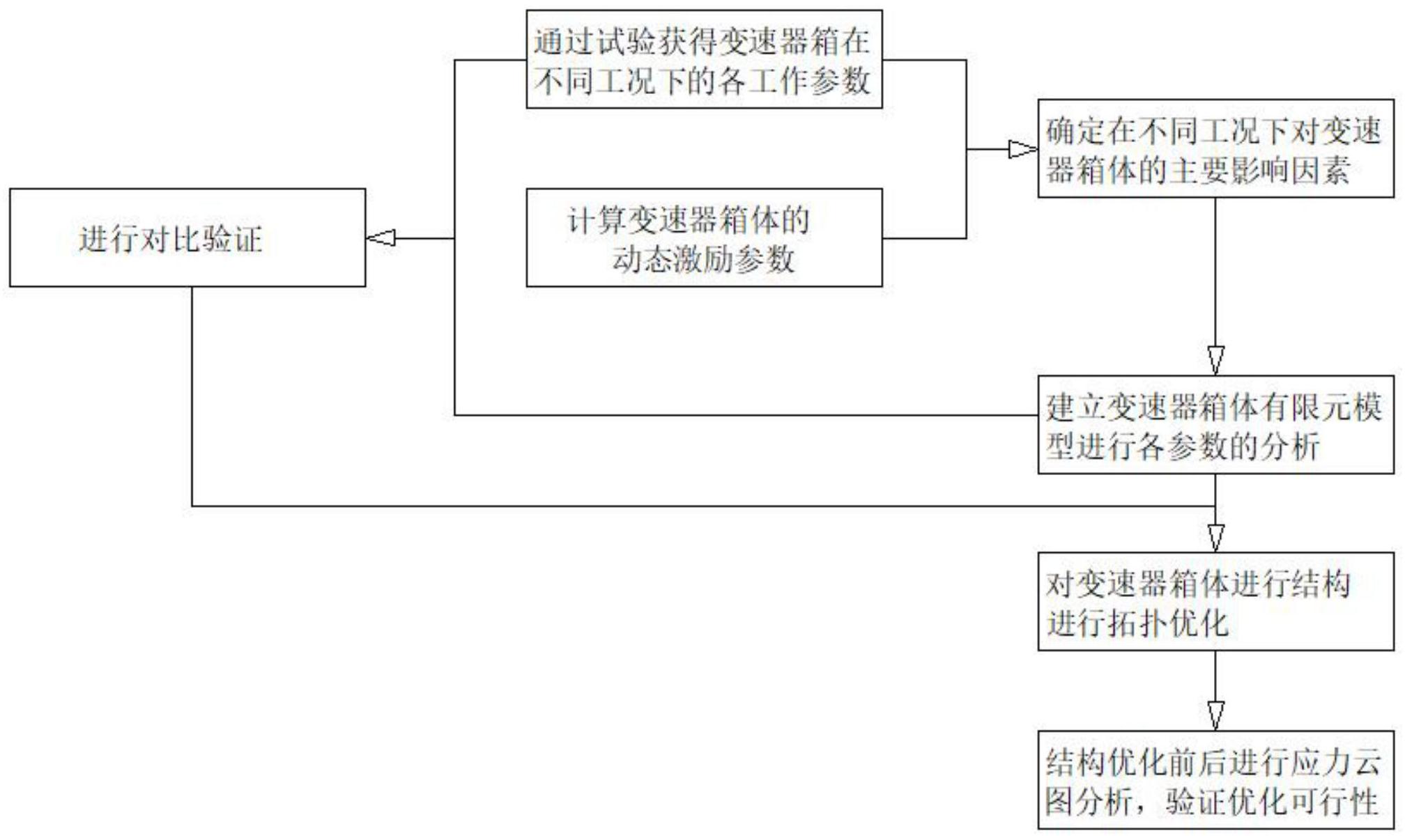
技术摘要:
本发明公开了一种变速器箱体轻量化优化方法,包括如下步骤:S1通过试验获得变速器箱在不同工况下的各工作参数;S2计算变速器箱体的动态激励参数;S3对步骤S1和步骤S2进行分析,确定在不同工况下对变速器箱体的主要影响因素;S4根据步骤S3中的分析结果建立变速器箱体有 全部
背景技术:
变速器箱体作为安装、保护齿轮传动的机构,是保证各档位齿轮传动精度的基础, 在变速器工作过程中,箱体因齿轮传动承受较大的载荷,可能产生较大的变形和应力,如果 变速器箱体的刚强度不足,导致箱体产生裂纹或变形,这会造成齿轮和轴的安装误差,再加 上齿轮和轴受载变形,破坏了齿轮理论上正确的啮合条件,降低了齿轮传动精度,引起齿轮 传动系统的振动、冲击和噪声、齿轮的过早疲劳破坏,导致整个变速器的性能下降。 齿轮传动故障在振动信号上表现为幅值调制和频率调制现象,不同的故障在频谱 上会有不同的表现。为了避免上述问题,在变速器设计时常常通过加大变速器箱体的厚度 来提高其刚强度,但同时也加大了变速器的自重,进而增加了汽车重量,影响汽车的动力性 和经济性,因此设计合适的变速器箱体至关重要;但是传统的变速箱设计过程耗时长、效率 低。
技术实现要素:
本发明的目的是提供一种变速器箱体轻量化优化方法,可以解决上述技术问题中 的一个或是多个。 为了达到上述目的,本发明提出的技术方案如下: 一种变速器箱体轻量化优化方法,包括如下步骤: S1通过试验获得变速器箱在不同工况下的各工作参数; S2计算变速器箱体的动态激励参数; S3对步骤S1和步骤S2进行分析,确定在不同工况下对变速器箱体的主要影响因 素; S4根据步骤S3中的分析结果建立变速器箱体有限元模型进行各参数的分析; S5再根据S1步骤中的试验结果,对步骤S4中的有限元模型进行对比验证; S6对步骤S4中的有限元模型进行拓扑优化模型,进而根据该优化模型对变速器箱 体进行结构优化。 优选的:步骤S1中包括如下步骤:将变速器箱体安装在“电功率封闭式机械传动系 统综合试验台”上,在变速器箱体上的不同位置贴有传感器,通过各传感器获得箱体在不同 工况下的温度参数、振动加速度参数、输入轴转速参数和扭矩测量参数、输出轴的转速参数 和扭矩测量参数。 优选的:步骤S2中所述变速器箱体的动态激励参数为振动的激励力,其主要由齿 轮动态刚度激励和齿轮误差激励组成。 优选的:根据步骤S3中和步骤3的结果获知引起齿轮故障的主要影响因素:齿轮轴 工作频率、啮合频率以及谐波频率和边频的特征;因此需要计算变速器齿轮箱的各主要特 4 CN 111611732 A 说 明 书 2/10 页 征频率。 优选的:步骤S4的步骤是应用三维软件Solidworks建立变速器箱体的三维模型; 应用Hypermesh软件对变速器箱体的三维模型进行网格划分,最后应用Abaqus有限元软件 进行各参数的分析。 优选的:步骤S5的步骤如下:抽取步骤S1中任意一段时间内所对应的步骤S4中的 仿真结果做对比验证。 优选的:步骤S6中拓扑优化目标函数的数学模型为: min.C(ρ)=UTKU s.t.K(ρ)U(ρ)≤F 0<ρmin≤ρe≤1 (1) 其中,ρ=[ρ1 ,ρ2,…,ρn]T是有限元离散的单元的当量密度(即设计变量);K(ρ)为 结构的整体刚度矩阵;U(ρ)和F分别为有限元位移和载荷(假定载荷同设计变量无关);Ve和 V分别为单元体积和目标体积;ρmin是为防止0密度造成总体刚度矩阵奇异而设定的密度下 限,一般取为0.001。 优选的:为了获得设计变量的更新方向,需要求目标及约束关于设计变量的偏导 数—即灵敏度;具体过程如下: 对目标函数的偏导数,有: 由平衡方程KU=F,得到(F独立于设计变量): 联立(2)和(3)两个式子可得到目标函数的灵敏度: 其中,ue和ke是单元e对应的位移响应和单元刚度矩阵; 结合(1)式,可以得到结构总柔度的灵敏度: 体积约束的灵敏度: 优选的:步骤S6中的结构优化式通过ABAQUS仿真软件进行计算获得的。 本发明的技术效果是: 5 CN 111611732 A 说 明 书 3/10 页 本发明中主要通过仿真软件进行拓扑优化,采用仿真软件的过程中简化了计算过 程,整体计算量小,再结合试验的方式进行对仿真优化结果进行验证,降低设计周期;使变 速器箱体的结构更加合理,性能得到提高。 附图说明 构成本申请的一部分的说明书附图用来提供对本发明的进一步理解,本发明的示 意性实施例及其说明用于解释本发明,并不构成对本发明的不当限定。 在附图中: 图1变速器动态测试平台示意图; 图2测试系统框图; 图3变速器箱体振动测试现场 图4轮齿载荷变化示意图; 图5齿轮振动模型示意图; 图6是2号测点振动加速度及频谱图; 图7是3号测点振动加速度及频谱图; 图8是4号测点振动加速度及频谱图; 图9是在三维软件中建立的变速器箱体初始几何模型; 图10是图9在导入仿真软件中的网格划分示意图; 图11是变速器箱体在仿真软件中的前五阶振型云图; 图12是变速器箱体有限元模型及传感器布置示意图; 图13是在试验平台上的0.4s内的加速度及频谱图; 图14是仿真软件中得到的加速度及频谱图; 图15是变速器箱体结构拓扑优化设计流程图; 图16是变速器箱体的刚度法优化后箱体材料分布云图; 图17图16的去除单元后箱体网格模型图; 图18是变速器箱体改进前后对比示意图; 图19是结构改进之后三档下箱体应力云图和位移云图; 图20是改进结构后箱体第一阶和第二阶振型图; 图21是改进前三档箱体应力云图; 图22是改进前三档下箱位移云图; 图23本发明的工作流程示意图。