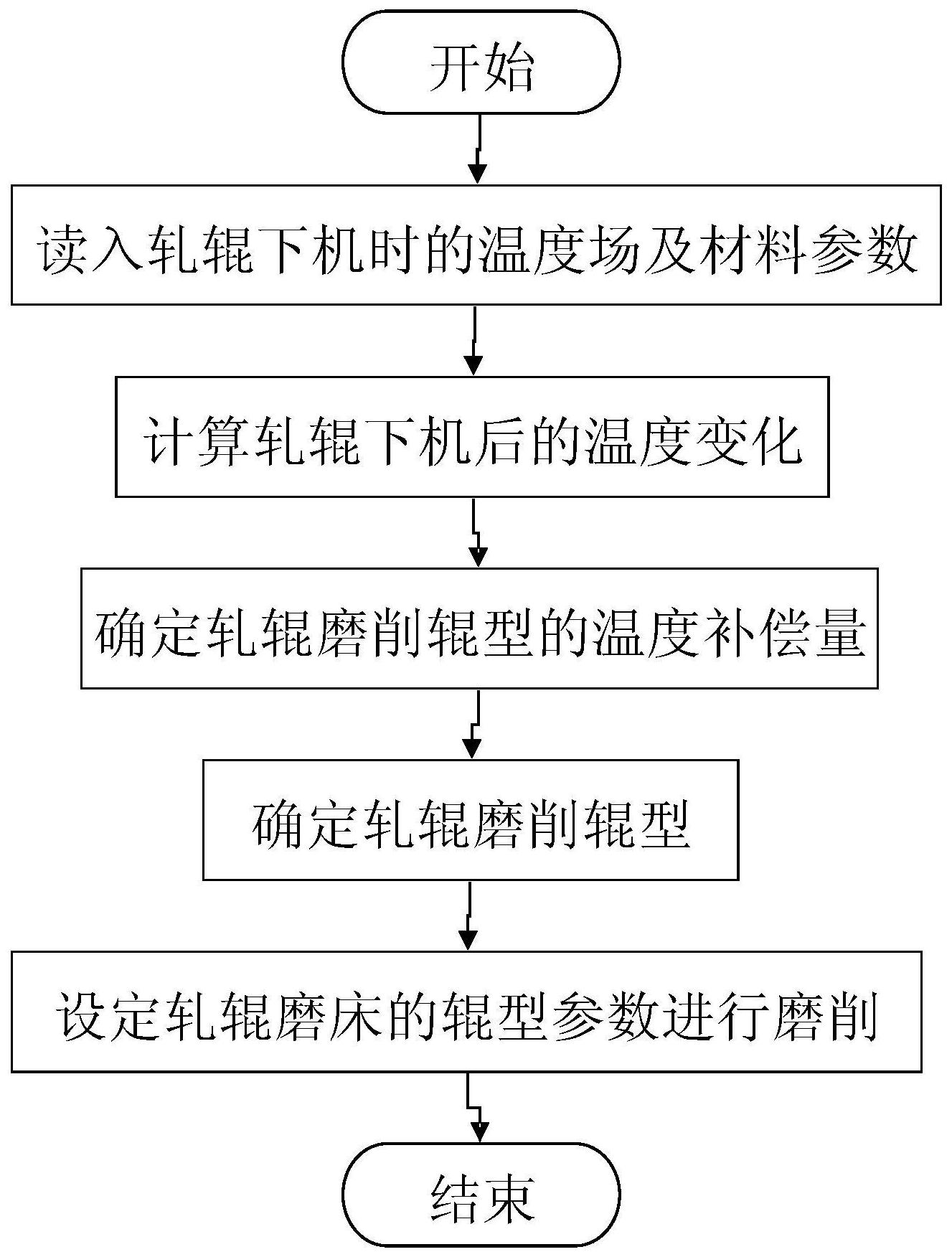
技术摘要:
本发明公开了一种轧辊辊型的磨削控制方法,包括如下步骤:步骤1:通过在线计算机模型读入下机时刻的轧辊的温度场及物性参数;步骤2:根据离线轧辊的冷却边界条件,计算温度场的动态变化;步骤3:确定轧辊磨削辊型的温度补偿量;步骤4:确定轧辊的磨削辊型,设定目标初 全部
背景技术:
轧辊是热轧板带轧机的重要部件,包括辊身1、辊肩2和辊颈3,如附图1所示。在轧 制过程中,轧辊表面会产生磨损。为了保证带钢产品的板形与表面质量,在轧制一定公里数 后,轧辊需要卸下重新磨削。 为了保证初始辊型的准确性,被磨削的轧辊温度需要冷却到室温。然而,为了提高 轧辊周转速度,有时未冷却到室温即进行重磨。此时由于存在热膨胀,磨削辊型会有偏差, 这将导致上机使用中辊缝形状设定不准确,从而影响热轧带钢板形质量控制,造成浪形缺 陷和凸度超差。 日本专利申请JP11005106A公开了一种轧辊磨削方法,涉及沿轧辊长度方向温度 不均匀分布的磨削辊型补偿方法。在该发明中,轧辊表面温度采用传感器测量,并实时反馈 给磨辊控制系统,以考虑温度影响对磨削辊型进行补偿。但轧辊热膨胀是由轧辊整体的温 度分布决定的,该方法只能测量轧辊表面温度,内部温度分布无法准确知道,因此不能就温 度的影响对磨削辊型作出准确补偿。
技术实现要素:
本发明的目的在于提供一种轧辊辊型的磨削控制方法,能通过磨削时轧辊的温度 场和热膨胀情况修正磨削目标辊型,从而保证轧辊辊型的正确磨削。 本发明是这样实现的: 一种轧辊辊型的磨削控制方法,包括如下步骤: 步骤1:通过在线计算机模型读入下机时刻的轧辊的温度场及物性参数; 步骤2:根据离线轧辊的冷却边界条件,计算温度场的动态变化; 步骤3:确定轧辊磨削辊型的温度补偿量; 步骤3.1:计算轧辊热膨胀量,轧辊辊身表面任一点z处的热膨胀量为: 其中,ν为泊松比,β为热膨胀系数,R为轧辊半径,T0为初始温度,T为温度,r为轧辊 径向坐标,z为轧辊轴向坐标; 步骤3.2:计算轧辊相对膨胀量,轧辊辊身表面任一点z处的相对膨胀量为: △ut(z)=ut(z)-ut(e) (8) 其中,ut(e)为轧辊边部代表点e处的热膨胀量; 步骤3.3:拟合相对膨胀量,计算轧辊辊身表面任一点z处的辊型磨削补偿量: △ut(z)=a0 a2z2 a z44 (9) 其中,a0、a2和a4为拟合系数; 4 CN 111716250 A 说 明 书 2/5 页 步骤4:确定轧辊的磨削辊型,设定目标初始辊型为u0(z),计算带温磨削时的温度 补偿量,计算修正后的磨削辊型: u(z)=u0(z) △ut(z) (10); 步骤5:在数控轧辊磨床中设定轧辊磨削的辊型参数,并对轧辊进行磨削。 在所述的步骤1中,轧辊的物性参数包括密度、比热和热传导率。 在所述的步骤2中,温度场的动态变化的计算公式如下: 其中,T为温度,t为时间,ρ为轧辊材料的密度,c为轧辊材料的比热,λ为轧辊材料 的热传导率,r和z分别为轧辊径向和轴向坐标。 在所述的步骤2中,轧辊冷却过程包括强制冷却前的空冷、强制喷水冷却和强制冷 却之后的空冷。 所述的轧辊冷却过程中的冷却边界条件包括左右对称边界、上下对称边界、辊身 和辊径的表面边界、轧辊与轴承接触部位边界及轧辊端部边界。 所述的轧辊左右对称边界的计算公式如下: 其中,T为温度,λ为轧辊材料的热传导率,z为轧辊轴向坐标。 所述的轧辊上下对称边界的计算公式如下: 其中,T为温度,λ为轧辊材料的热传导率,r为轧辊径向坐标。 所述的辊身、辊径的表面边界的计算公式如下: 其中,T为温度,λ为轧辊材料的热传导率,r为轧辊径向坐标,αA为轧辊与空气间的 换热系数,TA为空气温度。 所述的轧辊与轴承接触部位边界的计算公式如下: 其中,T为温度,λ为轧辊材料的热传导率,r为轧辊径向坐标,αB为轧辊与轴承间的 换热系数,TB为轴承温度。 所述的轧辊端部边界的计算公式如下: 其中,T为温度,λ为轧辊材料的热传导率,z为轧辊轴向坐标,αA为轧辊与空气间的 换热系数,TA为空气温度。 本发明与现有技术相比,具有如下有益效果: 5 CN 111716250 A 说 明 书 3/5 页 1、本发明能通过磨削时轧辊的温度场和热膨胀情况修正磨削目标辊型,减小上机 生产设定偏差,实现轧辊磨削辊型的设定,从而保证轧辊辊型的正确磨削,提高热轧板形设 定精度和板形质量。 2、本发明适用于热轧板带生产中轧辊下机后在空气中缓慢冷却14小时以内再进 行重磨情况,也适用于下机后经过喷水冷却20~120分钟再进行重磨的情况,推广应用前景 广阔。 附图说明 图1是现有技术的轧辊的主视图; 图2是本发明轧辊辊型的磨削控制方法的流程图; 图3是本发明轧辊辊型的磨削控制方法的轧辊有限差分网格示意图; 图4是本发明轧辊辊型的磨削控制方法的实施例1的轧辊相对热膨胀量的变化图。