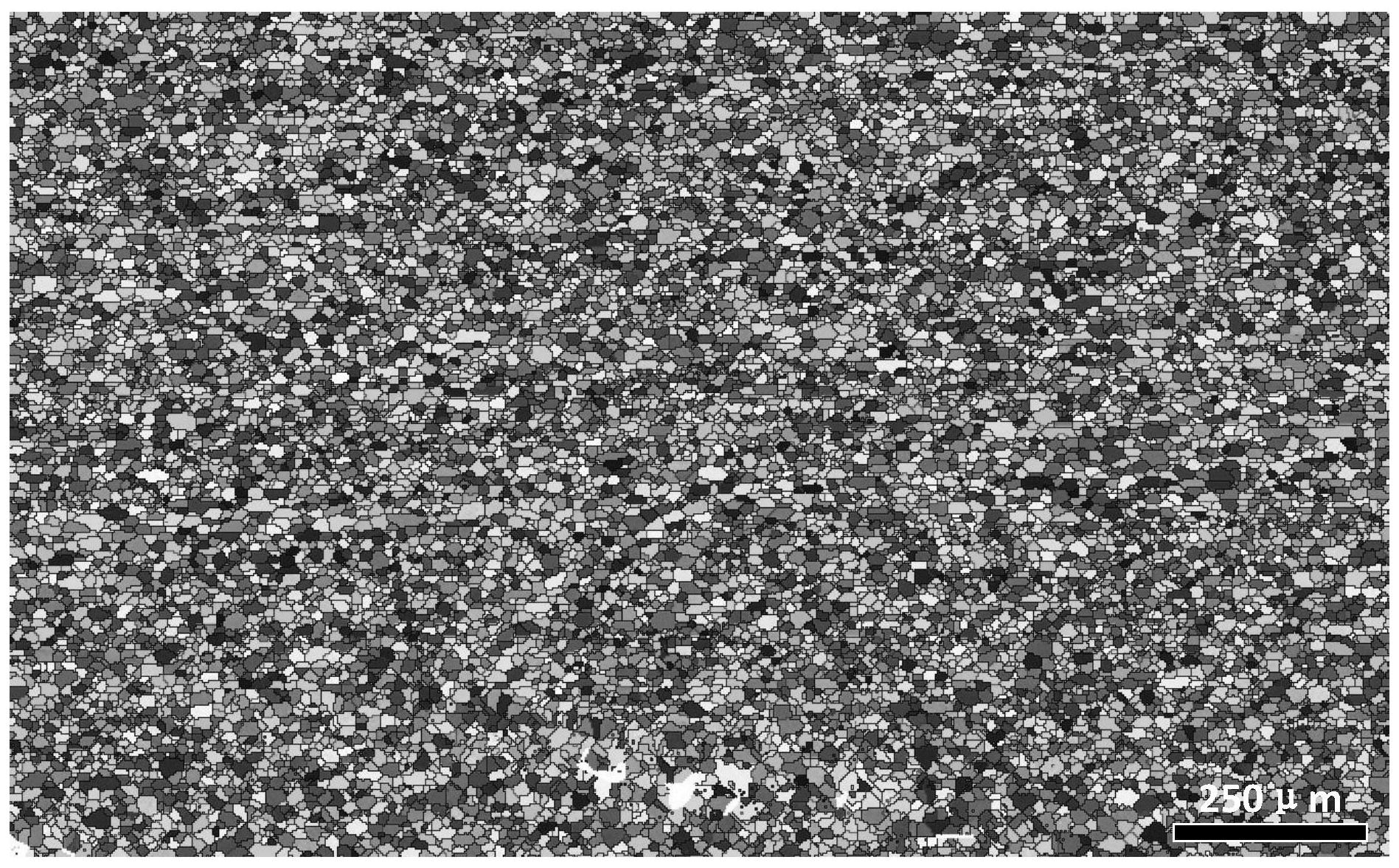
技术摘要:
本发明公布一种车身结构用低成本高成形性铝合金板材及其制备方法,属于铝合金技术领域。其可利用回收铝或普铝配制Al‑Zn‑Mg‑Cu‑Fe系合金,在非真空下利用中频感应熔炼合金,并将其浇铸在水冷钢模内冷却;对铸锭进行一定时间的低温热处理,然后一定温下热轧;短时均 全部
背景技术:
随着汽车数量的增加,能源消耗和空气污染已引起全球各国的重视。而汽车轻量 化是解决上述问题的有效途径之一。铝合金由于质轻、耐蚀、比强度高、易加工、表面美观、 储量丰富以及可回收循环利用等特性,已成为汽车轻量化的关键材料。此外,据统计在汽车 中采用铝合金所节省的能量是生产该零件所用原铝耗能的6~12倍。因此,汽车轻量化用先 进铝合金板材的开发和应用已经引起全球汽车生产厂家以及科研人员的广泛重视,而且近 几年汽车用铝量也在逐年增加。 除铸造铝合金之外,汽车轻量化更为重要的是变形铝合金的开发和应用。由于系 列铝合金的性能差异,其在车身上的应用也有重大差异。5xxx系铝合金由于成形性能好,普 遍应用于车身内板的制造,而6xxx系铝合金由于成形性能和烤漆硬化增量均较好,普遍应 用于车身外板的制造。随着应用的不断深入,近期研究和应用过程中发现,如果车身结构件 仍然使用钢板制造,车身外板铝合金与钢结构件连接会存在较多问题,如钢铝焊接难,应力 腐蚀等问题。因此,以往主要应用于航空领域的7xxx系铝合金开始被关注,并期望能够广泛 应用于车身结构件的制造,从而更好解决上述钢铝连接等问题。但是高强度7xxx系铝合金 普遍存在成本高、冲压成形性能较差等问题,这是制约其在车身结构件上广泛应用的关键。 近期,已有大量研究表明,热成形或温成形均可促进该系合金板材的成形性能,但是成形工 艺复杂,生产成本较高,而且温、热成形时很容易影响沉淀相的分布进而使得合金板材强度 降低,这非常不利于该系合金在车身结构件上的广泛应用。由此可见,为了更好满足实际应 用需求,急需充分利用回收铝或普铝熔铸合金并结合进一步的成分设计优化以及热加工工 艺对合金组织演化进行调控,进而在保证大幅降低其生产成本的同时,也能保证其室温冲 压成形性能优异,只有这样才能快速推进其在汽车车身结构件上的广泛应用,同时对于加 快汽车轻量化进程也具有重要促进作用。
技术实现要素:
为了更好满足车身结构件对低成本、高强、高成形性Al-Zn-Mg-Cu系合金的迫切需 求,同时为了解决该系合金板材传统热加工工艺复杂,生产成本高,以及所生产的合金板材 室温冲压成形性能较低等问题,本发明提出一种车身结构用低成本高强高成形性Al-Zn- Mg-Cu-Fe系铝合金板材及其制备方法。 一种车身结构用低成本高成形性铝合金板材,其特征在于,所述车身结构用低成 本高强高成形性铝合金为Al-Zn-Mg-Cu-Fe系合金,化学成分及其质量百分比含量为:Zn: 4 CN 111593239 A 说 明 书 2/13 页 4 .5~6 .8wt%,Mg:1 .0~2 .2wt%,Cu:1 .0~2 .2wt%,Fe:0 .15~0 .7wt%,Mn:0 .05~ 0.3wt%,Ni:0.01~0.06wt%,Ti:0.05~0.2wt%,B<0.01wt%,Si<0.01wt%,余量为Al。 优选的,所述Al-Zn-Mg-Cu-Fe系合金化学成分及其质量百分比含量为:Zn:4.6~ 6.0wt%,Mg:1.0~2.0wt%,Cu:1.5~2.2wt%,Fe:0.2~0.7wt%,Mn:0.08~0.3wt%,Ni: 0.03~0.06wt%,Ti:0.08~0.2wt%,B<0.01wt%,Si<0.01wt%,余量为Al。 如上所述一种车身结构用低成本高成形性铝合金板材的制备方法,所述制备方法 具体包括: (1)利用回收铝或普铝配制汽车用低成本高强高成形性Al-Zn-Mg-Cu-Fe系合金, 然后在非真空下利用中频感应熔炼合金,并将其浇铸在水冷钢模具内,控制冷却速率大于 50℃/min使得合金晶粒尺寸和原生富铁相分布满足后续调控要求; (2)根据铸态组织,对铸锭进行低温预热处理,温度低于420℃,升温速率低于20 ℃/min,然后将低温预热处理的铸锭进一步快速升温至430~460℃,升温速率大于20℃/ min,然后对其进行热轧变形处理,热轧变形量70~96%; (3)随后对热轧板材进行单级热处理调控合金沉淀相、溶质元素以及原生富铁相 分布状态,热处理温度450~490℃; (4)随后对首次热轧变形量小于90%的均匀化态板材进行二次热轧变形处理,直 接将合金板材置于430~460℃热处理炉中保温10~40min,然后对其进行热轧变形,热轧变 形量22~70%; (5)随后顺序进行一定量一次冷轧变形 中间退火处理 二次冷轧处理,使得合金 基体内原生富铁相呈均匀弥散和多尺度分布特征; (6)高温短时固溶处理,固溶温度450~480℃,随后将固溶处理后的合金试样从固 溶处理温度淬火冷却到室温; (7)将淬火态试样在1min内转移到时效炉内进行双级等温预时效处理,第一级温 度90~140℃,第二级温度150~185℃。 优选的,步骤(1)中,在非真空下利用中频感应熔炼合金工艺为:首先将回收铝或 普铝全部加入坩埚并熔化,温度控制在780~880℃,然后分别添加Al-20wt%Fe,Al-10wt% Mn,Al-10wt%Ti中间合金,待熔化后再添加Al-50wt%Cu中间合金,然后大功率搅拌熔体 10min,随后再添加所需含量的纯Ni到熔体内并用大功率搅拌熔体10min,然后将合金熔体 温度控制在720℃以上,分别添加纯Zn和纯Mg,添加纯Mg时用石墨钟罩将其压入熔体底部, 待其彻底溶化后取出钟罩,调控中频感应炉功率使合金熔体温度重新稳定在740℃后扒渣、 加入精炼剂进行除气精炼;然后将熔体温度降至720℃时加入Al-5wt%Ti-1wt%B晶粒细化 剂并进行适当搅拌,最后在此温度720℃保温10min后将熔体浇铸到四周水冷的钢模内,控 制冷却速率大于60℃/min。 优选的,步骤(2)中,对铸锭进行低温预热处理,温度低于410℃,保温时间0.5~ 2h,升温速率低于20℃/min,然后将低温预热处理的铸锭进一步快速升温至430~450℃,升 温速率大于30℃/min,然后对其进行热轧变形处理,热轧变形量70~96%,道次压下量:5~ 15%,终轧温度:低于300℃,轧制方式:单向轧制。 优选的,步骤(3)中,对热轧板材进行单级热处理调控合金沉淀相、溶质元素以及 原生富铁相分布状态,热处理温度450~485℃,热处理时间:5~17h,升温速率大于100℃/ 5 CN 111593239 A 说 明 书 3/13 页 min,冷却速率大于100℃/min。 优选的,步骤(4)中,对首次热轧变形量小于90%的均匀化态板材进行二次热轧变 形处理,直接将合金板材置于430~450℃热处理炉中保温10~40min,然后对其进行热轧变 形,热轧变形量22~62%,道次压下量:16~40%,终轧温度:低于300℃,轧制方式:单向轧 制。 优选的,步骤(5)中,顺序进行一定量一次冷轧变形 中间退火处理 二次冷轧处理 具体包括:一次冷轧处理:变形量为40-55%,道次压下量:15~35%;中间退火工艺为:380- 440℃/0.5h-3h;二次冷轧处理:冷轧变形量为40-55%,道次压下量:20~35%。 优选的,步骤(6)中,高温短时固溶处理具体包括:455~480℃/3-15min,随后将固 溶处理后的合金试样从固溶处理温度淬火冷却到室温,冷却速率大于150℃/s。 优选的,步骤(7)中,将淬火态试样在1min内转移到时效炉内进行双级等温预时效 处理,温度90~130℃,时间0.5~3h,第二级温度150~185℃,时间1~20min。 本发明充分利用回收铝或普铝普遍含有溶质元素Fe,其可以与主合金元素Cu相互 作用形成AlFeCu或AlCuFe原生富铁相。由于其在热加工过程中会发生破碎,调控合理还可 以形成多尺度弥散粒子。这些粒子一旦形成合理搭配的多尺度和弥散分布特征,其不仅在 热加工过程中可以有效弱化织构,降低板材的各向异性,促进成形性能提高,而且在高温热 处理时粗大粒子还可以诱发再结晶形核,而细小粒子又可以阻碍再结晶晶粒快速长大,最 终所开发合金板材会具有细晶组织和织构近随机分布的组织特征,室温冲压成形性能可获 得大幅度提高。因此,本发明拟开发新型低成本Al-Zn-Mg-Cu-Fe系合金材料。但是由于原生 富铁相在Al-Zn-Mg-Cu系合金熔铸时很容易发生偏聚粗化,这对后续有效调控其尺寸和分 布极为不利,为此,本发明进一步提出熔铸微合金化和短流程热加工调控新思路以更好避 免上述可能产生的不利影响。首先,熔铸时拟充分引入溶质元素Ni,使其能够有效促进原生 富铁相的形核率,从而达到细化原生相的目的。同时由于Al-Zn-Mg-Cu系合金均匀化温度不 能太高,即使长时间均匀化也不利于熔铸态所形成棒状或网状原生富铁相发生熔断进而球 化,因此,本发明提出首先对该系合金进行合适热轧变形,由于热轧变形不仅可以破碎原生 富铁相,而且还可以增加基体内的应变储能,随后再对合金进行短时均匀化热处理即可有 效促进原生富铁相的熔断和球化。当然,由于熔铸态存在成分偏析,合金的加工性能较差, 如果热轧工艺设计不合理,不仅不能实现上述目的,而且还会使得合金铸锭在热轧时发生 开裂等现象。此外,随着热轧工艺的改变,均匀化之后的冷轧和退火工艺的合理搭配对于更 好调控原生富铁相尺寸和分布也非常关键。本发明优化出了随成分变化,最佳的一体化调 控方法,即,一次热轧变形→均匀化处理→根据一次热轧变形情况进行的二次热轧变形或 直接进行一次冷轧变形→中间退火→二次冷轧变形→固溶淬火处理;同时为了稳定合金自 然放置过程中溶质原子团簇的析出和强度升高,本发明还在固溶淬火之后引入双级等温预 时效调控,第一级预时效为了消耗空位并析出大量溶质原子团簇,第二级预时效为了进一 步消耗空位并溶解部分不稳定溶质原子团簇,从而降低预时效态合金板材的强度。经此工 艺调控后,新型Al-Zn-Mg-Cu-Fe系合金预时效态可表现出优异的室温冲压成形性能和抗自 然时效稳定特性。 本发明所述车身结构用低成本高强高成形性Al-Zn-Mg-Cu-Fe系合金板材应用在 汽车中。 6 CN 111593239 A 说 明 书 4/13 页 本发明的有益效果: 通过采用上述的技术方案,本发明具有如下优越性:本发明不仅可以充分利用回 收铝或普铝熔铸合金,从而降低合金板材的生产成本,而且还通过开发熔铸时的微合金化 调控技术以及新的热加工制备工艺,使得熔铸时形成的原生富铁相发生破碎、球化以及再 破碎等过程,最终实现了能在基体内呈多尺度和均匀弥散分布的组织特征。此种分布特征 可以有效影响合金组织和织构演化,可以使得固溶淬火态织构显著弱化,同时再结晶组织 得到显著细化;然后再辅以预时效调控还可以表现出优异的抗自然时效稳定性和较低的强 度,最终预时效态合金板材可表现出优异的室温冲压成形性能,可用于典型汽车零部件的 室温冲压成形,有效解决了高强度Al-Zn-Mg-Cu系合金成形难等问题。这对于该系铝合金板 材的进一步广泛应用具有重要推动作用。本发明非常适合应用于汽车用铝合金材料的加工 和生产,以及对铝合金板材组织特征以及冲压成形性能等有特定要求的其它铝合金材料生 产企业使用,当然也适合应用于对其它系列铝合金材料组织和综合性能有较高要求的其它 技术行业。 附图说明 图1示出根据本发明的车身结构低成本高强高成形性Al-Zn-Mg-Cu-Fe系合金板材 制备方法流程图; 图2示出实施例3预时效态合金EBSD显微组织; 图3示出实施例4预时效态合金EBSD显微组织; 图4示出实施例5预时效态合金EBSD显微组织; 图5示出实施例6预时效态合金EBSD显微组织; 图6示出实施例7双级预时效调控时显微硬度变化规律。