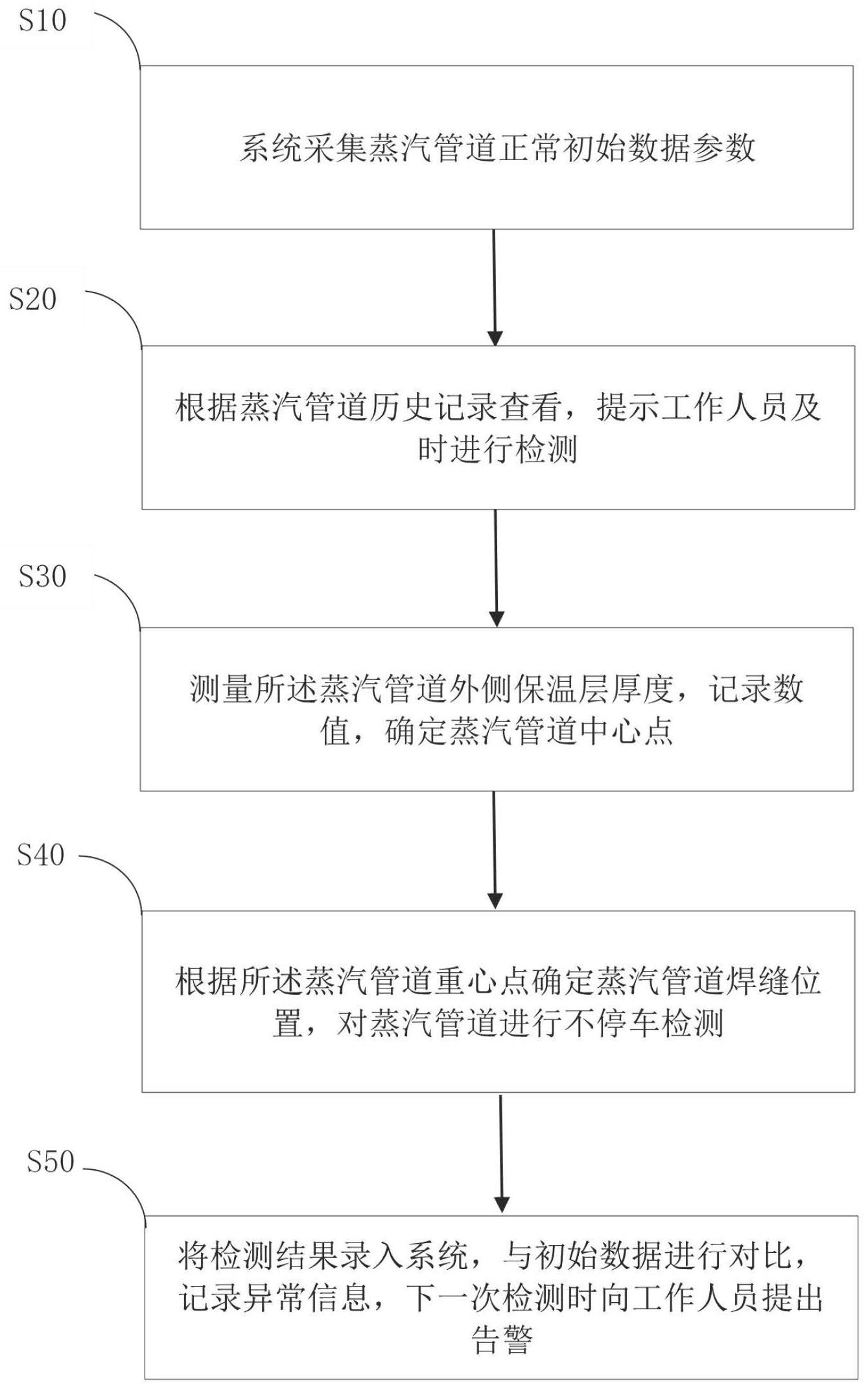
技术摘要:
本发明公开了一种蒸汽管道不停车检测方法,本方法通过对蒸汽管道规格、半径、电压、焦距的初始值进行采集,结合历史检测记录提醒工作人员适时对管道进行检修,检修过程中采用蒸汽管道不停车、不拆除保温层的方法进行管道检修,利用保温层厚度测量钢针对保温层进行测量 全部
背景技术:
在电厂实际生产过程中,生产工作通常置于300°及以上的高温高压工作环境下, 电厂的管道内部会有水、蒸汽、有毒有害气体流通,蒸汽为最常见的管道内部流通物质。 每段管道使用六年必须进行检测一次,目前对管道的检测方法通常为对管道进行 停机处理并拆除外部保温层,进行管道检测,并在检测完成后提供报告对管道后期维护进 行管理,现有管道检测方法存在以下问题: 1、对管道停机进行检查,耽误工作进程,造成损失; 2、保温层的拆除与后期重新安装为检测工作增添许多麻烦; 3、每次检测完成后出具的报告,经过人员流动、时间过长等一些因素缺乏追溯力, 导致工作人员不了解管道情况,做出错误决策; 4、每次的检测报告累积较多时,缺少系统分析,在某一段管道出现问题时,查阅历 史检测记录耗时耗力,无法准确给出提示信息。
技术实现要素:
本发明的目的在于提供一种蒸汽管道不停车检测方法,以解决现有技术中的问 题。 为实现上述目的,本发明提供如下技术方案: 提供一种蒸汽管道不停车检测方法,所述方法的运行步骤包括: 步骤S10,系统采集蒸汽管道正常初始数据参数; 步骤S20,根据蒸汽管道历史记录查看,提示工作人员及时进行检测; 步骤S30,测量所述蒸汽管道外侧保温层厚度,记录数值,确定蒸汽管道中心位置; 步骤S40,根据所述蒸汽管道重心点确定蒸汽管道焊缝位置,对蒸汽管道进行不停 车检测; 步骤S50,将检测结果录入系统,与初始数据进行对比,记录异常信息,下一次检测 时向工作人员提出告警。 进一步地,步骤S10采集到的数据包含不同状态下,所述蒸汽管道的规格、半径、电 压、焦距。 进一步地,步骤S20调用蒸汽管道历史记录,查看所述蒸汽管道的检修频率以及最 近一次检修时间,推算该蒸汽管道是否需要检测,将推算结果反馈到工作显示台,提示工作 人员及时进行检测。 推算蒸汽管道是否需要检测包括: 步骤S201,根据管道使用频率以及使用时间的长短确定蒸汽管道的检修时间间 隔; 4 CN 111595569 A 说 明 书 2/7 页 步骤S202,调用蒸汽管道历史记录,查看管道最近一次检修时间; 步骤S203,管道最近一次检修时间与检修时间间隔相加,确定蒸汽管道是否需要 检测。 优选地,蒸汽管道历史记录包括所述步骤S10中采集到的正常初始数据参数和每 一次管道检测结果; 根据管道的工作环境、管道规格、检测频率和时间推算蒸汽管道是否需要检测,因 此需要通过所述蒸汽管道历史记录判断蒸汽管道是否需要进行检测。 在每一次进行管道检测之前,根据系统提醒和历史查看记录系统检索、查阅该蒸 汽管道的状态,对管道进行目的性检测,提高管道检测效率,在检测前先对管道情况进行预 先了解。 进一步地,步骤S30包括: 步骤S301,利用测量钢针测量保温层周围保温层厚度,记录厚度信息; 步骤S302,根据保温层厚度和已知蒸汽管道外径和壁厚,计算弯头中心至端部的 中心位置; 步骤S303,判断管道弯头是长半径弯头还是短半径弯头以及对应电压、时间、焦距 的数值是否在正常范围内的数值; 优选地,步骤S301中,所述保温层厚度测量钢针为一种尖头螺纹钢针,测量保温层 厚度时,将尖头深入保温层中,根据钢针插入保温层的长度确定保温层厚度; 保温层不同位置厚度存在差别,对保温层厚度进行测量,得到保温层厚度集合为H ={h1,h2,h3,…hn}; 其中 表示测得保温层厚度平均值; 所述步骤S302,测得不同部位、不同规格蒸汽管道弯头的外径,计算弯头外径中间 位置与两侧边缘的距离; 所述步骤S303中长半径弯头指弯头曲率半径等于1.5倍管道外径的弯头,即R= 1.5D,短半径弯头指弯头曲率半径等于管道外径的弯头,即R=D,其中,R为曲率半径,D为管 道外径; 优选地,步骤S302弯头中心位置确定用于定位焊缝位置,根据公式: 其中,C为弯头外径的中间位置与两侧边缘的距离; 所述弯头半径参数值包括长半径参数和短半径参数,根据安装位置不同确定该出 是长半径还是短半径,对电压、时间、焦距参数进行测量。 对正在使用中的管道利用保温层厚度和管径大小进行不停车检测,工作人员可以 根据不同规格的弯头和保温层的厚薄进行焊缝定位,得到准确位置。 进一步地,步骤S40对蒸汽管道进行不停车检测包括: S401,已知弯头外径中间位置与两侧边缘的距离,将弯头两端中间位置进行反向 延长,取交点,该交点对应所述弯头的圆心角,为弯头中心位置点; 5 CN 111595569 A 说 明 书 3/7 页 S402,根据弯头中心位置点分别在横向和纵向与弯头半径参数值相加得到管道焊 缝位置,即以中心位置为原点,分别向管道弯曲两侧移动长半径或短半径距离为焊缝所在 位置; S403,通过焊缝位置准确定位待检测设备位置,进行不停车检测。 优选地,步骤S403对蒸汽管道进行检测,由于弯头参数均为固定值,不同规格弯头 参数值不同,使用过程中管道参数会发生改变,当改变超过一定范围时,应对管道采取技术 措施,保障管道正常安全工作。 进一步地,步骤S50对检测结果与固定参数进行对比分析,发现异常数据,进行系 统记录,对异常数据及时查找问题源并处理记录,对未处理或未发现的异常进行标记,在下 次检测时向工作人员提出告警; 所述告警通过显示屏的方式向工作人员进行展示,同时显示屏内部设有监控措 施,对工作状态下的管道进行实时监控,结合历史记录在固定时间间隔内提醒工作人员对 管道进行检测。 在每一次检测完成后,对历史记录中的数据进行更新分析,为工作人员准确地提 供管道管理方案,并通过提醒告知工作人员下次检修时的工作。 与现有技术相比,本发明的有益效果是: 1、对管道进行不停车检测,正常工作状态下进行检测,节省检测时间; 2、蒸汽管道外侧保温层不进行拆除,对保温层进行检测并根据外径数值确定检测 方位,提高检测效率,减少财力及人工损失; 3、每次检测完成后进行系统记录,所有使用过程中的管道都有对应历史检测记 录,根据历史检测记录对管道状态进行了解和判断; 4、系统可以对每个管道的历史检测记录进行分析,发现管道存在问题,当有问题 出现时,发出告警,及时提醒工作人员对管道进行检修,防止出现因检修不及时导致的损 失。 附图说明 为了使本发明的内容更容易被清楚地理解,下面根据具体实施例并结合附图,对 本发明作进一步详细的说明。 图1为本发明一种蒸汽管道不停车检测方法的方法流程图; 图2为本发明一种蒸汽管道不停车检测方法的步骤S30流程图; 图3为本发明一种蒸汽管道不停车检测方法的步骤S40流程图; 图4为本发明一种蒸汽管道不停车检测方法的管道弯头示意图; 图5为本发明一种蒸汽管道不停车检测方法的测量钢针示意图。