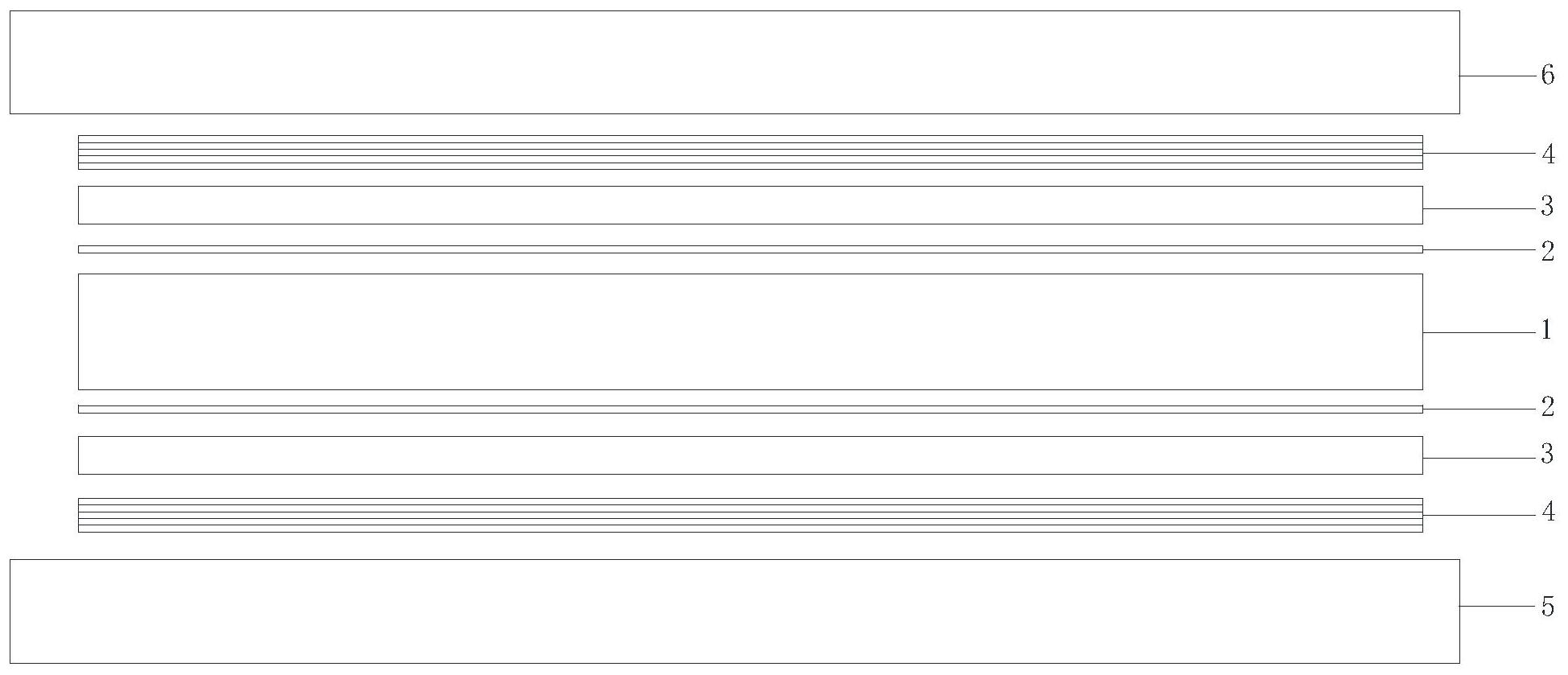
技术摘要:
本发明公开了一种PCB板件的压合叠板方法及压合排板结构,所述压合叠板方法中在对PCB进行压合时,利用PCB上下的钢板对其进行压合,在PCB与上下的钢板之间均设置至少一片铝片,且所述铝片的厚度控制在0.1‑0.2mm。本发明通过PCB板与钢板之间设置铝片,利用铝片的特性可有 全部
背景技术:
PCB压合叠板过程中,PCB板件之间使用钢板隔离。 正常叠板顺序为:底盘-牛皮纸-钢板-PCB板件-钢板-PCB板件-钢板……牛皮纸- 盖板。 PCB压板叠板过程中,PCB板件之间只使用钢板隔离,对于厚铜板及内层芯板残铜 率小的PCB板件,由于钢板的硬度高,使压板过程中PCB板件中芯板内层无铜区受力较有铜 区小,致使树脂填充不完全,PCB板件出现铜箔起皱,内层存在白点等不良坏点,从而导致返 工或者报废。 而在刚挠结合板加工过程中,由刚性板、不流动半固化片及挠性板三部分进行压 合,其中不流动半固化片与挠性板材料聚酰亚胺结合力差,对压合过程中的覆型、导热等性 能要求高,否则容易出现层压白斑、爆板分层等不良问题导致报废,压合品质对产品品质起 关键作用。 为满足刚挠结合板压合过程中施压均匀、覆型效果及温度的要求,生产工厂一般 采用缓冲材料辅助刚挠结合板压合,常用缓冲材料为硅胶垫、离型膜和PE膜的组合。 在此类型缓冲材料使用过程中,硅胶垫长期经受高温高压的环境,会出现不同程 度的老化,在一定使用次数后其缓冲覆型和传热效果无法满足使用要求,导致产品压合出 现白斑报废。白斑的产生主要是由于刚挠结合板中不流动半固化片含胶量低造成的,由于 含胶量低,施压不均会使内层间添胶不均引起部分区域树脂少,玻璃纤维就会显露出来,形 成白斑。而且,此类品质缺陷目前暂无有效方法对硅胶垫使用次数进行统计规范以更换。离 型膜和PE膜均为一次性塑料物料,硅胶垫、离型膜和PE膜使用回收难,不环保。硅胶垫厚度 大(单张1.6mm),硅胶垫、离型膜、PE膜压合方法叠层必须≤3层,否则压力传递不良,导致中 间层产品报废,极大占用压机产能,造成加工成本高。
技术实现要素:
本发明针对上述现有的技术缺陷,提供一种PCB板件的压合叠板方法,通过PCB板 与钢板之间设置铝片,利用铝片的特性可有效解决残铜率小的内层芯板压合过程中由于受 力不均导致内层无铜区填胶不足引起的铜箔起皱和内层白点问题,提高压合的品质和良品 率。 为了解决上述技术问题,本发明提供了一种在PCB板件的压合叠板方法,在对PCB 进行压合的排板结构中,利用PCB上下的钢板对其进行压合,在PCB与上下的钢板之间均设 置至少一片铝片,且所述铝片的厚度控制在0.1-0.2mm。 进一步的,所述铝片的厚度为0.15mm。 3 CN 111586975 A 说 明 书 2/3 页 进一步的,所述铝片的尺寸等于或大于所述PCB的尺寸。 进一步的,所述钢板的外侧均层叠设有至少14张牛皮纸。 进一步的,每次压合后均需要更换全新的牛皮纸。 进一步的,所述铝片为表面平整的双面光铝片。 还提供了一种PCB板件的压合排板结构,包括由下往上依次设置的底盘、牛皮纸 组、钢板、铝片、PCB、铝片、钢板、牛皮纸组和盖板,且所述铝片的厚度控制在0.1-0.2mm。 进一步的,所述铝片的厚度为0.15mm。 进一步的,所述铝片的尺寸等于或大于所述PCB的尺寸;所述铝片为表面平整的双 面光铝片。 进一步的,所述牛皮纸组包括至少14张牛皮纸。 与现有技术相比,本发明具有如下有益效果: 本发明通过在PCB板与钢板之间设置一片铝片,铝片的膨胀系数大,且铝片的韧 性、延展性和导热性好,在压板过程中,铝片可以更好的传递压力到内层芯板中的无铜区, 使内层芯板无铜区及有铜区压力分布一致,树脂受力均匀,可完全填充内层芯板无铜区,从 而防止出现填胶不足的问题,避免内层出现白点等不良现象,从而利用铝片的特性可有效 解决残铜率小的内层芯板压合过程中由于受力不均导致内层无铜区填胶不足引起的铜箔 起皱问题,提高压合的品质和良品率;另外将铝片的厚度控制在0.1-0.2mm,该厚度的铝片 柔软程度适中,可更好并平均的传递压合时施加的压合力,避免因铝片过厚导致传导压力 不均及因铝片过薄导致容易出现变形而影响压合的品质;压合时在钢板的外侧均需要设置 一定张数的牛皮纸作为缓冲物,可进一步提高PCB板压合后的品质,且每次压合时均需更换 全新的牛皮纸,避免压合过的牛皮纸再次利用时因物理特性的变化而影响压合品质;并且 本发明采用铝片的方式,减少了压合过程中硅胶垫和离型膜的使用,降低硅胶垫厚度过厚 造成的品质风险,并可有效提高叠板操作的生产效率。 附图说明 图1为实施例中的压合排板结构示意图。