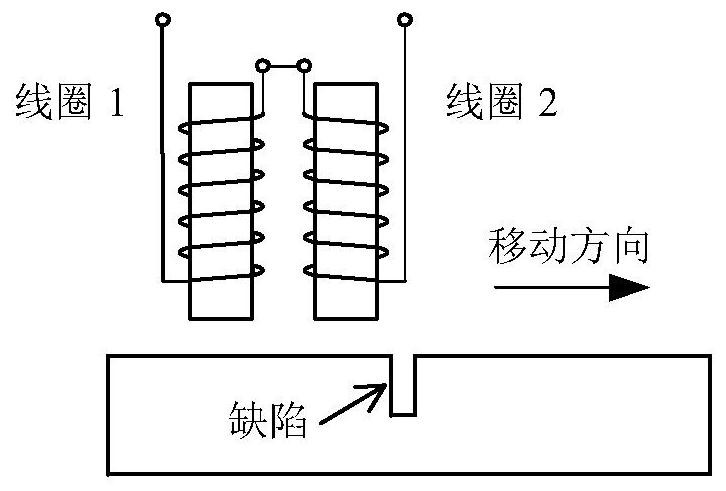
技术摘要:
本发明公开了基于差分涡流的高速轨道缺陷检测系统的参数设计方法,该方法具体步骤如下:首先设计差分涡流检测线圈的直径D参数,以匹配簇状裂纹检测的分辨力要求;然后设计在线检测的涡流激励频率f参数,以匹配高速检测速度v,最大缺陷检测深度dmax要求。本发明方法考虑 全部
背景技术:
高速运行轨道在线检测是一种为了防止高速铁路钢轨故障,对服役状态下的钢轨 采用无损检测方法进行缺陷伤损在线检测和健康监护的技术。目前国内外常用的高速运行 轨道在线检测技术主要包括超声检测、涡流检测、漏磁检测和视觉检测等。涡流检测是一种 基于电磁感应原理的无损检测方法,具有快速性和低成本的优点,在高速运行轨道在线检 测中主要用于钢轨表面和近表面缺陷检测。作为非接触检测技术,涡流检测可以实现高速 化、自动化在线检测。 差分式结构的涡流检测系统可以在一定程度上抑制提离距离等因素带来的影响。 受趋肤效应影响,涡流检测更适用于轨道表面细小缺陷的检测,而其对缺陷深度的分辨率 与涡流检测线圈的直径和激励频率相关。不同深度的裂纹缺陷对轨道安全的危害程度不 同,为了实现不同缺陷危害等级的区分,有必要对差分涡流检测系统的线圈参数和激励频 率进行设计。
技术实现要素:
本发明所要解决的技术问题是:提供基于差分涡流的高速轨道缺陷检测系统的参 数设计方法,通过对检测线圈直径D和激励频率f进行设计,从而优化差分涡流检测对不同 缺陷深度d的分辨率,对一定速度下的差分涡流检测参数的选取提供指导。 本发明为解决上述技术问题采用以下技术方案: 基于差分涡流的高速轨道缺陷检测系统的参数设计方法,包括如下步骤: 步骤1,对于高速轨道所有需要区分深度的缺陷,依据所要求的区分间距最小值Ds 设计差分涡流检测线圈的直径D,即差分涡流检测线圈的直径D满足如下条件: D≤Ds 步骤2,对于高速轨道所有需要区分深度的缺陷,依据所要求的最大缺陷深度dmax, 在步骤1的基础上,设计差分涡流检测的激励频率f,以匹配检测速度v和最大缺陷深度dmax 要求,即差分涡流检测的激励频率f满足如下条件: 其中,σ为待检测试件的电导率,μ为待检测试件的磁导率; 步骤3,根据步骤1和步骤2设计的直径D和激励频率f,设计差分涡流检测线圈,利 用差分涡流检测线圈检测高速轨道所有需要区分深度的缺陷,得到缺陷的深度即高速轨道 受损程度。 作为本发明的一种优选方案,所述差分涡流检测线圈的直径D大于所有需要区分 3 CN 111581814 A 说 明 书 2/3 页 深度的缺陷的宽度。 作为本发明的一种优选方案,所述差分涡流检测线圈的直径D等于间距最小值Ds。 本发明采用以上技术方案与现有技术相比,具有以下技术效果: 本发明提出的差分涡流检测系统的线圈直径和激励频率设计方法考虑到了检测 线圈参数和激励频率对不同缺陷深度分辨的影响,使得设计出的差分涡流检测方案更贴合 实际检测需求,为后续对缺陷深度危害等级的评价提供指导。 附图说明 图1是本发明差分涡流检测示意图。 图2是交流电桥电路原理示意图。 图3是差分涡流检测信号正交解调原理图。 图4是趋肤效应原理示意图。 图5是不同直径检测线圈的电感变化率峰值随缺陷深度变化曲线图。