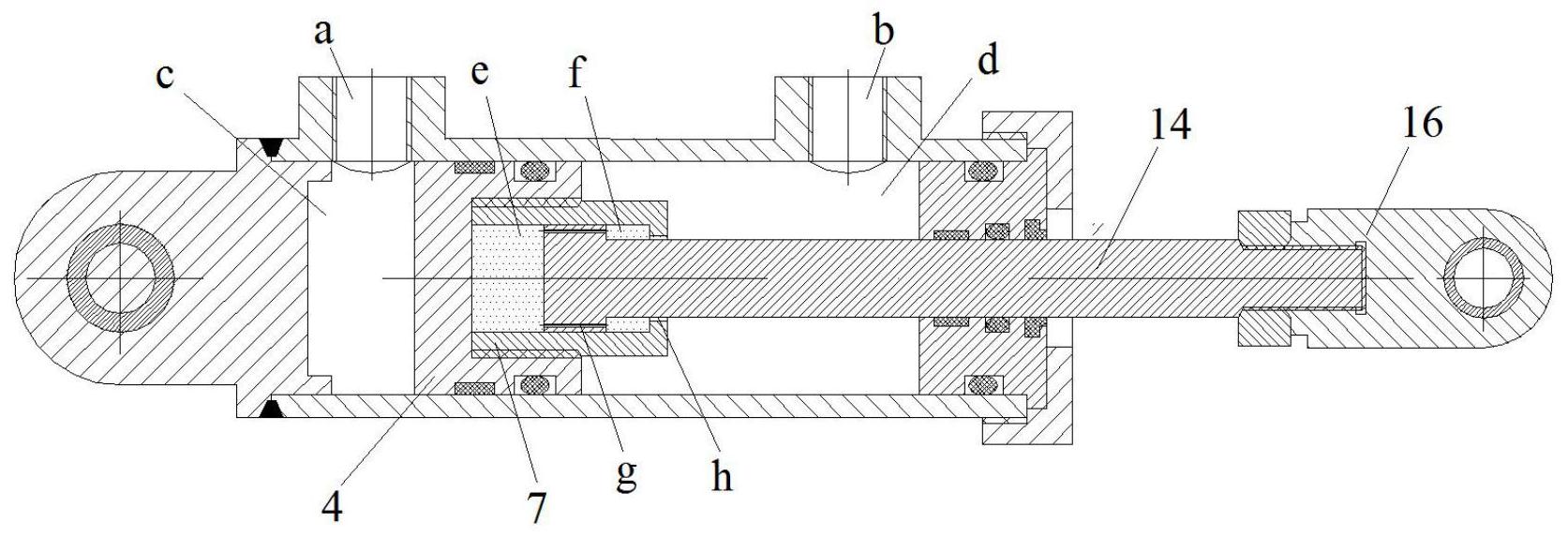
技术摘要:
本发明涉及一种液压作动筒在行程始端的缓冲方法,涉及流体传动技术领域。本发明通过构建的新型内部缓冲结构实现了液压作动筒在工作行程初始端的缓冲功能,能够解决传统内部缓冲结构难以实现作动筒初始端缓冲的问题;该方法在实现过程中所设计的液压作动筒,与作动筒外 全部
背景技术:
液压作动筒是液压系统中重要的往复运动类执行元件,其作动性能对系统具有重 要影响。当液压作动筒的运动速度较快或负载惯量较大时,容易在作动筒工作行程的初始 端或末端产生冲击。其中,在工作行程初始端的冲击主要通过作动筒活塞杆作用于负载,导 致负载瞬间受到一个较大的冲击载荷,从而产生振动和噪声,甚至运动失稳。在工作行程末 端的冲击,主要是因作动筒的活塞刚性撞击筒底而产生,再通过筒壁传递至外负载,产生较 大的冲击振动和噪声,进而影响运动件的工作稳定性,严重时会导致紧固件松动,损坏液压 作动筒及相关设备,缩短其使用寿命。 目前,液压作动筒多采用阶梯圆柱、圆锥台阶和短笛孔等结构型式通过油液动态 可变节流来实现缓冲,属于内部缓冲方式,即在缓冲行程中,将排油腔的一部分油液封闭或 阻隔,使液体只能从节流缝隙中挤出,使排油口液体产生适当的反压力,阻碍活塞的运动。 然而,上述缓冲结构型式多设置在作动筒行程的末端,目的是解决作动筒行程末端的缓冲、 冲击振动问题,但很难解决液压作动筒工作行程初始端的缓冲问题。所以针对液压作动筒 工作行程初始端的缓冲问题,目前多是通过外部缓冲的方式,即在液压系统中增设节流阀、 溢流阀或蓄能器等元器件来实现缓冲。上述外部缓冲方式虽然灵活可调,但会占据较大的 安装空间,使液压系统结构更加复杂,提高了液压系统使用和维护的成本。因此,构建新型 的内部缓冲形式,以实现作动筒在工作行程初始端的缓冲功能,对于弥补现有液压作动筒 的缓冲缺陷、简化液压系统结构、降低系统装机成本等都具有重要意义。
技术实现要素:
(一)要解决的技术问题 本发明要解决的技术问题是:设计一种液压作动筒在行程始端的缓冲方法,通过 构建新型内部缓冲结构实现液压作动筒在工作行程初始端的缓冲功能,一方面解决传统内 部缓冲结构难以实现作动筒初始端缓冲的问题;另一方面使其实现过程中所设计的液压作 动筒与作动筒外部缓冲方式相比,具有结构简单、使用维护成本低等优点。 (二)技术方案 为了解决上述技术问题,本发明提供了一种液压作动筒在行程始端的缓冲方法, 该方法基于一种液压作动筒的设计实现,该液压作动筒设计为包括:筒体1、筒底2、活塞4、 缓冲活塞7、导向套9、静密封10、锁紧套11、防尘圈13、活塞杆14、锁紧螺母15和杆头16; 其中,所述筒体1的两端分别设有第一油口a和第二油口b,筒体1中靠近第一油口a 的一侧安装筒底2,筒体1中靠近第二油口b的一侧由内向外依次安装导向套9和锁紧套11; 活塞4位于筒体1内部,活塞4的外缘为圆柱状结构,活塞4的内部为盲孔状结构,活塞4的底 4 CN 111577702 A 说 明 书 2/5 页 面与筒体1内壁面、筒底2端面形成无杆腔c,活塞4的顶面即盲孔开口端面与筒体1内壁面、 导向套9端面形成有杆腔d;缓冲活塞7的外缘为圆柱状结构,缓冲活塞7的内部为阶梯孔状 结构,缓冲活塞7的阶梯孔直径较大的一端伸入活塞4的内部,并与活塞4的内壁面连接紧 固;活塞杆14为阶梯轴结构,其中直径较大的部分位于缓冲活塞7的内部并沿轴向开有数个 阻尼通孔g,活塞杆14直径较大一端的底面与缓冲活塞7内壁面、活塞4盲孔底面形成无杆缓 冲腔e,活塞杆14阶梯轴的轴肩与缓冲活塞7内壁面形成有杆缓冲腔f,活塞杆14直径较小的 一端依次穿过缓冲活塞7的内孔、导向套9的内孔和锁紧套11的内孔从筒体1的端面伸出,并 与杆头16通过螺纹连接,并且通过锁紧螺母15连接紧固; 所述的行程始端缓冲的液压作动筒中,活塞杆14直径较小部分的外缘与缓冲活塞 7内孔之间为隙配合,由此形成环形阻尼缝隙h; 所述的行程始端缓冲的液压作动筒中,第一油口a与无杆腔c相互沟通,第二油口b 与有杆腔d相互沟通,有杆腔d与有杆缓冲腔f通过环形阻尼缝隙h连通,有杆缓冲腔f与无杆 缓冲腔e通过阻尼通孔g连通; 基于所述液压作动筒实现的液压作动筒在行程始端的缓冲方法,包括以下步骤: 当作动筒处于缩回状态时,活塞杆14相对于筒体1处于缩回状态,活塞杆14相对于 缓冲活塞7处于伸出状态,即活塞4的底面靠近筒底2内端面或者两者直接接触,活塞杆14的 轴肩端面靠近缓冲活塞7的阶梯孔的台阶端面或者两者直接接触; 当作动筒开始伸出时,油液从第一油口a进入无杆腔c,进而推动活塞4、缓冲活塞7 和活塞杆14一并向外伸出,外部负载通过杆头16反推活塞杆14,在外部负载和油液的共同 作用下,无杆缓冲腔e内部的油液被挤压并通过阻尼通孔g进入有杆缓冲腔f,再由有杆缓冲 腔f通过环形阻尼缝隙h被挤入有杆腔d,并与有杆腔d内部的油液一起通过第二油口b流出, 油液依次通过阻尼通孔g、环形阻尼缝隙h从无杆缓冲腔e先流入有杆缓冲腔f再流入有杆腔 d的过程中,活塞杆14相对于缓冲活塞7作缩回运动,起缓冲作用; 当作动筒伸出一段距离后,无杆缓冲腔e内部的油液全部被挤出,活塞杆14的底面 与活塞4的内孔的端面接触,缓冲过程停止;作动筒继续伸出,直到缓冲活塞7与导向套9接 触时,作动筒实现伸出到位; 当作动筒处于伸出状态时,活塞杆14相对于筒体1处于伸出状态,活塞杆14相对于 缓冲活塞7处于缩回状态,即缓冲活塞7靠近导向套9或者两者直接接触,活塞杆14的底面靠 近活塞4内孔的端面或者两者直接接触; 当作动筒开始缩回时,油液从第二油口b进入有杆腔d,进而推动活塞4、缓冲活塞7 和活塞杆14一并作缩回运动,外部负载通过杆头16拉拽活塞杆14,在外部负载和油液的共 同作用下,有杆缓冲腔f内部的油液被挤压,一部分通过阻尼通孔g进入无杆缓冲腔e,另一 部分通过环形阻尼缝隙h进入有杆腔d,并与有杆腔d内部的油液一起推动作动筒缩回,油液 通过阻尼通孔g由有杆缓冲腔f流入无杆缓冲腔e以及通过环形阻尼缝隙h由有杆缓冲腔f流 入有杆腔d过程中,活塞杆14相对于缓冲活塞7作外伸运动,起缓冲作用; 当作动筒缩回一段距离后,有杆缓冲腔f内部的油液全部被挤入无杆缓冲腔e和有 杆腔d,活塞杆14的轴肩端面靠近缓冲活塞7的阶梯孔的台阶端面或者两端面直接接触,从 此停止缓冲;作动筒继续缩回,直到活塞4的底面与筒底2内端面接触,作动筒实现缩回到 位。 5 CN 111577702 A 说 明 书 3/5 页 优选地,所述导向套9的一端外缘伸入筒体1内部并通过静密封10与筒体1内壁面 密封,导向套9的另一端的端面由锁紧套11压紧,锁紧套11再通过螺纹与筒体1连接紧固。 优选地,所述活塞4外缘与筒体1内壁面通过第一支撑环5、第一动密封6分别实现 支撑与动密封。 优选地,所述活塞杆14外缘与导向套9的内孔通过第二支撑环8、第二动密封12、防 尘圈13分别实现支撑、动密封,所述活塞杆14外缘与导向套9的内孔之间还设有防尘圈13。 优选地,所述筒体1与筒底2之间通过焊接或螺纹连接方式实现连接紧固,并安装 密封装置。 优选地,所述缓冲活塞7与活塞4之间通过螺纹连接或焊接实现连接紧固。 优选地,所述阻尼通孔g的数量为2-4个。 优选地,所述筒底2内部安装第一轴承3。 优选地,所述杆头16内部安装第二轴承17。 本发明还提供了一种所述的液压作动筒在行程始端的缓冲方法在液压系统中的 应用。 (三)有益效果 与现有技术相比,本发明所具有的有益效果是: (1)构建出作动筒新型内部缓冲结构,通过嵌套式活塞、细长阻尼孔口和环形阻尼 缝隙的有机配合,巧妙地将无杆腔内部油液引入缓冲活塞内部,使活塞与活塞杆产生相对 运动和可变阻尼,能够解决传统内部缓冲结构难以实现作动筒初始端缓冲的问题; (2)该方法在实现过程中所设计的液压作动筒,与作动筒外部缓冲方式相比,具有 结构简单、安装维护方便、使用成本低等优点。 附图说明 图1是本发明的缓冲方法在实现过程中所设计的液压作动筒主要结构示意图; 图2是图1中活塞杆伸出始端起缓冲作用时的结构示意图; 图3是图1中活塞杆伸出过程中缓冲到位后的结构示意图; 图4是图1中活塞杆伸出到位后的结构示意图; 图5是图1中活塞杆缩回始端起缓冲作用时的结构示意图; 图6是图1中活塞杆缩回过程中缓冲到位后的结构示意图。 其中:1-筒体,2-筒底,3-第一轴承,4-活塞,5-第一支撑环,6-第一动密封,7-缓冲 活塞,8-第二支撑环,9-导向套,10-静密封,11-锁紧套,12-第二动密封,13-防尘圈,14-活 塞杆,15-锁紧螺母,16-杆头,17-第二轴承,a-第一油口,b-第二油口,c-无杆腔,d-有杆腔, e-无杆缓冲腔,f-有杆缓冲腔,g-阻尼通孔,h-环形阻尼缝隙。