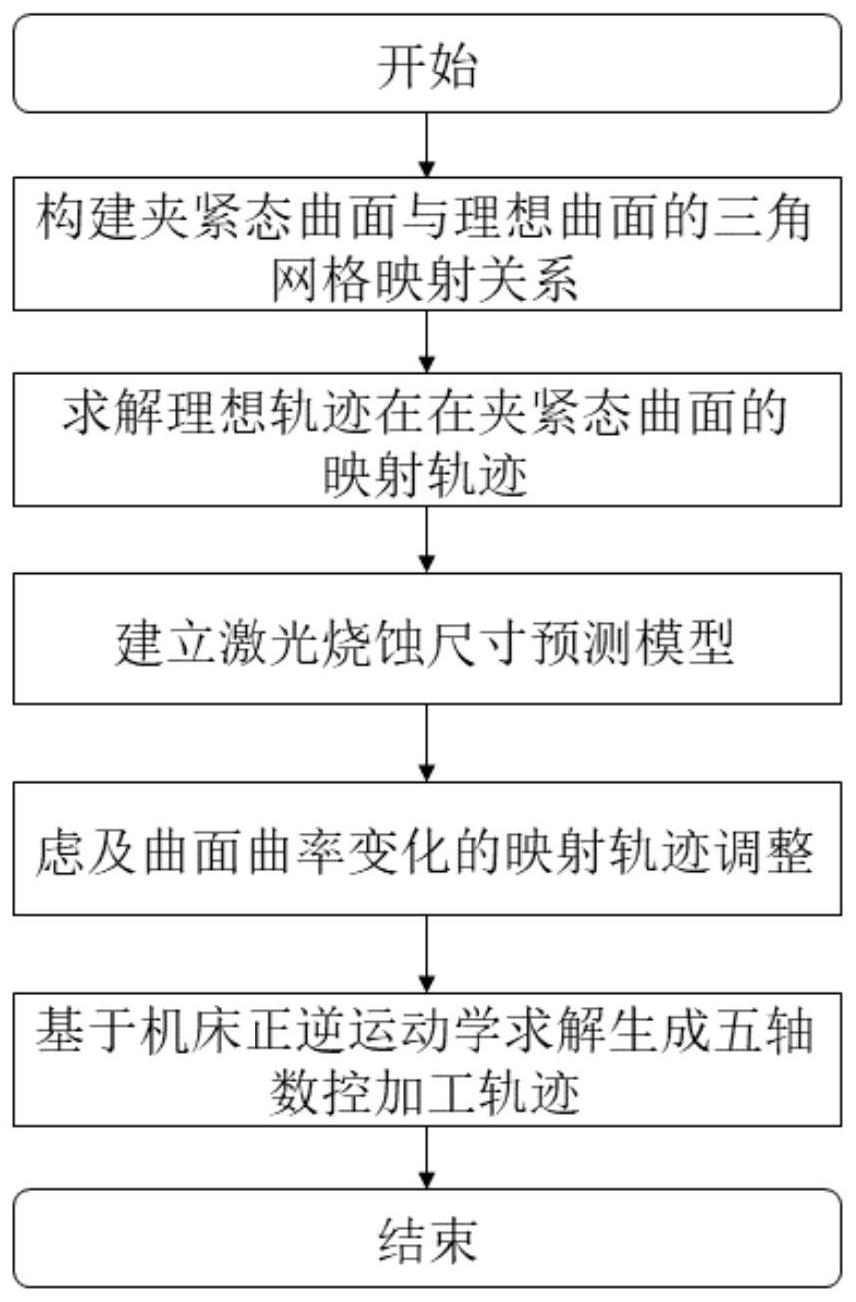
技术摘要:
本发明一种薄壁曲面表层图案激光加工轨迹求解方法属于薄壁曲面表层图案精密制造技术领域,涉及一种薄壁曲面表层图案激光加工轨迹求解方法。该方法根据薄壁曲面件装夹变形特点,通过三坐标测量机获得夹紧态曲面点云数据,沿径向方向映射到理想曲面,构建夹紧态曲面及理 全部
背景技术:
随着航空航天、信息传导等领域的发展,针对电磁波传输控制需要的复杂曲面结 构功能一体化部件逐渐成为了一种重要的构件形式。高速飞行器天线是此类构件的一重要 应用,为满足高性能和轻量化需求,天线多采用轻质材料薄壁曲面基体结构,且加工精度要 求一般在微米级,对现有加工技术提出了新的挑战。在薄壁曲面零件表面高效率、高精度的 制造复杂图案仍是研究的热点与难点。近年来迅速发展的激光刻蚀加工技术,因其非接触 式加工、易于与多轴驱动装置结合等优点,逐渐成为复杂曲面构件表层图案精密高效制造 的有效方法。但是薄壁曲面件刚度低,在夹紧态下易产生弹性变形,导致实际加工曲面与理 想曲面产生偏差,若按理想天线图案规划的加工轨迹进行加工,将导致装夹释放后天线图 案曲线的轮廓、位置与原始设计不符。此外,薄壁曲面变形后曲率发生变化,加工过程激光 工艺参数将发生改变,影响天线图案的加工尺寸精度。因此迫切需要研究一种薄壁曲面表 层图案激光加工轨迹求解方法,求解图案理想加工轨迹在夹紧态曲面的映射轨迹,并考虑 曲面变形后的曲率变化对激光工艺参数的影响,并以加工图案曲线的轮廓精度和尺寸精度 为约束对加工轨迹超差点进行调整,实现薄壁曲面表层图案的精密加工。 现有技术文献1“Simulation of workpiece deformation caused by releasing the clamping force”,Shao Xiaodong等,Transactions of the Canadian Society for Mechanical Engineering,2013,37:703-712,该文献提出了一种基于四面体网格模型的加 工轨迹映射方法,通过有限元方法建立变形前后有限元网格间的映射关系,并根据相似变 换原理求解工件变形后的加工轨迹,改善了薄壁件的加工精度。但是在真实情况下装夹变 形受装夹顺序和夹紧力的影响,稳定性较差,采用仿真分析的方法会引入新的误差。现有技 术文献2“Adaptive machining for curved contour on deformed large skin based on on-machine measurement and isometric mapping”,Bi Qingzhen等,International Journal of Machine Tools and Manufacture,2019,136:34-44,该文献针对大型薄壁蒙 皮曲面,提出了一种曲面匹配方法,将变形后曲面测量点云投影到标准曲面获得初始匹配 点,并基于等距映射的曲面匹配算法迭代构建标准曲面与变形曲面的映射关系,并据此自 适应调整加工轨迹,实验结果表明这种方法有效提高了加工轮廓精度。但是这种方法仅适 用于变形主要沿法向方向的大型薄壁蒙皮曲面工件,且曲面匹配算法需要大量的迭代计 算,复杂费时。
技术实现要素:
本发明针对现有技术缺陷,发明了一种薄壁曲面表层图案激光加工轨迹求解方 法。该方法首先建立夹紧态曲面与理想曲面间映射关系,求解理想轨迹在夹紧态曲面的映 9 CN 111581874 A 说 明 书 2/12 页 射轨迹,然后分析由夹紧态曲面曲率变化导致的局部轨迹激光加工工艺参数变化,结合激 光烧蚀尺寸预测模型,以表层图案加工精度要求为约束调整加工轨迹,保证了薄壁曲面表 层图案曲线的加工尺寸精度和轮廓精度。 本发明采用的技术方案是一种薄壁曲面表层图案激光加工轨迹求解方法,其特征 在于,该方法首先根据薄壁曲面件装夹变形特点,提出装夹变形主要沿径向方向的假设,通 过三坐标测量机获得夹紧态曲面点云数据,沿径向方向映射到理想曲面,分别构建夹紧态 曲面及理想曲面三角网格映射关系,求解理想加工轨迹在夹紧态曲面上的映射轨迹,然后 根据激光烧蚀尺寸预测模型,离散化求解映射轨迹上任一刀位点处的材料烧蚀深度和烧蚀 宽度,考虑曲面曲率变化导致的瞬时工艺参数变化,并对图案曲线尺寸或轮廓超差处进行 局部加工轨迹点调整,最终后处理生成符合加工精度要求的五轴数控加工轨迹,方法的具 体步骤如下: 步骤1,构建夹紧态曲面与理想曲面的三角网格映射关系 首先,在Ansys软件中,以圆筒底端面2的圆心为原点,建立坐标系,圆筒底端面2为 XOY平面,圆筒轴线为Z轴。薄壁圆筒件在径向方向受夹持,夹紧力在周向方向对称分布。采 用Ansys有限元分析软件对工件装夹变形进行仿真,在Ansys中建立四节点shell181单元模 型,并设置材料属性,采用自由网格划分方式。在4个夹紧点J1、J2、J3、J4施加集中载荷,在圆 筒上端面1设置全约束,求解当前载荷与约束下的结果;在后处理界面设置在柱坐标系下查 看结果,此时x方向代表径向方向,y方向代表切向方向,z方向代表轴向方向。将节点变形量 计算结果导出,并计算各个节点径向变形与总变形间的偏差值,若偏差值比总变形小一个 数量级,认为变形主要沿径向方向,并提出薄壁圆筒件装夹变形主要沿径向方向的假设。 根据薄壁圆筒件装夹变形主要沿径向方向这一假设,用三坐标测量机测量获得夹 紧态薄壁圆筒离散点云,并沿径向映射到理想曲面上,即可求解理想曲面中测量点的唯一 映射点。将夹紧态曲面离散点云进行三角网格剖分,构建夹紧态圆筒三角网格曲面,并根据 映射点云以相同拓扑关系构建理想曲面的三角网格单元。由此将测量点与映射点间映射关 系转化为两三角网格曲面顶点间的映射关系,建立夹紧态曲面与理想曲面间的映射关系。 步骤2,求解理想轨迹在夹紧态曲面的映射轨迹 通过三角形的仿射变换理论,求解理想曲面网格与夹紧态曲面网格上任一点的映 射关系。根据原始设计图案在理想曲面上生成理想刀位点,令某一理想刀位点为Wi(i=1, 2,...,n),n为刀位点个数,在理想曲面网格中根据刀位点坐标值找到它所在的的三角面 片,令此三角面片顶点坐标为Qi,Mi,Ni。理想刀位点Wi在ΔQiMiNi中的面积坐标可表示为为Wi (λ1,λ2,λ3),则点Wi满足公式(1),且λ1 λ2 λ3=1。 (λ1 λ2 λ3)Wi=λ1Qi λ2Mi λ3Ni (1) 点Wi与ΔQiMiNi各顶点将ΔQiMiNi分割为ΔQiMiWi,ΔMiNiWi,ΔQiNiWi,其面积分别 为 由三角形面积坐标的性质可得: 10 CN 111581874 A 说 明 书 3/12 页 理想网格曲面中的三角面片ΔQiMiNi在夹紧态网格曲面中的映射三角面片为Δ Q′iM′iN′i,由根据三角形仿射变换的面积坐标不变性,可以求得ΔQiMiNi内任意刀位点Wi在 ΔQ′iM′iN′i内的映射刀位点W′i的坐标为: W′i=λ1Q′i λ2M′i λ3N′i (3) 在UG中建立薄壁圆筒件理想模型,在工件表面绘制图案曲线,并投影到工件表面, 用曲线驱动的方式生成五轴加工轨迹。将刀位点导出,并由式(1)-(3) 求解其在夹紧态曲面的映射点,实现加工轨迹的映射。 步骤3,建立烧蚀尺寸预测模型 建立激光烧蚀尺寸预测模型,便于后续离散化求解映射轨迹上任一刀位点处的材 料烧蚀深度和烧蚀宽度,判断轨迹超差点。采用纳秒激光进行加工,光束在x-z截面激光能 量密度的分布可表达为: 式中,w为实际光斑尺寸,F0为光束作用在x-z截面的峰值能量密度,可由下式计 算: 式中 为激光器的平均功率,f为激光的脉冲重复频率。 光束在z方向任意位置的光斑尺寸w可表示为: 式中,w0为光束在束腰位置的光斑尺寸,λ为激光的波长。 当脉冲激光能量密度超过材料的烧蚀阈值时,激光作用区内材料表面出现蒸发现 象,形成材料的去除,此过程符合能量守恒定律: (1-R)F(x,z)-Fth=δ(x,z)(ρsHsl ρlHlv) (7) 式中,R为目标材料对激光的反射率,ρl为目标材料的液态密度,Hlv为目标材料的 汽化焓,Hsl为目标材料的熔化焓,Fth为激光对目标材料的烧蚀阈值,F(x,z)为光束在x-z截 面的能量密度分布,δ(x,z)为作用于材料表面的单脉冲激光束离焦量为z时,x-z截面上任 一点材料烧蚀深度,记为单脉冲激光烧蚀深度。 则单脉冲烧蚀深度δ(x,z)可表示为: 11 CN 111581874 A 说 明 书 4/12 页 作用于材料表面的光束光斑偏移焦平面的距离和方向,决定了各个脉冲激光作用 于材料表面的光斑尺寸。当z为负值时,激光束焦平面在材料表面上方,记为负离焦;当z为 正值时,激光束焦平面在材料表面下方,记为正离焦。 当脉冲激光的扫描速度为v时,作用于某位置的激光脉冲个数N可表示为: 其中int为向下取整函数。激光束在传播过程中逐渐发散,光束的发散度可由光斑 尺寸的微分方程表示: 则某位置(x,z)处的激光的发散角θ*为: 经过位置(xk-1,zk-1)的第k个激光脉冲烧蚀之前,光束的离焦量zk-1可表示为: zk-1=z0 δk-1 (12) 式中,z0为光束的初始离焦量,δk-1为前k-1个脉冲烧蚀深度之和。 经过烧蚀位置(xk-1,zk-1)的第k个激光脉冲的单脉冲能量分布可表示为: 计算的烧蚀位置(x *k-1,zk-1)处的激光发散角θ(xk-1,zk-1)可表示为: 烧蚀沿着激光的传播方向进行,经过烧蚀位置(xk-1,zk-1)的第k个激光脉冲烧蚀深 度可表示为: 烧蚀前后两个空间位置(xk-1,zk-1)和(xk,zk)有以下几何关系: 令N=2n 1则脉冲激光烧蚀目标材料的截面尺寸可表示为: 当x=0时,烧蚀深度达到最大值,最大烧蚀深度为depth(0)。 12 CN 111581874 A 说 明 书 5/12 页 depth(x)=0时的位置即为烧蚀轮廓的边缘,两侧边缘的距离为最大烧蚀宽度,令 x=depth-1(x)为depth(x)的反函数,当depth(x)=0时,反函数的两个解分别为x1,x2,则最 大烧蚀宽度width=|x1-x2|。 步骤4,虑及曲面曲率变化的映射轨迹调整 结合烧蚀尺寸预测模型,考虑曲面曲率变化导致的瞬时加工工艺参数变化,并对 图案曲线尺寸或轮廓超差处进行局部映射加工轨迹点调整。 将映射轨迹相邻两刀位点W′i、W′i 1间沿进给方向的曲面曲线简化为半径为R1的圆 弧,将W′i、W′i 1间理想图案曲线简化为半径为R2的圆弧。结合最近邻搜索算法和最小二乘曲 面拟合法,对W′i附近点进行最小二乘曲面拟合,曲面参数方程为表示为r(u,v),曲面r(u, v)的第一基本形式和第二基本形式可表示为: 其中系数E,F,G,L,M,N为: 其中 为曲面r(u,v)在W′i点的单位法矢量,可由下式计算: 曲面r(u ,v)的主曲率和主方向为Weingarten矩阵ω的特征值和特征方向, Weingarten矩阵ω可表示为: 求解Weingarten矩阵ω的特征值和特征方向,可解得曲面r(u,v)的最大主曲率为 k1,对应的主方向为d1,最小主曲率为k2,对应的主方向为d2。令进给方向 与主方向d1 的夹角为 则由欧拉公式可以求得沿进给方向的法曲率,即相邻刀位点W′i、W′i 1间沿进给 方向的曲面曲线曲率kn: 以W′i为原点, 方向为x0轴,W′i在夹紧态曲面上的法矢方向 为z1轴,建立局 部动态平面直角坐标系。加工过程中,激光束由刀位点W′i运动到W′i 1时,轨迹任意位置的 激光加工初始离焦量z0可由下式计算: 13 CN 111581874 A 说 明 书 6/12 页 激光束由刀位点W′i运动到W′i 1的过程中,实际扫描速度v'可由下式计算: 根据激光烧蚀尺寸预测模型,由Matlab软件迭代计算,可以得到W′i到W′i 1点的运 动轨迹任意位置的材料烧蚀深度为depth(x0),烧蚀宽度为width(x0)。 则加工时,光束由刀位点W′i经过W′i 1的过程中,W′i、W′i 1间沿进给方向的曲面曲 线任意位置的烧蚀深度误差DE可表示为: DE=depth(x0)-depth(0) (25) 由于夹紧态曲面曲率变化,映射到夹紧态曲面的加工轨迹相邻两刀位点间的距离 也发生变化,实际加工曲线与理想曲线之间产生偏差,即轮廓偏差。 采用三次B样条插值的方法,通过特征点即映射到夹紧态曲面的轨迹点反算控制 点,插值出夹紧态曲面上的理想天线图案的图形曲线。三次B样条曲线的NURBS有理分式形 式为: 式中,ωi(i=0,1,...n)为权因子,首末权因子ω0,ωn>0,其余ωi≥0,Ai(i=0, 1,...,n)为控制点,Bi,k(u)为k次规范B样条基函数,u为参数值,刀位点W′i对应的参数值为 ui。 则夹紧态曲面理想天线曲线在刀位点W′i处的曲率半径R2可由下式计算: 基于相邻刀位点W′i、W′i 1间理想曲线,建立局部平面直角坐标系,则W′i、W′i 1间理 想曲线方程可表示为: 加工后,W′i、W′i 1间实际曲线方程可表示为: z3=width(x0)-width(0) (29) 则加工时,光束由刀位点W′i经过W′i 1的过程中,实际加工曲线与理想曲线之间的 轮廓偏差CR可表示为: CR=z3-z2 (30) 将烧蚀深度误差的允差值表示为[DE],将图案曲线轮廓偏差允差值表示为[CR], 14 CN 111581874 A 说 明 书 7/12 页 由Matlab软件编程计算相邻刀位点W′i、W′i 1间轨迹的烧蚀深度误差DEi及图案曲线轮廓偏 差CRi,并判断是否在允差范围内,若超差,在两刀位点中间增加一个刀位点W′|u=u',其中参 数u'=(ui ui 1)/2,继续判断,若在允差范围内,计算刀位点W′i、W′i 2间轨迹的烧蚀深度误 差DEii及图案曲线的轮廓偏差CRii,若在允差范围内则去除冗余点W′i 1,继续判断,最终求 解得到符合精度要求的刀位点数据。 步骤5,基于机床正逆运动学求解生成五轴数控加工轨迹 调整后的刀位数据点无法通过UG软件的后处理模块生成能被机床识别的五轴加 工程序,因此为将调整后的刀位数据变换成机床各轴的运动数据,需对激光-五轴数控机床 系统进行正逆运动学求解。 OMXMYMZM为与机床床身固连的坐标系,在运动学变换中刀位点和刀轴方向相对于 机床坐标系O X Y Z 的齐次坐标分别为M MM M M M P和 V。激光加工为非接触式加工,没有实体刀具,刀 轴方向为激光束传播方向。 OAXAYAZA为与定轴A固联的坐标系,原点OA在坐标系中OMXMYMZM的坐标为(Umax,Umay, Umaz),当机床运动到(X,Y,Z,A,C)位置时,OAXAYAZA会绕其自身的X轴旋转-A角度,则OAXAYAZA 相对于OMXMYMZM的位姿 为: OCXCYCZC为与定轴C固联的坐标系,原点OC在坐标系中OAXAYAZA的坐标为(Uacx,Uacy, Uacz),当机床运动到(X,Y,Z,A,C)位置时,OCXCYCZC会绕其自身的Z轴旋转-C角度,则OCXCYCZC 相对于OAXAYAZA的位姿 为: OWXWYWZW为与工件固联的工件坐标系,原点OW与OC重合,则OWXWYWZW相对于OCXCYCZC的 位姿 为: 在工件坐标系中,刀位点和刀轴方向的齐次坐标WP和WV分别为: 对于调整后的刀位点,需要求解其刀轴方向。将某一刀位点Pi(x,y,z)及附近的点 15 CN 111581874 A 说 明 书 8/12 页 拟合最小二乘曲面,求解该刀位点在此曲面的法矢,法矢方向 即为该刀位点的在 工件坐标系下的刀轴方向。 OTXTYTZT为与激光器固联的刀具坐标系,OTXTYTZT相对于OMXMYMZM的位姿 为: 在刀具坐标系中,刀位点和刀轴方向的齐次坐标TP和TV分别为: 通过齐次变换,将刀位点分别从刀具坐标系和工件坐标系映射到机床坐标系: 解得在工件坐标系下,刀位点和刀轴方向的齐次坐标WP和WV分别为: 由机床逆运动学变换得到工件坐标系到机床坐标系的反变换公式: 其中,A轴的运动的范围为-5°到95°,C轴转角可为任意值,为避免A的解超出运动 范围或由于C轴角度多解导致的机床转角C的不连续性,A、C角度应修正为: 由式(39)-(40)即可将调整后的刀位数据变换成机床各轴的运动数据,进而生成 夹紧态曲面表层图案的五轴数控加工程序。 本发明的显著效果和益处是该方法阐明了薄壁曲面件的装夹变形特点,可快速准 16 CN 111581874 A 说 明 书 9/12 页 确求解得到理想加工轨迹在夹紧态曲面的映射轨迹;该方法分析了映射轨迹对变形后曲面 的适用性,考虑了变形导致的曲面曲率变化对映射轨迹激光加工工艺参数的影响,结合激 光烧蚀尺寸预测模型对轨迹局部超差点及冗余点进行调整,最终生成符合精度要求的夹紧 态薄壁曲面表层图案的激光加工轨迹。该方法解决了薄壁曲面件表层图案激光加工过程 中,由于装夹变形导致的加工位置偏移,激光工艺参数改变,加工图案轮廓与原始设计不 符,图案过烧蚀或欠烧蚀等问题,能够减小由于装夹变形造成的薄壁曲面件表层图案激光 加工误差,对于实现薄壁曲面件表层图案精细制造具有重要意义。 附图说明 图1—方法整体流程图。 图2—薄壁圆筒件载荷与约束施加情况。其中,1—圆筒上端面,在此端面设置全约 束,即各个方向的自由度为0,2—圆筒底端面,坐标系以圆筒底面圆圆心为原点,底面为xoy 平面,圆筒轴线为z轴;图中,薄壁圆筒件在距圆筒底面0.03m所在截面有4个夹紧点J1、J2、 J3、J4。 图3—薄壁圆筒件装夹变形仿真结果。其中,图a)为径向变形云图,图b)为切向变 形云图,图c)为轴向变形云图,图d)为总变形云图,变形量单位为m。 图4—理想加工轨迹刀位点图。 图5—映射轨迹刀位点图。 图6—刀位点调整程序流程图。 图7—经映射及调整后的加工轨迹刀位点图。其中刀位点坐标单位为mm,图中“·” 所示为映射轨迹刀位点,“*”所示为增加的刀位点,“o”所示为去除的冗余刀位点。