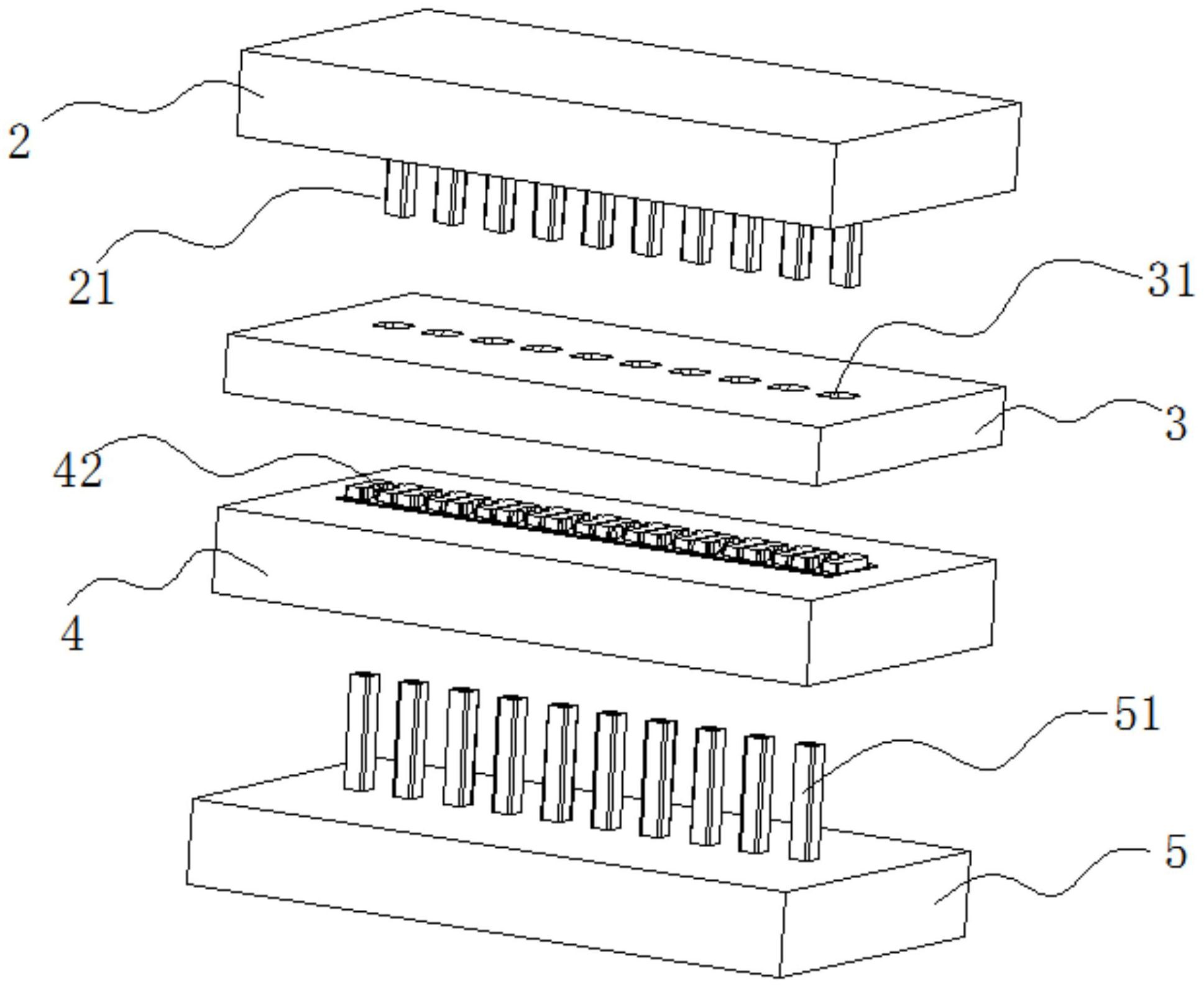
技术摘要:
本发明公开了高效率一体电感制造工艺:1)制备粉料,采用水性树脂等组分并应用75%以下的酒精溶液,加入软磁性材料粉后配合锆珠分散包膜,获得低树脂含量的高性能粉料;2)预备线圈件,线圈件包括线圈;3)预备成型模具,成型模具包括上模、盖板、中模及底模;4)将线 全部
背景技术:
目前的一体电感制造工艺,是先通过冷成型模具将粉料(又称铁粉料或者铁粉)与 线圈组件进行预成型冷压,形成备用的电感半成品;然后再将电感半成品放置到热成型模 具中进行热压成型,经过软化、固化、保压的过程之后形成一体电感。中国发明专利申请《一 体成型电感成型方法》,申请号201811022929.9,申请公布号CN109166717A,申请公布日期 2019-01-08,其公开了一种一体成型电感成型方法:步骤一,将线圈、SMD引脚、混合有热固 性粘结剂和耦合剂的铁粉料放置在冷成型模的模腔中,以1.8~2.5T/cm2的压力进行预成 型冷压,线圈固定于铁粉料中压制成半成品;步骤二,热成型模加热到预热温度,预热温度 高于使热固性粘结剂软化、铁粉粒相对位移变得容易的软化温度;步骤三,半成品放置在热 成型模设有的电感容置孔、SMD引脚容置孔中加热到软化温度;步骤三,对放置在电感容置 孔、SMD引脚容置孔中的半成品以热固化压力进行热压,且升温到热固性粘结剂的热固化温 度使热固性粘结剂固化并保压,完成一体式成型电感成型。上述一体成型电感成型方法,其 采用的便是目前较为常见的先将线圈与粉料冷压预制成电感半成品后再热压成型为一体 电感。目前的这种一体电感制造工艺,存在着两大不足:一是不良率高,因为存在着冷压的 步骤,由于线圈相对较为脆弱,在线圈与铁粉进行冷压预制的过程中,容易把线圈压坏,导 致线圈变形、断路等缺陷,从而导致不良品的产生;二是生产效率低,产能低导致成本高,尽 管上述《一体成型电感成型方法》已经增加了“热成型模预热”的步骤,缩短了一部分制造时 间,但整个制造过程需要花费时间仍然超过100秒,而且由于其是先冷压后热压的,冷压成 型后的电感半成品的粉料处于压实结合状态,因此后续需要“使热固性粘结剂软化、铁粉粒 相对位移变得容易”的软化后重新塑造形态的加热软化过程,所以导致了热成型过程中的 “加热软化塑形时间”与“加热加压保压固化定型时间”较长,必须在30秒和50秒以上,加起 来便超过80秒,再加上前面冷压步骤的时间,便会远远超过100秒,这样便大大限制了生产 效率的提升;这是冷压成型电感半成品的步骤所带来的巨大缺陷,导致软化塑形和热压固 化所需的时间过长。因此,目前一体电感制造工艺还存在许多有待改进完善的地方。
技术实现要素:
针对上述不足,本发明的目的在于,提供一种高效率一体电感制造工艺及成型模 具,减少冷压成型电感半成品的步骤,避免制程中线圈的损坏,提高成品率,同时提升生产 效率以及产品品质。 本发明采用的技术方案为:一种高效率一体电感制造工艺,包括如下步骤: 1)粉料的制备; 1.1)预备以下重量份数的组分:水性树脂15-20份;胺基树脂2-5 份;组合助剂1-2 份;水与酒精的混合溶液200-300份,其中,酒精的含量控制在75%以下;将上述组分在2500 4 CN 111599586 A 说 明 书 2/10 页 至3500r/min的高速条件下搅拌分散,获得树脂混合液,并使得树脂混合液中的树脂的固含 量为 0.5%至1.5%;具体地,所述水性树脂为水性环氧改性树脂、聚脂改性树脂、水性丙烯 酸改性树脂的一种或两种以上混合;所述胺基树脂为六甲氧基甲基三聚氰胺、甲基醚化高 亚胺三聚氰胺的一种或两种以上混合;所述组合助剂包括偶联剂、成膜助剂及湿润剂;在高 速分散机中进行搅拌25至35分钟,获得树脂混合液。 1.2)按软磁性材料粉与树脂混合液比为1:0.8至1:1.2的比例,将软磁性材料粉投 入树脂混合液中,再投入锆珠,进行持续搅拌,先搅拌至液体浓稠,再搅拌至液体完全挥发 成粉体,获得粉料半成品;在搅拌的过程中,利用锆珠的剪切力、磨擦力使得低树脂固含量 为0.5%至 1.5%的树脂混合液与软磁性材料粉能均匀的分散包膜。具体地,在行星搅拌机 中进行持续搅拌,先高速搅拌至液体浓稠,再降低速度,低速搅拌至液体完全挥发成粉体; 其中,与软磁性材料粉和树脂混合液的整体重量相比,所投入的锆珠的比重为5~7,且,锆 珠为直径1~5mm的高纯锆珠。其中,电感所使用的材料鉄氧体、鉄硅铝合金、鉄镍合金等都 可统称为软磁,即软磁性材料粉。 1.3)将粉料半成品依次进行烘烤及筛选,获得所需粒度大小的成品粉料。具体地, 通过烤箱进行烘干,用90摄氏度/120分钟;然后使用震动筛选机进行筛选,筛选网为三层至 五层,纱网目数依据所需粉料大小而定;筛出分选各目数的粉料,检查后保证干爽无结块, 并使用霍尔流速计检测,秤重50g用秒表测流速时间40~50秒。 在此,要对上述粉料进行专门的说明,因为上述粉料的存在,依托其性能,才能实 现后续的工艺步骤。一般来说,粉料中的软磁性材料粉含量纯度越高性能越好,性能越好的 粉料,相应地,便可以采用越少的铜卷,也就是说,同样数值的电感,粉料纯度越高,那么体 积就会越小。上述工艺制备的粉料,采用优化组分配方,采用水性树脂、氨基树脂组合,并应 用浓度75%以下的酒精溶液,加入软磁性材料粉后配合锆珠分散包膜,实现高速搅拌同时 防止燃烧爆炸,可以获得包膜均匀的低树脂含量的粉料,提升粉料性能,并且提高粉料的流 动性能,使得其可以沙漏式从孔进行添加。而且由于树脂包膜均匀,且含量低,也能减少后 续的热固化时间,提升热固化效果品质,压合能使每一细小软磁性材料粉体颗粒表面的包 膜紧密结合。另外,水与酒精的混合溶液中,酒精的含量控制在75%以下;因此,在搅拌的过 程中,无燃点,不易发生燃烧、爆炸等危险,保证生产安全。 传统的粉料制备,树脂 丙酮搅拌将树脂分散,丙酮的闪点是 -17.8℃,即只要温 度等于或高于-17 .8℃,丙酮挥发出的气体遇火源即可燃烧发生危险。形成火源有多种情 况:明火,电弧(包括静电放电),撞击产生的火星另外丙酮的爆炸下限也很低:2.6%。粉未 放置于搅拌容器,搅拌过程再适当添加分散好的液体;搅拌过程与分散需注意事项相同,故 搅判过程为防止起火与爆炸发生,限制了搅拌条件(无法进行高速搅拌等),树脂不易包覆 粉未颗粒。 2)预备一体电感使用的线圈件,该线圈件包括有线圈; 3)预备一体电感使用的成型模具,所述成型模具包括上模、盖板、中模及底模,所 述上模设置有上冲头,所述底模设置有下冲头,所述盖板设置有上冲头导孔,该上冲头导孔 还作为进粉孔洞使用,所述中模设置有下冲头导孔,所述盖板的下侧设置有凹模部,所述中 模的上侧设置有凸模部,所述凸模部形成有成型模腔及卡位结构,使得线圈件放置到位后, 线圈与成型模腔相对应;所述凹模部与凸模部相适配,进行合模后,所述成型模腔分别与盖 5 CN 111599586 A 说 明 书 3/10 页 板的上冲头导孔、中模的下冲头导孔相对应; 4)将线圈件放置到中模的凸模部,然后盖板的凹模部与中模的凸模部进行合模, 使得线圈位于成型模腔内; 5)中模的凸模部与盖板的凹模部合模完成后,将粉料从盖板的进粉孔洞处进料, 使得设定的压制所需量的粉料进入成型模腔内; 6)粉料进料完成后,通过上模与底模的配合,对成型模腔内的粉料进行热压成型, 到达设定的压制所需时间后,退模取出一体电感。 进一步,还包括如下步骤:7)将取出的一体电感进行后续的保温定型。 在此需要说明的是,步骤2)中,线圈件的形式有两种,一种是无金属框架线圈,即 相对单个的线圈件,包括线圈部分和引脚部分,该种线圈放置到模具中,可以通过人工单个 逐一放置,也可以通过专用的放料装置,进行自动化放置,又可以通过相应的放料模具,排 列好后,一次性放置10个、20个、30个不等。另外一种是有金属框线圈,即后续所述的线圈料 片,采用料片的形式,可以将多个线圈预先做成料片,便于放置以及批量生产。本高效率一 体电感制造工艺对于两种线圈形式,都可适用。 在此还需要说明的是,所述凸模部的卡位结构,是使得线圈件放置到位后,对线圈 件起到一个固定、定位的作用;针对有金属框线圈、无金属框架线圈,其结构会略有不同。对 于无金属框架线圈,凸模部的卡位结构只需要针对线圈件的线圈引脚部分设置即可;对于 有金属框架线圈(即线圈料片),凸模部的卡位结构要同时针对框架部分和线圈引脚部分 (引脚连接部)进行设置。 步骤2)中,所述线圈件为线圈料片,所述线圈料片包括金属框架及设置在金属框 架上的线圈;相应地,步骤4)将线圈件放置到中模的凸模部,使得金属框架与卡位结构配合 到位。 再进一步,步骤2)中:所述金属框架呈条状,排列设置有两个以上的线圈;相对应 地,步骤3)中,所述上模排列设置有两个以上的上冲头,所述底模排列设置有两个以上的下 冲头,所述盖板排列设置有两个以上的上冲头导孔,该些上冲头导孔还作为进粉孔洞使用, 所述中模排列设置有两个以上的下冲头导孔,所述盖板的下侧排列设置有两个以上的凹模 部,所述中模的上侧排列设置有两个以上的凸模部。 再进一步,步骤2)中:所述条状的金属框架划分为两个以上的单元格,每个单元格 的两侧设置有引脚连接部;两个以上的线圈分别设置在各个单元格中,且每个线圈两端的 引脚分别与对应单元格两侧的引脚连接部相连接;步骤3)中:每个凸模部的两侧,对应金属 框架的每个单元格两侧的引脚连接部,设置有引脚连接部避让槽,相对应地,每个凹模部的 两侧设置有避让槽压槽部;所述避让槽压槽部与引脚连接部避让槽相配合,将引脚连接部 压紧密封。 再进一步,步骤3)中:所述上模与热压成型设备的上加热板相连接,所述底模与热 压设备的下加热板相连接。 一种实施所述工艺的高效率一体电感成型模具,其与线圈料片相配合使用,所述 线圈料片包括金属框架及设置在金属框架上的线圈;成型模具包括上模、盖板、中模及底 模,所述上模设置有上冲头,所述底模设置有下冲头,所述盖板设置有上冲头导孔,该上冲 头导孔还作为进粉孔洞使用,所述中模设置有下冲头导孔,所述盖板的下侧设置有凹模部, 6 CN 111599586 A 说 明 书 4/10 页 所述中模的上侧设置有凸模部,所述凸模部形成有成型模腔及卡位结构,使得线圈料片放 置到位后,金属框架与卡位结构相对应,线圈与成型模腔相对应,所述凹模部与凸模部相适 配,进行合模后,所述成型模腔分别与盖板的上冲头导孔、中模的下冲头导孔相对应。 进一步,所述金属框架呈条状,排列设置有两个以上的线圈;所述上模排列设置有 两个以上的上冲头,所述底模排列设置有两个以上的下冲头,所述盖板排列设置有两个以 上的上冲头导孔,该些上冲头导孔还作为进粉孔洞使用,所述中模排列设置有两个以上的 下冲头导孔,所述盖板的下侧排列设置有两个以上的凹模部,所述中模的上侧排列设置有 两个以上的凸模部。 进一步,所述条状的金属框架划分为两个以上的单元格,每个单元格的两侧设置 有引脚连接部;两个以上的线圈分别设置在各个单元格中,且每个线圈两端的引脚分别与 对应单元格两侧的引脚连接部相连接;每个凸模部的两侧,对应金属框架的每个单元格两 侧的引脚连接部,设置有引脚连接部避让槽,相对应地,每个凹模部的两侧设置有避让槽压 槽部;所述避让槽压槽部与引脚连接部避让槽相配合,将引脚连接部压紧密封。 进一步,所述凸模部的引脚连接部避让槽是卡位结构的一部分;相邻的两个凸模 部之间的间隙部亦是卡位结构的一部分。 进一步,所述引脚连接部呈T字形,所述引脚连接部避让槽呈T字形,所述避让槽压 槽部亦呈T字形。 本发明具有以下优点:研发出了高性能的专用粉料及相应的制备工艺,该粉料的 树脂固含量低,提高性能的同时,确保粉料的流动性;结合利用专门的粉料,去除掉采用冷 成型模具进行预成型冷压的步骤,减少一套冷压模具的使用,避免冷压成型过程中对电感 的损坏,提高成品率;无需将电感与粉料冷压成型为电感半成品的步骤,而是采用直接对处 于松散状态的粉料进行连贯性的加热塑形、热压固化定型,整个过程十分流畅,粉料塑形速 度极快,而且需要的保压时间短,保压定型20 秒左右便可提前取出,然后放到烘箱进行后 续的保温定型即可,这样便能快速地腾出成型模具,进行下一次的制造,提高生产效率。整 个制备过程最快20多秒便可完成,效率高,成品率高,而且质量更好。 下面结合附图说明与