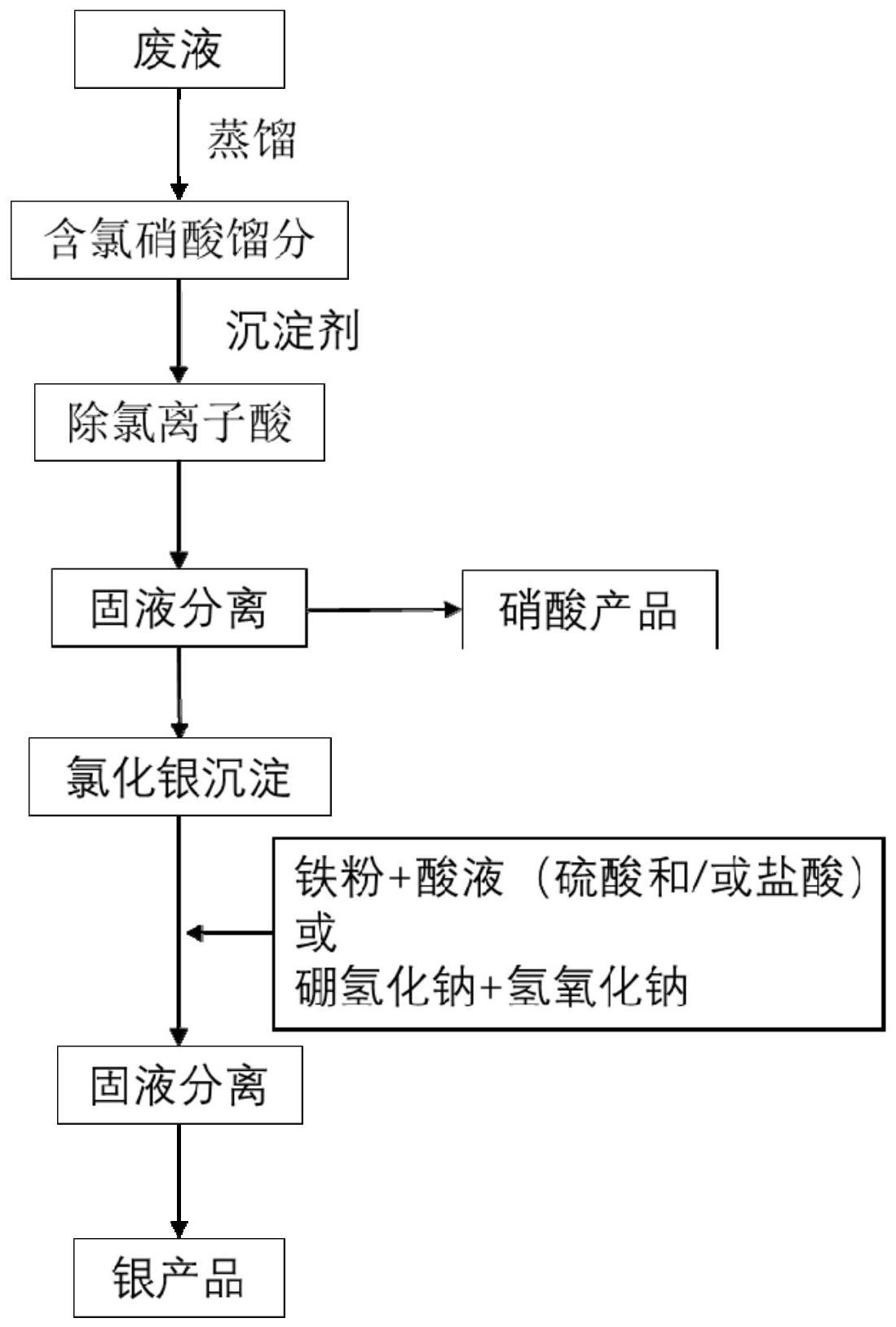
技术摘要:
本发明提供一种电极箔废液联产硝酸和银的方法,所述方法通过向经蒸馏预处理后的含氯硝酸馏分中加入沉淀剂将氯离子去除,制得硝酸产品,通过还原剂将氯化银沉淀还原,制得银产品,其中,含氯硝酸馏分中的氯离子能够达到较好的去除效果,制得的银可循环使用,操作过程简 全部
背景技术:
硝酸是常用的化工原料,电极箔的扩孔工艺和化学清洗工序都使用硝酸做主要原 料,硝酸清除孔洞中氯离子保障产品获得更高更稳定的电性能。工业上中和处理废硝酸的 方法造成了资源的浪费,又污染了环境,不符合节能减排的标准,这些处理方法也会对污水 处理系统造成冲击。 电极箔生产工艺产生的废硝酸中的杂质大部分不具挥发性,因此可采用蒸馏法将 杂质除去。经蒸汽预处理的废硝酸含有氯离子,氯离子去除方法主要有:化学沉淀法、絮凝 沉淀法、离子交换技术、电化学技术(包括电解法、电渗析法和电吸附法)、反透膜法、多孔填 料法、溶剂萃取法、水化硅酸盐法、水洗和焙烧法、紫外诱变法、蒸发浓缩法等。 以稀硝酸为主体的溶液酸性较强,大部分氯离子去除方法不适用。氯离子在此条 件下不易形成沉淀和絮凝物或形成后不稳定重新溶解,如超高石灰铝法生成的沉淀 Ca4Al2Cl4(OH)12需碱性条件;离子交换树脂或膜对酸的耐受能力有限且无法达到有效区分 NO3-和Cl-的效果,此外离子交换树脂需再生而使用膜成本较高;常用的硝酸萃取剂有磷酸 三丁酯(TributylPhosphate,TBP)、煤油、苯或甲苯等,TBP浓度越高,对硝酸的萃取有利,但 萃入有机相的盐酸量将急剧增加,选择性变差,于硝酸和盐酸的分离不利。 CN105731704A公开了一种污酸中去除氟、氯离子的处理方法,所述方法先浓缩污 酸(硫酸)再加热使所含的氟、氯离子形成氯化氢和氟化氢,挥发至蒸汽中除去,但此方法适 用于挥发性不强且沸点较高的酸,无法适用于硝酸的回收。 CN105905999A公开了一种三维电极电吸附去除硫酸体系氯离子的方法,该方法使 用钛板做阳极、铅板做阴极、活性炭填充于阳极区为第三电极,达到去除氯离子的目的,但 此方法耗电量较大、成本较高。 因此,如何对电极箔生产工艺产生的废硝酸进行最大化回用,是该生产过程亟待 解决的技术问题。
技术实现要素:
鉴于现有技术中存在的问题,本发明提供一种电极箔废液联产硝酸和银的方法, 所述方法通过蒸馏使废液中的硝酸和形成的盐酸和大部分水分被汽化分离,得到含氯硝酸 馏分,并以去除硝酸中氯离子提纯硝酸为目的,提供了一种能有效去除硝酸中氯离子保证 成品硝酸品质的方法,同时联产银产品并能够实现沉淀剂的循环使用。 为达此目的,本发明采用以下技术方案: 本发明提供一种电极箔废液联产硝酸和银的方法,所述方法包括如下步骤: (1)所述废液经蒸馏,得到含氯硝酸馏分; 4 CN 111573641 A 说 明 书 2/7 页 (2)所述含氯硝酸馏分中加入沉淀剂,固液分离,得到氯化银沉淀和硝酸产品; (3)所述氯化银沉淀经还原剂进行还原反应后固液分离,得到银产品。 本发明提供的电极箔废液联产硝酸和银的方法通过蒸馏预处理、沉淀和还原步 骤,能够回收电极箔废液中的硝酸,同时制得银产品,经济效益高,同时制得的银还可以作 为沉淀剂循环使用。该方法中,采用先蒸馏后沉淀法去除废液中的氯离子去除率高,制得硝 酸能够达到市售产品中氯离子的含量要求。 优选地,步骤(1)中所述废液中氯含量为30~40g/L,例如可以是30g/L、32g/L、 34g/L、35g/L、38g/L或40g/L等。 优选地,所述废液中总氢离子浓度为2.5~5g/L,例如可以是2.5g/L、3g/L、3.5g/ L、4g/L、4.5g/L或5g/L等。 优选地,所述含氯硝酸馏分中硝酸的质量浓度为15~30wt%,例如可以是15wt%、 17wt%、18wt%、19wt%、20wt%、24wt%、25wt%或30wt%等。 优选地,所述含氯硝酸馏分中的氯含量为3~10g/L,例如可以是3g/L、4g/L、5g/L、 6g/L、8g/L、9g/L或10g/L等。 优选地,步骤(1)中所述蒸馏的压力为-0.05~-0.07MPa,例如可以是-0.05MPa、- 0.055MPa、-0.056MPa、-0.058MPa、-0.06MPa、-0.065MPa或-0.07MPa等。 优选地,所述蒸馏的温度为70~90℃,例如可以是70℃、72℃、75℃、78℃、80℃、82 ℃、85℃、88℃或90℃等。 优选地,步骤(2)中所述沉淀剂包括硝酸银和/或银。 优选地,所述沉淀剂中银与含氯硝酸馏分中氯的摩尔比为0.9~1.1:1,例如可以 是0.9:1、0.95:1、0.99:1、1:1、1.01:1、1.05:1或1.1:1等,优选为1:1。 优选地,所述含氯硝酸馏分中加入沉淀剂后进行搅拌。 优选地,所述搅拌的时间为5~60min,例如可以是5min、8min、10min、20min、 30min、40min、50min或60min等。 优选地,步骤(3)中所述还原剂包括硼氢化钠或铁粉,优选为铁粉。 本发明中的还原剂优选为铁粉,这是因为硼氢化钠在还原过程中将产生氢气,处 理相对困难。 优选地,步骤(3)中所述还原剂为硼氢化钠时,加入氢氧化钠进行还原反应。 优选地,所述硼氢化钠与氯化银沉淀的摩尔比为0.9~1.1:1,例如可以是0.9:1、 0.95:1、0.99:1、1:1、1.01:1、1.05:1或1.1:1等,优选为1:1。 优选地,所述氢氧化钠与氯化银沉淀的摩尔比为1.8~2.2:1,例如可以是1.8:1、 1.85:1、1.9:1、1.95:1、2:1、2.05:1、2.1:1、2.15:1或2.2:1等。 优选地,步骤(3)中所述还原剂为硼氢化钠时,还原反应的时间为1.5~2.5h,例如 可以是1.5h、1.6h、1.7h、1.8h、1.9h、2h、2.2h或2.5h等。 优选地,步骤(3)中所述还原剂为硼氢化钠时,还原反应的温度为50~60℃例如可 以是50℃、52℃、54℃、55℃、56℃、58℃或60℃等。 优选地,步骤(3)中所述还原剂为铁粉时,加入酸液进行还原反应。 本发明采用铁粉进行还原时,优选在酸液体系中进行还原,还原率更高且铁粉不 会残留在银粉中,能够更好地提高银产品的纯度。 5 CN 111573641 A 说 明 书 3/7 页 优选地,所述酸液包括盐酸和/或硫酸,优选为盐酸。 优选地,所述铁粉与氯化银沉淀的摩尔比为0.5~1:1,例如可以是0.5:1、0.55:1、 0.6:1、0.65:1、0.7:1、0.75:1、0.8:1、0.85:1、0.9:1、0.95:1或1:1等,优选为0.55~0.8:1。 本发明优选控制铁粉与氯化银沉淀的摩尔比为0.55~0.8:1,能够更好地保障还 原效果和银的纯度。 优选地,所述酸液中酸与氯化银沉淀的摩尔比为1~5:1,例如可以是1:1、1.5:1、 2:1、2.5:1、3:1、3.5:1、4:1、4.5:1或5:1等。 优选地,步骤(3)中所述还原剂为铁粉时,还原反应的时间为2~4h,例如可以是 2h、2.5h、3h、3.5h或4h等。 优选地,步骤(3)中所述还原剂为铁粉时,还原反应的温度为20~60℃,例如可以 是20℃、25℃、30℃、35℃、40℃、45℃、50℃、55℃或60℃等。 优选地,步骤(3)中先加入酸液,升温至20~60℃后再加入铁粉进行还原反应,优 选升温至40~60℃。 本发明中优选先加入酸液,再升温至40~60℃最后再加入铁粉作为还原剂进行还 原反应,能够更充分的保障铁粉的还原效果,提高银的收率。 优选地,所述方法还包括:将所述银产品加入步骤(1)得到的含氯硝酸馏分中进行 沉淀反应。 优选地,所述沉淀反应的时间为0.5~1h,例如可以是0.5h、0.6h、0.7h、0.8h、0.9h 或1h等。 作为本发明优选的技术方案,所述方法包括如下步骤: (1)所述废液经-0 .05~-0 .07MPa、70~90℃蒸馏,得到硝酸质量浓度为15~ 30wt%,氯含量为3~10g/L的含氯硝酸馏分;其中,所述废液中氯含量为30~40g/L,所述废 液中总氢离子浓度为2.5~5g/L; (2)所述含氯硝酸馏分中加入银和/或硝酸银作沉淀剂,搅拌5~10min,固液分离, 得到氯化银沉淀和硝酸产品;其中,所述沉淀剂中银与含氯硝酸馏分中氯的摩尔比为0.9~ 1.1:1; (3)在所述氯化银沉淀中加入酸液,升温至20~60℃,再加入铁粉进行还原反应, 还原反应的时间为2~4h,还原反应后固液分离,得到银产品;其中,铁粉与氯化银沉淀的摩 尔比为0.5~1:1,酸液中酸与氯化银沉淀的摩尔比为1~5:1。 本发明对上述固液分离过程没有限制,可采用本领域技术人员熟知的任何可用于 固液分离的操作,例如可以是过滤、抽滤、压滤或离心分离等方式。 与现有技术相比,本发明至少具有以下有益效果: (1)本发明提供的电极箔废液联产硝酸和银的方法实现了电极箔生产过程中产生 的废硝酸的回收利用,避免了废硝酸中和处理造成的资源损失和填埋盐渣造成的环境负 担; (2)本发明提供的电极箔废液联产硝酸和银的方法其中硝酸中氯离子的去除过程 中,既可以联产银产品,银产品也可以作为氯离子沉淀剂实现循环利用,沉淀剂银的回收率 在82wt%以上,沉淀剂的回收率高达99.66wt%,银产品纯度在97wt%以上,极大的降低了 处理成本,所得硝酸中氯离子杂质去除率达99wt%以上; 6 CN 111573641 A 说 明 书 4/7 页 (3)本发明提供的电极箔废液联产硝酸和银的方法通过铁粉和酸液体系还原氯化 银,还原效率高且不产生其他气体,不存在铁粉残留。 附图说明 图1是本发明提供的电极箔废液联产硝酸和银的方法的流程示意图。