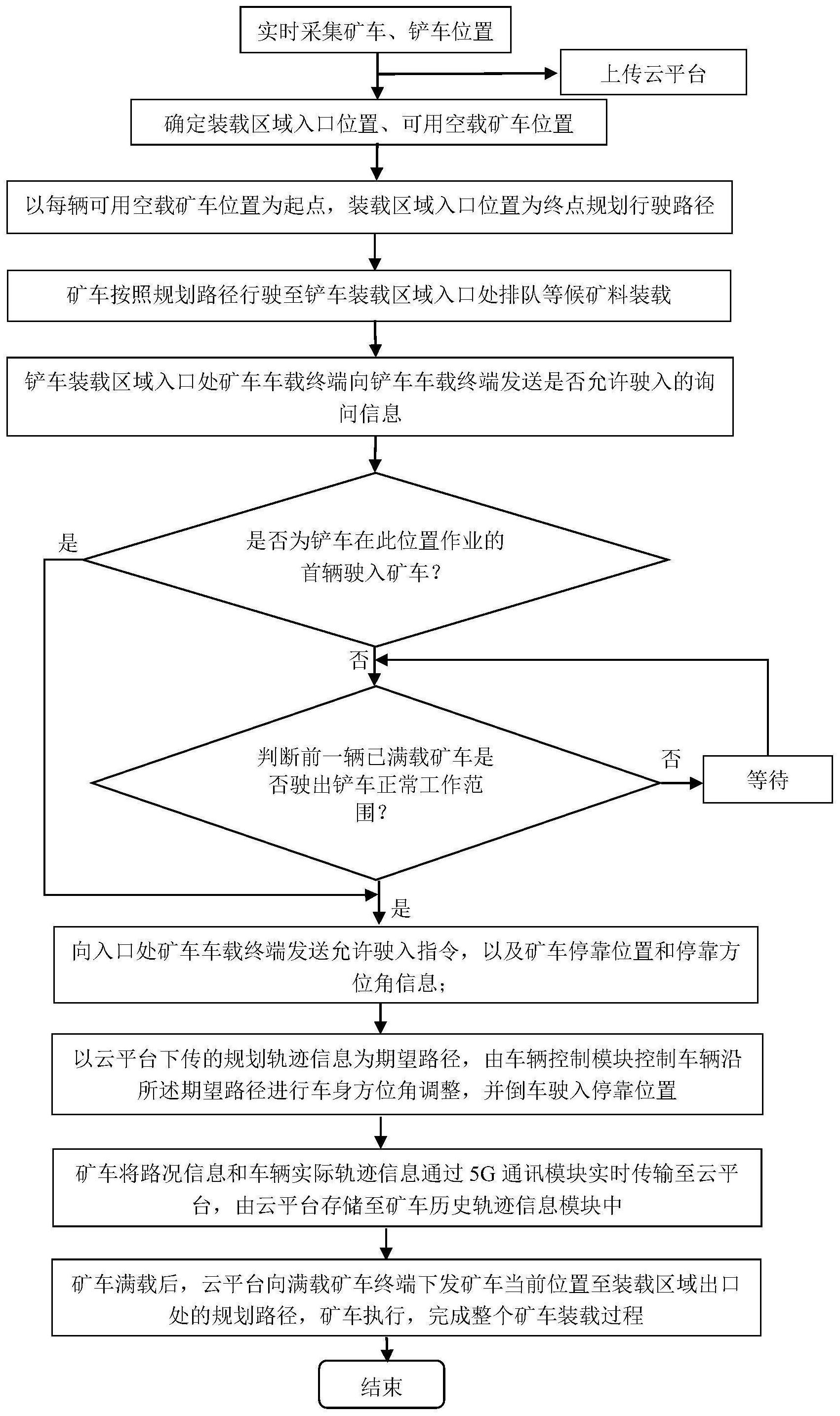
技术摘要:
本发明公开了一种基于5G的矿区无人运输系统及其矿铲车的协同控制方法,采用5G通讯模块高速率、低延时的绝对优势进行信息传输,实现了云平台与无人矿车、智能铲车的实时信息传输;本发明基于5G无人驾驶运输平台,通过定位技术、感知技术、路径规划技术和深度学习方法, 全部
背景技术:
随着传感器技术的快速发展,无人驾驶技术逐步成熟,并已经率先在矿区等封闭 场景内落实应用,对传统矿山生产运营模式做出时代性改变。通常,矿区生产作业主要包括 穿孔、爆破、采装、运输和排土等流程,其中采装和运输流程是在铲车、矿车定位至安全区域 的基础上,由铲车挖掘矿料,并控制移动机械臂将其装载至矿车箱槽,由矿车按照规划路径 运输至目的地,整个开采运输过程依靠矿车与铲车之间的密切协同配合。但由于4G通讯设 备高延时和低速率的性能特点,车辆间的实时信息通讯受限,使得无人驾驶技术在矿区仅 实施于矿车或铲车等单车运输系统,车车协同作业尚需人工参与分配,生产效率较低,无法 满足智慧矿山生产作业流程一体化机制。 5G无人驾驶运输系统是5G多模通信技术与无人驾驶运输系统技术的深度融合。与 4G网络条件相比,5G通讯具备极高速率、极大容量以及极低时延的优势特性,满足无人驾驶 运输平台与矿、铲车以及矿车与铲车间信息通讯的实时性要求,保证矿车与铲协同作业的 有序进行。 为解决以上问题,建立基于5G无人驾驶运输系统的矿车与铲车协同控制方法成为 较理想的解决方案。本发明结合5G通讯技术优势以及矿车与铲协同作业的需求,提出一种 基于5G矿区无人运输系统及其矿车与铲车协同控制方法。
技术实现要素:
为了解决上述已有技术存在的不足,本发明提出一种基于5G的矿区无人运输系统 及其矿车与铲车协同控制方法,以提高矿区矿料开采与运输效率,实现矿车与铲车协同自 动化控制,本发明的具体技术方案如下: 基于5G的矿区无人运输系统,其特征在于,包括云平台、无人矿车、智能铲车,5G通 讯模块;所述无人矿车上安装第一车载终端、第一车辆感知模块、第一车辆控制模块以及第 一车辆定位模块,所述智能铲车上安装第二车载终端、第二车辆感知模块、第二车辆控制模 块、第二车辆定位模块以及第三车辆定位模块;其中, 所述云平台用于与所述无人矿车上的所述第一车载终端、所述智能铲车上的所述 第二车载终端信息交互、信息处理以及历史数据存储,并对所述无人矿车进行路径规划调 度; 所述5G通讯模块用于所述云平台与所述无人矿车、所述智能铲车进行信息传输; 所述第一车载终端用于接收和处理所述云平台、所述第一车辆感知模块、所述第 一车辆控制模块以及所述第一车辆定位模块的信息;所述第二车载终端用于接收和处理所 述云平台、所述第二车辆感知模块、所述第二车辆控制模块以及所述第二车辆定位模块的 4 CN 111600933 A 说 明 书 2/7 页 信息; 所述第一车辆感知模块和所述第二车辆感知模块均包括激光雷达和毫米波雷达, 用于感知周围环境信息; 所述第一车辆控制模块用于接收所述第一车载终端控制指令,控制所述无人矿车 自主行驶;所述第二车辆控制模块用于接收所述第二车载终端控制指令,控制所述智能铲 车自主行驶; 所述第一车辆定位模块为安装于所述无人矿车前端的GPS天线,通过串口连接在 所述第一车载终端的输入端,用于所述无人矿车定位; 所述第二车辆定位模块和所述第三车辆定位模块分别为安装于所述智能铲车铲 臂底座旋转中心和所述智能铲车铲臂与铲斗铰接部位的GPS天线,均通过串口连接在所述 第二车载终端的输入端,用于所述智能铲车铲臂底座旋转中心定位以及铲臂末端部位定 位。 基于无人运输系统的矿铲车协同控制方法,其特征在于,所述矿铲车协同控制方 法包括以下步骤: S1:无人矿车的第一车辆定位模块和智能铲车的第二车辆定位模块实时采集自身 位置信息,分别通过串口传输至所述第一车载终端和所述第二车载终端,并分别由第一车 载终端和第二车载终端通过5G通讯模块实时上传至云平台; S2:云平台处理更新步骤S1获取的位置信息,确定当前时刻智能铲车位置和所在 装载区域入口位置,以及可用空载无人矿车位置,其中,可用空载无人矿车位置由云平台内 部的调度模块基于整体矿区作业状态、装载区域矿料运载需求以及空载无人矿车位置路径 可达性确定; S3:云平台以步骤S2的当前时刻可用空载无人矿车位置为起点、装载区域入口位 置为终点规划行驶路径,并将规划路径分别发送至每辆空载无人矿车的第一车载终端; S4:空载无人矿车由第一车辆感知模块感知路况、第一车辆控制模块控制车体按 照步骤S3的规划路径行驶至装载区域入口处排队等候装载矿料; S5:装载区域入口处空载无人矿车的第一车载终端向智能铲车的第二车载终端发 送是否允许驶入的询问信息; S6:装载区域入口处无人矿车为其在此位置停靠时间内的首辆驶入无人矿车,智 能铲车车载终端向首辆驶入无人矿车发送允许驶入指令、无人矿车停靠位置和停靠朝向信 息; 装载区域入口处无人矿车不是其在此位置停靠时间内的首辆驶无人入矿车,判断 前一辆已满载矿车是否驶出智能铲车正常工作范围,若已经驶出则向入口处无人矿车的第 一车载终端发送允许驶入指令、无人矿车停靠位置和停靠朝向信息,若尚未驶出则等待满 载矿车驶出智能铲车正常工作范围; 无人矿车停靠位置和停靠朝向信息的确定方法为: S6-1:以智能铲车铲臂底座旋转中心的GPS天线检测的正北方向为基准0°,智能铲 车的第二车载终端接收铲臂挖掘矿料时铲臂与铲斗铰接部位的GPS定位信息,确定此时铲 臂相对于正北方向的方位角θ1; S6-2:智能铲车的第二车辆控制模块控制铲臂向逆时针或顺时针方向旋转90°,智 5 CN 111600933 A 说 明 书 3/7 页 能铲车的第二车载终端接收此时铲臂末端定位信息,确定此时铲臂相对于正北方向的方位 角θ2; S6-3:步骤S6-2中智能铲车铲臂与铲斗铰接部位的定位信息即为无人矿车后车厢 中心停靠位置,无人矿车停靠朝向为垂直于智能铲车铲臂且无人矿车车头背对矿山的朝 向,无人矿车停靠位置能够通过无人矿车后车厢中心停靠位置及无人矿车停靠朝向共同确 定; S7:以云平台下传的规划路径信息为期望路径,由第一车辆控制模块控制无人矿 车沿期望路径按照停靠朝向驶入停靠位置; 若步骤S6装载区域入口处无人矿车不是首辆驶入无人矿车,则下传的规划路径信 息为前一辆无人矿车上传的历史轨迹;若步骤S6装载区域入口处无人矿车是首辆驶入无人 矿车,则所述下传的规划路径信息计算方法如下: S7-1:确定无人矿车可行驶的规划路径范围: 延伸无人矿车在所述装载区域入口处车身中部纵向轴线L1和无人矿车停靠位置 处的车身中部纵向轴线L2得到车头朝向夹角θ3,两轴线在夹角θ3之间的区域范围即为无人 矿车可行驶的规划路径范围; S7-2:确定规划路径范围内的可行驶路径集合Φ={p1,p2...,pn},p1,p2,...,pn分 别为n个可行驶路径,所有可行驶路径区段半径ri满足ri≥rmin,且路径坐标点(Xj,Yj,Zj)、矿 山边缘点(Xk,Yk,Zk)以及装载区域边缘点(Xl,Yl,Zl)满足条件(1),rmin为无人矿车车身的最 小物理转弯半径,d为最小安全距离,条件(1)为: S7-3:在可行驶路径集合中选取长度最小的路径作为下传的规划路径pchoose,即: pchoose=minΦ; S8:无人矿车按照期望路径行驶过程中,根据第一车辆感知模块实时感知周围路 况,并将路况信息和车辆实际轨迹信息通过5G通讯模块实时传输至云平台,由云平台存储 至无人矿车历史轨迹信息模块中; S9:无人矿车装载完成后,云平台向无人矿车的第一车载终端下发无人矿车装载 位置至装载区域出口处的规划路径,由无人矿车的第一车辆控制模块控制执行,完成整个 无人矿车装载过程,循环进入步骤S4。 本发明的有益效果在于: 1 .本发明采用5G通讯模块高速率、低延时的绝对优势进行信息传输,实现了云平 台与矿车、铲车的实时信息传输。 2.本发明基于5G无人驾驶运输平台,通过定位技术、感知技术、路径规划技术和深 度学习方法,确保无人驾驶矿车安全、精准地停靠在装载区域,实现了无人驾驶矿车与铲车 的高效、协同作业控制。 6 CN 111600933 A 说 明 书 4/7 页 附图说明 为了更清楚地说明本发明实施例或现有技术中的技术方案,下面将对实施例中所 需要使用的附图作简单地介绍,通过参考附图会更加清楚的理解本发明的特征和优点,附 图是示意性的而不应理解为对本发明进行任何限制,对于本领域普通技术人员来讲,在不 付出创造性劳动的前提下,可以根据这些附图获得其他的附图。其中: 图1为本发明工作流程图; 图2为本发明的基于5G的无人运输系统示意图; 图3为本发明智能铲车的定位模块安装位置图; 图4为本发明无人矿车停靠位置和停靠朝向信息确定方法示意图; 图5为本发明无人矿车可行驶规划路径确定方法示意图。 附图标号说明: 1-智能铲车铲臂;2-智能铲车铲斗;3-智能铲车铲臂底座旋转中心的GPS天线;4- 智能铲车铲臂和铲斗铰接处的GPS天线;5-矿山物料;6-矿车后车厢中心;7-车头朝向;8-排 队等候的无人矿车。