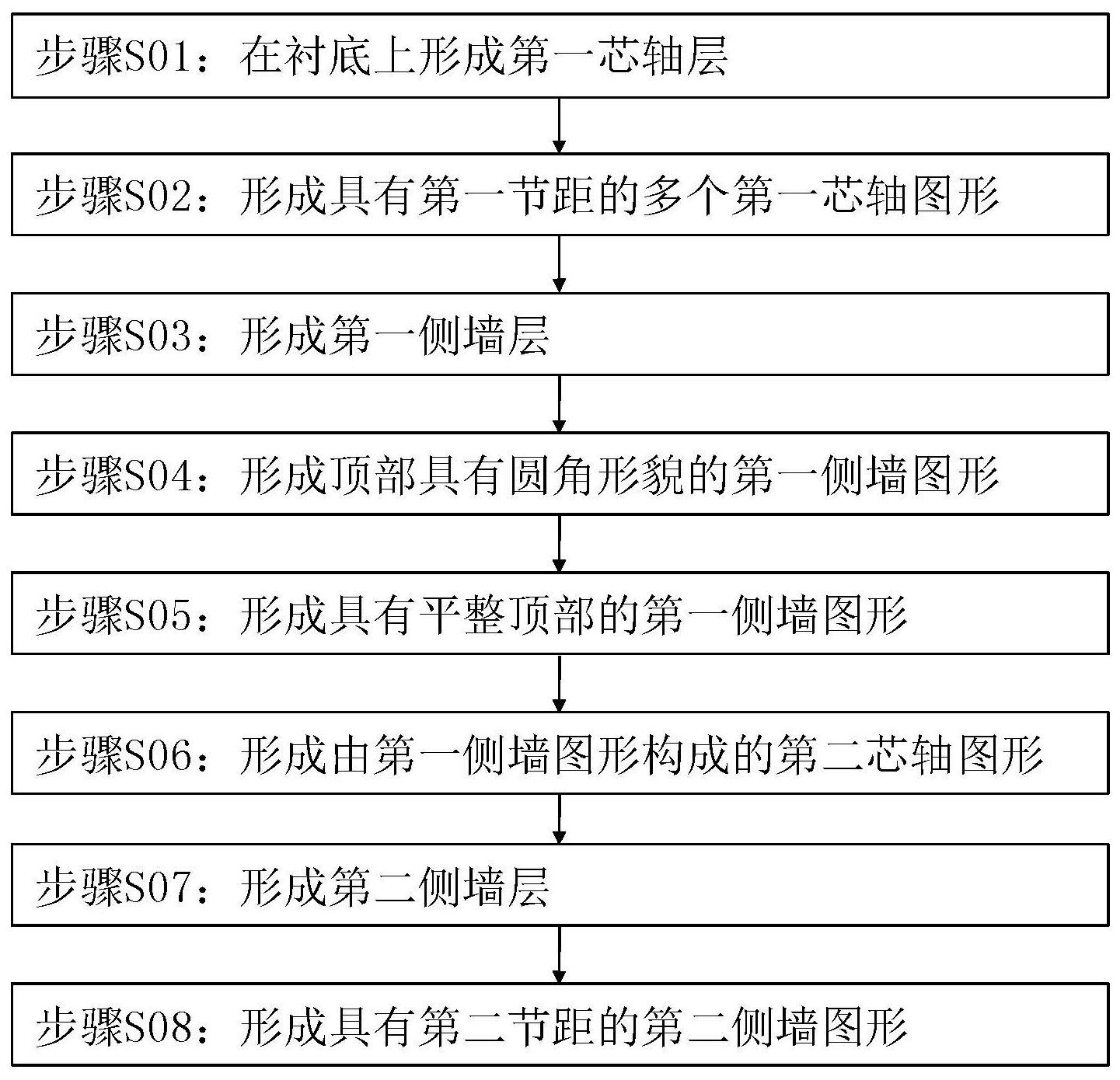
技术摘要:
本发明公开了一种自对准四重图形形成方法,包括:在衬底上形成第一芯轴层并图形化,形成第一芯轴图形;在第一芯轴图形表面上均匀形成第一侧墙层;去除第一芯轴图形顶部的第一侧墙层材料,在第一芯轴图形侧壁上形成第一侧墙图形;进行牺牲层的填充和平坦化,露出第一芯 全部
背景技术:
随着芯片尺寸的持续微缩,在进入三维鳍式场效应晶体管(FinFET)技术时代后, 特别是从7nm节点开始,由于图形周期(如鳍(Fin)尺寸为7nm,节距(pitch)为30nm)已经超 过193nm浸没式光刻机的曝光极限,故引进了自对准四重成像技术(Self-Aligned Quadruple Patterning,SAQP)来定义图形,如用于定义鳍的图形或后段金属层的图形均采 用这种图形方法。 请参考图1-图10,图1-图10是一种传统的自对准四重图形技术的工艺流程结构示 意图。如图1-图10所示,该传统的自对准四重图形技术的工艺流程包括: 如图1所示,自下而上依次形成第一氧化硅层10、第一不定形硅层11、第二氧化硅 层12、第二不定形硅层13以及有机复合阻挡层(包括SOC(碳涂层)14、SiARC(含Si的抗反射 涂层)15和光刻胶层16),并采用193nm浸润式光刻工艺进行光刻胶显影; 如图2所示,刻蚀形成第二不定形硅芯轴图形13’; 如图3所示,在第二不定形硅芯轴图形13’上形成第一氮化硅侧墙层17; 如图4所示,刻蚀形成第一氮化硅侧墙图形17’,并去除第二不定形硅芯轴图形 13’; 如图5所示,刻蚀形成第二氧化硅图形12’和第一不定形硅芯轴图形11’; 如图6所示,进行碳涂层18沉积; 如图7所示,进行碳涂层18背刻,露出第二氧化硅图形12’; 如图8所示,去除第一氮化硅侧墙图形17’和第二氧化硅图形12’,并去除碳涂层 18; 如图9所示,在第一不定形硅芯轴图形11’上形成第二氮化硅侧墙层19; 如图10所示,刻蚀形成第二氮化硅侧墙图形19’,并去除第一不定形硅芯轴图形 11’,在第一氧化硅层10上形成以第二氮化硅侧墙图形19’为硬掩模,节距为原光刻胶图形 节距1/4的规则图形。 然而,上述传统的SAQP技术在形成第一氮化硅侧墙图形时,一般是采用干法刻蚀 的方法,在进行非等向性刻蚀(各向异性刻蚀)的同时,会造成第一氮化硅侧墙图形17’顶部 的侧墙削角问题,从而在第一氮化硅侧墙图形17’顶部的单侧形成圆角171。由于该圆角171 的产生,使第一氮化硅侧墙图形17’成为不规则形状图形,因此第二氮化硅侧墙层19不能直 接沉积在第一氮化硅侧墙图形17’上。否则后续工艺没办法控制,必须再通过干法刻蚀进行 图形传递,以形成顶部平整的第一不定形硅芯轴图形11’,然后再进行第二氮化硅侧墙层19 的沉积和刻蚀。但这样做的缺点是图形层次和工艺都较为复杂,并且进行第一不定形硅芯 轴图形11’传递时的刻蚀负载效应会明显增大,容易造成图形传递时的尺寸偏差(即图形节 3 CN 111584430 A 说 明 书 2/5 页 距发生横向位移(pitchwalking)),由此增大了工艺控制难度。
技术实现要素:
本发明的目的在于克服现有技术存在的上述缺陷,提供一种自对准四重图形形成 方法。 为实现上述目的,本发明的技术方案如下: 一种自对准四重图形形成方法,包括以下步骤: 步骤S01:提供一衬底,在所述衬底上形成第一芯轴层; 步骤S02:图形化第一芯轴层,形成具有第一节距的多个第一芯轴图形; 步骤S03:在所述第一芯轴图形表面上均匀形成一第一侧墙层; 步骤S04:去除所述第一芯轴图形顶部的所述第一侧墙层材料,在所述第一芯轴图 形侧壁上形成顶部具有圆角形貌的第一侧墙图形; 步骤S05:进行牺牲层的填充和平坦化,露出所述第一芯轴图形和第一侧墙图形的 顶部,并进一步通过平坦化,消除所述第一侧墙图形顶部的圆角形貌,形成具有平整顶部的 所述第一侧墙图形; 步骤S06:去除牺牲层和所述第一芯轴图形,在所述衬底上形成由所述第一侧墙图 形构成的第二芯轴图形; 步骤S07:在所述第二芯轴图形表面上均匀形成一第二侧墙层; 步骤S08:采用侧墙刻蚀工艺,在所述第二芯轴图形侧壁上形成第二侧墙; 步骤S09:去除所述第二芯轴图形,在所述衬底上形成具有第二节距的所述第二侧 墙图形。 进一步地,步骤S02具体包括:在所述第一芯轴层上形成阻挡层和光刻胶层,进行 光刻胶显影,通过依次刻蚀所述阻挡层和第一芯轴层,对所述第一芯轴层进行图形化,并露 出所述衬底,然后去除剩余的所述阻挡层材料,形成所述第一芯轴图形。 进一步地,所述阻挡层为有机复合刻蚀阻挡层,所述有机复合刻蚀阻挡层含有碳 涂层和抗反射涂层,所述碳涂层包括不定形碳涂层或含碳的有机旋涂涂层。 进一步地,采用灰化工艺和湿法清洗工艺,去除剩余的所述碳涂层材料。 进一步地,步骤S02、步骤S08和步骤S09在同一个反应腔体内进行。 进一步地,所述反应腔体为电感耦合等离子体反应腔体。 进一步地,步骤S03和步骤S07中,采用原子层沉积工艺形成所述第一侧墙层和第 二侧墙层。 进一步地,步骤S05中,采用流动化学气相沉积工艺,进行所述牺牲层的填充。 进一步地,步骤S05中,采用化学机械研磨工艺进行平坦化,并利用过研磨消除所 述第一侧墙图形顶部的圆角形貌。 进一步地,步骤S06中,采用湿法刻蚀工艺,去除所述牺牲层和第一芯轴图形。 本发明能够有效解决现有技术存在的工艺复杂,工艺控制难度大的问题,并具有 以下技术优点: (1)图形结构简单,膜层沉积层次较少,使工艺步骤得到明显简化。 (2)减少了现有技术中原有第一氮化硅侧墙图形(第一侧墙图形)到第一不定形硅 4 CN 111584430 A 说 明 书 3/5 页 芯轴图形(第二芯轴图形)之间的图形传递步骤,由此减少了由于刻蚀造成的尺寸偏差,从 而明显降低了工艺控制难度。 附图说明 图1-图10是一种传统的自对准四重图形技术的工艺流程结构示意图。 图11是本发明一较佳实施例的一种自对准四重图形形成方法流程图。 图12-图20是本发明一较佳实施例的一种自对准四重图形形成方法的工艺流程结 构示意图。