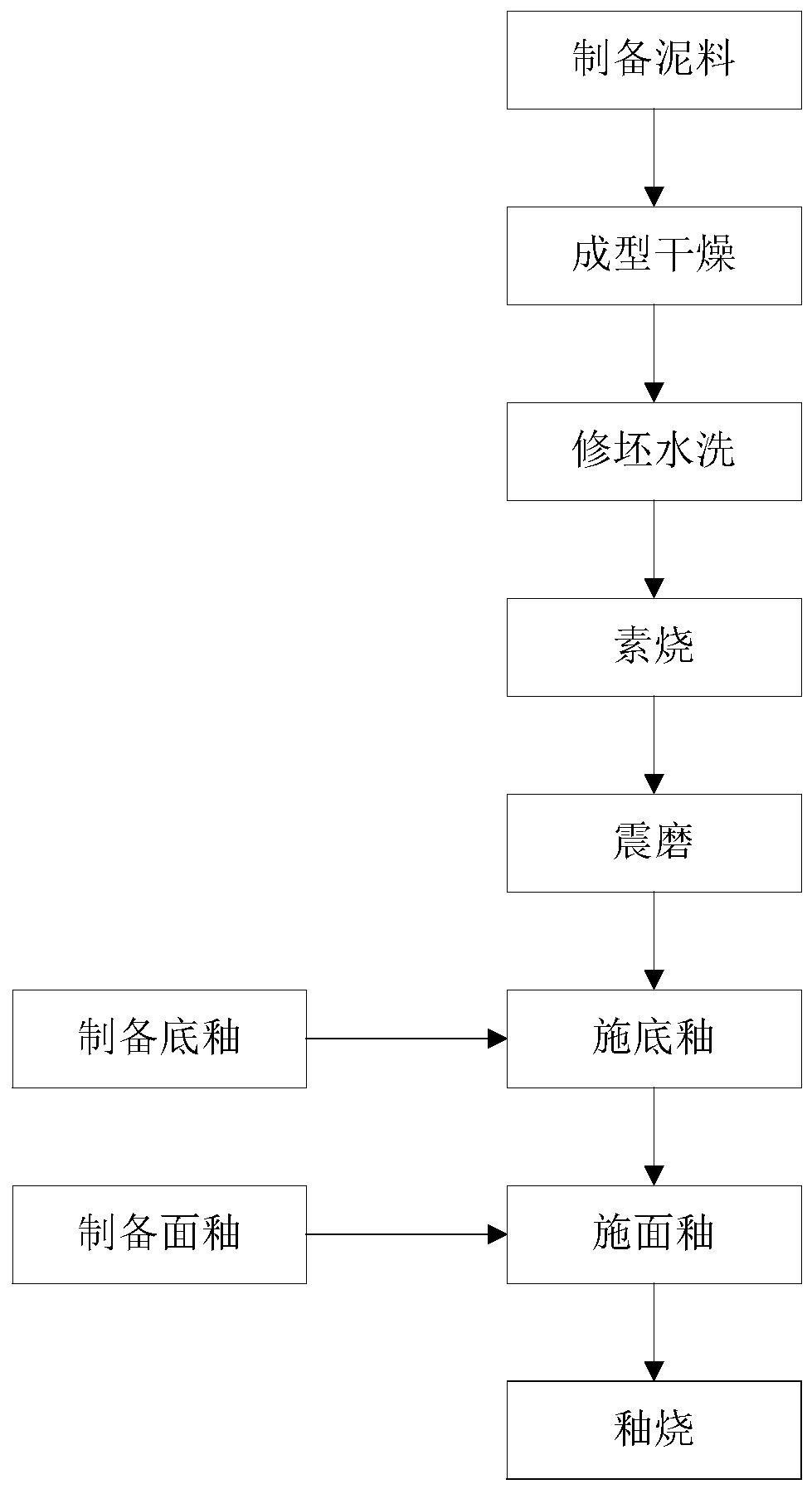
技术摘要:
本发明公开了一种釉料喷涂系统,通过电控机箱控制机械臂调整喷涂组件的位置,结合电控机箱控制喷涂夹持装置旋转进而带动待喷涂瓷器旋转,实现对待喷涂瓷器多方位喷涂,保证待喷涂瓷器的整体喷釉均匀,提高喷涂效率,保证喷涂质量。本发明还公开了一种窑变釉薄胎瓷器及 全部
背景技术:
传统的陶瓷表面装饰方法是在陶瓷制品表面上釉,釉层光滑、亮度高,既可使陶瓷 制品外观更美,又可以增加其耐受度。窑变釉即器物在窑内烧成时,由于窑中含有多种呈色 元素,经氧化或还原作用,出窑后呈现意想不到的釉色效果。但现有技术生产出来的窑变釉 瓷,大多数是人工向坯体喷涂釉料、生产效率低,釉层喷涂不均匀、釉面易有针孔瑕疵、釉面 粗糙等缺陷。
技术实现要素:
本发明旨在一定程度上解决相关记述中的技术问题。为此,本发明的一个目的是 提供一种釉料喷涂系统、窑变釉薄胎瓷器及其制备方法,制备得到的瓷器釉层喷涂均匀、釉 面光滑、美观大方。 为实现上述目的,第一方面,本发明提供了一种釉料喷涂系统,包括喷涂夹持装置 和喷涂机器人,所述喷涂夹持装置包括伺服电机和横梁,所述横梁中心底部设有转轴,所述 伺服电机通过转轴与所述横梁转动连接,所述横梁的两端分别安装有支架,所述支架上设 置有旋转支撑单元,所述旋转支撑单元包括用于放置待喷涂瓷器的第一转盘和位于所述第 一转盘顶面上、用于夹持待喷涂瓷器的夹持组件;所述喷涂机器人包括电控机箱、釉料箱、 喷涂组件和机械臂,所述电控机箱与所述喷涂夹持装置电性连接,所述釉料箱用于储存釉 料,所述喷涂组件与所述釉料箱连通,所述喷涂组件用于喷出釉料,所述机械臂设置在所述 电控机箱上,用于调整所述喷涂组件的位置,所述喷涂组件设置在所述机械臂上。 作为上述方案的进一步改进,所述横梁两端的顶部安装分度盘,所述分度盘上固 定有第二转盘,所述第二转盘的两端分别设置有所述第一转盘,所述第二转盘顶面两侧分 别安装有第一齿轮,通过所述第一齿轮与所述第一转盘连接,带动所述第一转盘转动。 作为上述方案的进一步改进,所述旋转支撑单元还包括电机和第二齿轮,所述电 机安装在所述支架上,所述第二齿轮设置在所述第二转盘上,所述电机的输出轴穿过所述 第二转盘与第二齿轮连接,所述第二齿轮与所述第一齿轮啮合。 第二方面,本发明提供了一种窑变釉薄胎瓷器,包括坯体和设置在坯体表面的底 釉层和面釉层, 所述坯体的组分及各组分的质量百分比为:骨灰20%~58%、长石8%~22%、高岭土25%~ 45%、石英9%~20%; 所述底釉层的组分及各组分的质量百分比为:熔块70%~75%、高岭土5%~8%、氧化锌4%~ 7%、碳酸钡1%~2%、三氧化二铁10%~13%; 所述面釉层的组分及各组分的质量百分比为:熔块70%~75%、高岭土5%~8%、氧化锌4.5% 4 CN 111571786 A 说 明 书 2/8 页 ~6.5%、碳酸钡1.2%~2.5%、钛白粉4.5%~6%、骨粉2.5%~4.5%、三氧化二铁1%~2%、氧化钴1%~ 2%。 作为上述方案的进一步改进,所述底釉层主要化学成分包括:SiO2、Fe2O3、Al2O3、 B2O3、Na2O、ZnO、BaO、CaO、K2O,所述底釉层主要化学成分的重量百分比为:SiO2 45%~50%、 Fe2O3 10%~13%、Al2O3 10%~12%、B2O3 9%~11%、Na2O 6%~8%、ZnO 4%~7%、BaO 1%~2%、CaO 1%~ 2%、K2O 0.4%~1.2%。 作为上述方案的进一步改进,所述面釉层的主要化学成分包括:SiO2、Al2O3、B2O3、 Na2O、ZnO、TiO2、CaO、BaO、Fe2O3、Co3O4、P2O5,所述面釉层主要化学成分的重量百分比为: SiO2 45%~50%、Al2O3 9%~12%、B2O3 8%~11%、Na2O 7%~9%、ZnO 4.5%~6.5%、TiO2 4.5%~6%、CaO 2.2%~3.8%、BaO 1.2%~2.5%、Fe2O3 1%~2%、Co3O4 1%~2%、P2O5 1%~2%。 作为上述方案的进一步改进,所述底釉层的厚度为0.2mm至0.5mm,所述面釉层的 厚度为0.3mm至1.0mm。 第三方面,本发明还提供了一种窑变釉薄胎瓷器制备方法,用于制备第一方面所 述的窑变釉薄胎瓷器,所述方法包括步骤: 制备泥料,按照瓷器坯体原料配方进行配比称重,加入水,搅拌均匀后进行球磨,制成 瓷器坯体泥料; 制备底釉:按照底釉层原料配方进行配比称重,入球湿式球磨,制成底釉釉浆,检测所 述底釉釉浆细度是否达到底釉釉浆细度阈值,若达到,则所述底釉釉浆过网筛,制成底釉; 制备面釉:按照面釉层原料配方进行配比称重,入球湿式球磨,制成面釉釉浆,检测所 述面釉釉浆细度是否达到面釉釉浆细度阈值,若达到,则所述面釉釉浆过网筛,制成面釉; 成型干燥:根据设计需要将所述瓷器坯体泥料压制成型,制成坯体并干燥处理; 修坯水洗:对所述坯体表面进行修边和水洗直到表面光滑; 素烧:将修坯水洗后的坯体放入窑内进行第一次烧制,得到素坯; 震磨:将所述素坯进行震磨抛光; 施底釉:采用第一方面所述的釉料喷涂系统在震磨后的素坯表面施一层底釉; 施面釉:待底釉干燥后,采用第一方面所述的釉料喷涂系统向底釉表面喷涂面釉; 釉烧:待面釉干燥后,将施有底釉和面釉的素坯放入窑内进行第二次烧制,得到窑变釉 薄胎瓷器。 作为上述方案的进一步改进,所述制备底釉步骤具体包括:按照底釉层原料配方 进行配比称重,将配制好的原料入球,加入水,进行湿式球磨,球磨时间为16小时至18小时, 制成底釉釉浆,检测所述底釉釉浆细度是否达到底釉釉浆细度阈值,所述底釉釉浆细度阈 值为300目至325目,若达到,则所述底釉釉浆过300目至325目的网筛,筛余小于0.2%,制成 底釉。 作为上述方案的进一步改进,所述制备面釉步骤具体包括:按照面釉层原料配方 进行配比称重,将配制好的原料入球,加入水,进行湿式球磨,球磨时间为16小时至18小时, 制成面釉釉浆,检测所述面釉釉浆细度是否达到面釉釉浆细度阈值,所述面釉釉浆细度阈 值为300目至325目,若达到,则所述面釉釉浆过300目至325目的网筛,筛余小于0.2%,制成 面釉。 作为上述方案的进一步改进,所述素烧步骤具体包括:将修坯水洗后的坯体放入 5 CN 111571786 A 说 明 书 3/8 页 窑内进行第一次烧制,烧制的温度为1200℃至1300℃,烧制的时间为10小时至13小时。 作为上述方案的进一步改进,所述釉烧步骤具体包括:待面釉干燥后,将施有底釉 和面釉的素坯放入窑内进行第二次烧制,烧制的温度为1100℃至1200℃,烧制的时间为9小 时至11小时,得到窑变釉薄胎瓷器。 本发明的有益效果是: 一种釉料喷涂系统,通过电控机箱控制机械臂调整喷涂组件的位置,结合电控机箱控 制喷涂夹持装置旋转进而带动待喷涂瓷器旋转,实现对待喷涂瓷器多方位喷涂,保证待喷 涂瓷器的整体喷釉均匀,解决现有的人工向坯体喷涂釉料、生产效率低的问题,提高喷涂效 率,保证喷涂质量。 一种窑变釉薄胎瓷器,采用独特的坯体、底釉和面釉配方,在高温中烧制,使瓷器 呈现出化学组成上的差异,从而呈现出黄红到蓝绿白等各种色调及多变的花纹、流纹等。与 现有技术相比,本发明制备得到的瓷器釉层釉面光滑、美观大方,降低产品加工成本。 一种窑变釉薄胎瓷器制备方法,通过二次烧成的方法,使得制备出的瓷器具有透 明度好、机械强度高、重量轻、瓷胎薄、声音清脆的优点,与现有技术相比,本发明制备得到 的瓷器釉层喷涂均匀、釉层釉面光滑、美观大方,降低产品加工成本。 附图说明 图1是本发明喷涂夹持装置实施例结构示意图; 图2是图1中A-A向剖视结构示意图; 图3是本发明夹持组件实施例结构示意图; 图4是本发明釉料喷涂系统实施例结构示意图。 图5是本发明窑变釉薄胎瓷器制备方法流程示意图。