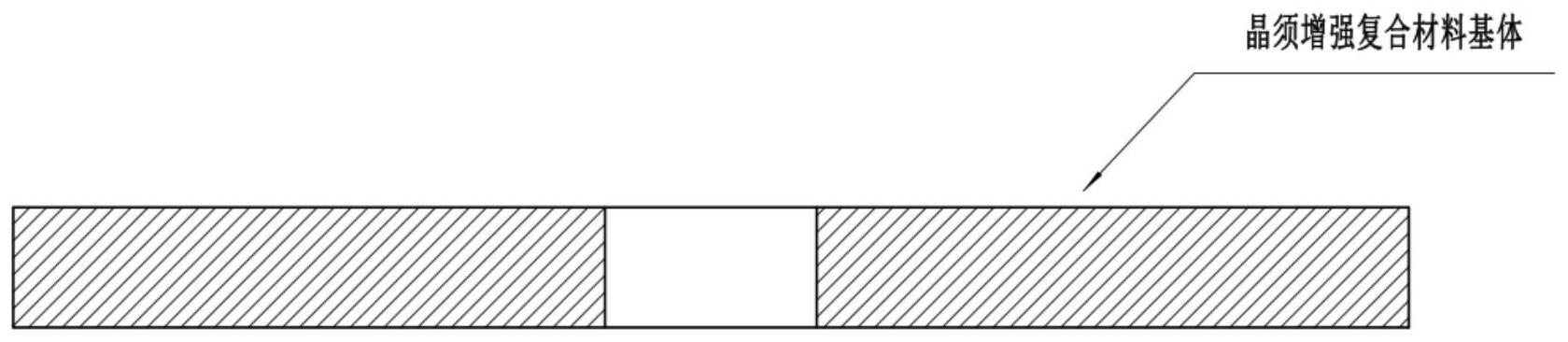
技术摘要:
本发明属于磨削磨具技术领域,具体涉及一种高速磨削砂轮用基体及其制备方法,还涉及一种超硬磨料砂轮。本发明的高速磨削砂轮用基体由以下质量百分比的原料制成:二元合金20~55%,单质金属5~15%,无机晶须5~40%,散热材料5~15%,玻璃纤维5~15%,石墨10~20% 全部
背景技术:
高速磨削(磨削速度大于80m/s)是一种高效高性能的加工方法,相比于普通磨削, 高速磨削在磨削效率、加工精度以及砂轮磨损方面都有着相当的优势。目前,常用的高速磨 削工具是超硬磨料砂轮,在高速磨削过程中超硬磨料砂轮充分发挥了超硬磨料(金刚石、立 方氮化硼)的高硬度、高锋利度的优势,对待加工工件实现精密、高效加工。 超硬磨料砂轮一般由磨料层和支撑磨料层的基体两大部分组成。其中磨料层一般 是由超硬磨料、结合剂(粘接剂和功能填料)、气孔组成。在高速磨削过程中,若要充分发挥 磨料层的高速锋利磨削,必须有与磨料层相匹配的基体。 现有的常用的超硬磨料砂轮基体一般是钢基体、铝基体、胶木基体以及碳纤维基 体等。在高速磨削过程中,钢基体、铝基体以及胶木基体都会发生不同程度的变形,容易与 磨料层脱离;碳纤维基体虽然不易变形,但是由于高速磨削会产生大量的热量,反复使用会 造成疲劳,最终容易造成损伤、断裂,使得砂轮的动平衡精度超差,造成砂轮磨削工件时易 产生震纹,且造成机床主轴的劳损。 因此,现有的基体由于在高速磨削过程中易出现变形、与磨料层脱离、断裂等现 象,已无法满足高速磨削的使用要求。
技术实现要素:
本发明的目的在于提供一种高速磨削砂轮用基体,该基体在高速磨削过程中不易 变形并且较好的动平衡性,能够应用于磨削速度大于120m/s的砂轮。 本发明的目的还在于提供一种上述高速磨削砂轮用基体的制备方法。 本发明的目的还在于提供一种采用上述高速磨削砂轮用基体的超硬磨料砂轮。 为实现本发明的目的,本发明采用的技术方案为: 一种高速磨削砂轮用基体,由以下质量百分比的原料制成:二元合金20~55%,单 质金属5~15%,无机晶须5~40%,散热材料5~15%,玻璃纤维5~15%,石墨10~20%,粘 接剂5~10%,润湿剂1~5%;所述二元合金为铁铜合金和/或镍钛合金;所述单质金属为 锡、铜、银中的一种或多种;所述散热材料为氧化锌、二硫化钼、冰晶石中的至少一种;所述 粘接剂为石蜡、酚醛树脂、水玻璃中的至少一种。 本发明的高速磨削砂轮用基体,所用二元合金为主要的金属相态结构材料,在基 体的制备过程中二元合金中的两种金属元素会发生金属相变,把其他原料一起牢固的把持 在一起,形成具有合适的强度、硬度的基体骨架结构。因此,二元合金属于支撑本发明的高 速磨削砂轮用基体的主要结合剂和基础结构。所用单质金属进一步增加了二元合金相变后 整体基体的韧性,降低整体基体的脆性,防止在高速旋转时,发生脆性断裂;单质金属还增 3 CN 111571464 A 说 明 书 2/6 页 加了整体基体的密度,从而增加整体基体的强度和硬度。 所用无机晶须和玻璃纤维具有两点作用:一、在组织结构中与二元合金一起形成 网络骨架结构,使整体材料具有很好的强度和韧性,增加抗冲击韧性和断裂强度;二、晶须 本身有一定的导热散热作用,在高负荷磨削时,基体传热分散效果好,不至于热力集中造成 局部机械强度降低。 所用散热材料具有较好的导热性能,并且还作为无机非金属颗粒均匀分散在金属 相中,能够降低金属基体的脆性,增加抗冲击韧性。 所用石墨的作用是在各原料反应时,增加二元合金的导热性,作为中间介质,使热 量分散均匀,促使反应均匀进行。 所用粘接剂为临时粘接剂,在制备过程中使各原料分散均匀,混合均匀。优选的, 所用粘接剂为石蜡、酚醛树脂、水玻璃中的至少一种。所用润湿剂使得各原料表面充分润 湿,保证了原料之间均匀结合。优选的,所用润湿剂在较低温度下具有粘性(即低温活性润 湿剂),在40℃温度时就会失去粘度,是临时润湿剂,其可以对二元合金和单质金属颗粒表 面进行充分润湿,更有利于粘接剂的粘接,使得各原料的混合均匀性,从而保证了砂轮基体 的组织均匀性。选择低温活性润湿剂是为了起到临时润湿作用,降低各种原料的表面活性, 有利于混料均匀性,且随着反应温度的升高,润湿剂失去活性,使其余各原料充分反应。进 一步优选的,本发明所用润湿剂为混合甲酚、硫化油、甘油中的一种或多种。 本发明高速磨削砂轮用基体中,各主要原料之间相互协调,形成了很好的金相组 织结构。本发明的砂轮基体具有硬度高,刚性好,热膨胀系数小,组织均匀,动平衡性能好的 优点,其各方面机械性能远优于普通的金属基体(铝、铜、钢等)和碳纤维基体。本发明的砂 轮基体适用于采用不同结合剂(陶瓷、树脂、金属结合剂)的超硬磨料砂轮,并且采用本发明 的砂轮基体的砂轮在磨削速度大于120m/s时仍能保证基体不变形、不发生断裂,满足高速 磨削的使用要求。 优选的,本发明的高速磨削砂轮用基体由以下质量百分比的原料制成:二元合金 20~25%,单质金属10~15%,无机晶须30~35%,散热材料5~10%,玻璃纤维5%,石墨 10%,粘接剂6~7%,润湿剂3~4%。 所述铁铜合金中铁与铜的质量比为85:15或70:30,镍钛合金中镍和钛的质量比为 65:35。 进一步优选的,所述二元合金为铁铜合金,所述单质金属为铜或锡;或者所用二元 合金为镍钛合金,所述单质金属为铜。采用上述种类的二元合金以及单质金属组合,有利于 提高金属相的结构均匀性,增加整体基体的强度、韧性和硬度。 本发明的高速磨削砂轮用基体中,为保证各原料的混合均匀性,所用二元合金、单 质金属以及散热材料均为粉料。 二元合金颗粒越小,有利于提高高速磨削砂轮用基体的硬度以及强度,优选的二 元合金的颗粒粒度为200~1000目。进一步优选的,所用二元合金的颗粒粒度为200~500 目。为提高粉料原料的混料均匀性,优选的所用单质金属的颗粒粒度为200~1000目,进一 步优选的所用单质金属的颗粒粒度为200~500目。优选的,所述散热材料的颗粒粒度为 2000~10000目,进一步优选的所用散热材料的颗粒粒度为2000~5000目。优选的,所用石 墨的颗粒粒度为100~1500目。进一步优选的,所用石墨的的颗粒粒度为100目、500目、1200 4 CN 111571464 A 说 明 书 3/6 页 目或1500目。进一步优选的,所用石墨为鳞片状石墨。 本发明的高速磨削砂轮用基体中,所用无机晶须优选为陶瓷质晶须和/或无机盐 晶须。优选的,所述无机盐晶须为硫酸钡晶须、硫酸钙晶须的一种或多种。优选的,所述陶瓷 质晶须为碳化硅晶须。 通过对无机晶须和玻璃纤维的尺寸的调整来提高其与其他原料的匹配程度,优选 的无机晶须的直径为10~50μm,长径比为5~25;进一步优选的无机晶须的直径为10~35μ m。优选的,所述玻璃纤维的直径为50~150μm,长径比为10~20;进一步优选的所用玻璃纤 维的直径为100~150μm。 本发明的高速磨削砂轮用基体的制备方法采用的技术方案为: 一种上述高速磨削砂轮用基体的制备方法,包括以下步骤:将各原料按质量百分 比混合、干燥得混合料;将混合料进行热压烧结,然后降温。 本发明的高速磨削砂轮用基体的制备方法简单,有利于大规模生产。 本发明的高速磨削砂轮用基体的制备方法中,各原料混合所用混合方法可以根据 实际进行调整,只需使各原料混合均匀即可。优选的,混合时采用球磨的方法混合,混合时 间为10~60min。 混合后在干燥过程中将粘接剂以及润湿剂除去,能够防止粘接剂以及润湿剂在后 续烧结过程中在高温下产生小分子气体逸出,造成基体出现气孔或者内部空洞。并且使其 余各原料保持干燥状态,有利于后续步骤的进行。优选的,所用干燥的温度为150~200℃, 时间为10~90min。 在热压烧结过程中,基体最终成型。优选的,所述热压烧结的压力为2~20MPa,温 度为550~600℃,时间为5~80min。 所述降温具体采用通风吹气方式进行降温,通风降温气动降温,风气温度为40~ 60℃,气流温度为5~10m/s,时间为10~25min。降温时通过控制通风条件对基体四周进行 降温,从而使基体缓慢降温,避免了直接由热压烧结时的温度降至室温时发生应力集中,从 而使得基体不会产生鼓泡,断裂,裂纹等内部暗伤。在降温过程中使得应力缓慢释放,从而 进一步保证了基体的良品率。 本发明的超硬磨料砂轮采用的技术方案为: 一种采用本发明的高速磨削用基体的超硬磨料砂轮。 以本发明的高速磨削用基体的超硬磨料砂轮,在磨削速度大于120m/s时仍具有较 好的磨削效果。 附图说明 图1为本发明的高速磨削用基体的截面示意图; 图2为采用本发明的高速磨削用基体制成的高速砂轮示意图。