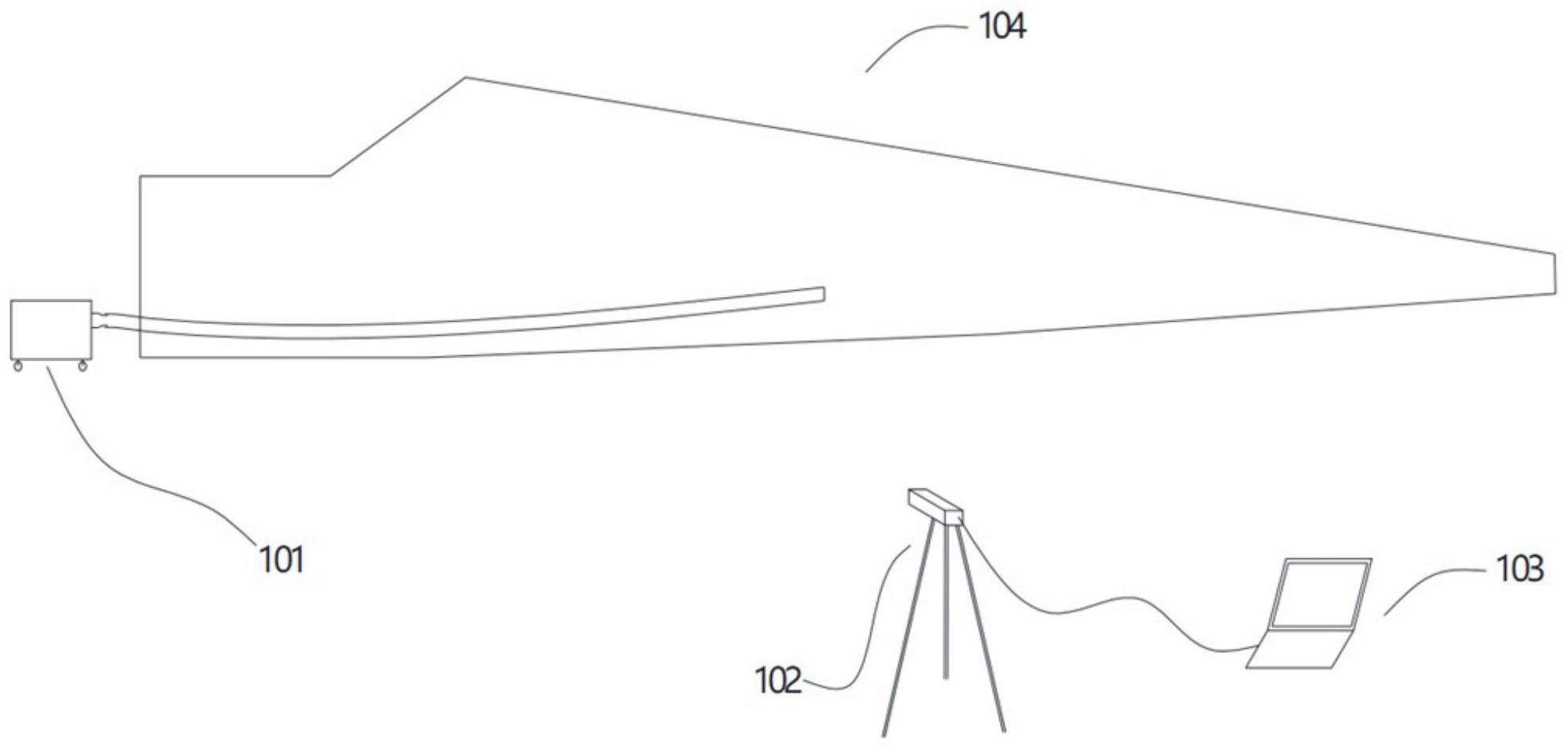
技术摘要:
本发明公开了一种风电叶片的红外无损检测方法及系统,结合红外热成像检测技术,使用激励热源对风电叶片的内腔及表面进行加热,在加热过程中,使用红外热成像设备对风电叶片进行动态检测,利用叶片不同结构,以及带有缺陷的结构在热传导过程中差异得到动态云图,通过对 全部
背景技术:
风电叶片是由复合材料制成的,叶片在风轮机的运行过程中,一方面叶片需要承 受很大的机械应力,另一方面会受到昆虫及各类脏物的吸附、沙蚀、雨蚀以及雷击等侵蚀, 这些因素都会导致风电叶片的复合材料以及结构的老化,主要表现为叶片的开裂,裂纹等 损伤,继而带来较大的安全隐患,并危及风电场运维人员的人身安全。而在叶片生产过程 中,由于风电叶片大多采用人工生产,自动化程度较低,在生产过程中也存在诸如空胶、褶 皱、壳体贫胶、芯材缺失、间隙等各种缺陷。而大部分缺陷存在于叶片复合材料的内部,从外 表面无法直观看出缺陷的类型、尺寸及程度。 目前市场上已发展出多种风电叶片的无损检测技术,较为成熟的例如红外热成 像、超声波、X射线等无损探伤技术,这些方法均可用于检测风电叶片的表面及内部缺陷,并 具有各自的优点及其局限性,例如超声波检测技术对于操作人员的技能要求较高,缺陷图 样不直观,另外检测速度较慢,无法适应快速检测的需求。而红外热成像检测技术虽然检测 速度快,但目前使用的红外热成像检测技术主要是通过分析静态的热成像云图数据判断缺 陷是否存在以及缺陷的类型,且需要结合大量的经验判断,因而检测结果的准确性有待进 一步提高。
技术实现要素:
本申请的目的在于一种风电叶片的红外无损检测方法,以提高检测的准确性。 为实现本发明的目的,本发明提供的一种风电叶片的红外无损检测方法,至少包 括如下步骤: S1 .将所述风电叶片基本呈水平状态或呈倾斜向上的状态进行布置,布置热风设 备并将所述热风设备的热风输出管路伸入所述风电叶片内腔内; S2.布置红外热成像设备,并调整所述风电叶片的倾斜角度,使所述红外热成像设 备的镜头对准所述风电叶片的待检区域; S3.开启所述热风设备,向所述风电叶片的内腔中持续输入预设温度及预设压力 的热风,利用所述热风对所述风电叶片自里向外进行加热,其中所述预设温度至少高于环 境温度,所述预设压力至少大于大气压力; S4.开启所述红外热成像设备,持续采集所述风电叶片待检区域自内部开始受热 至外表面温度稳定的温度场随时间变化的动态热成像云图数据; S5.提取并分析步骤S4中所采集的动态热成像云图数据的温度梯度特征,通过与 标准缺陷样品数据库的各项温度梯度缺陷特征进行对比,确定所述风电叶片待检区域是否 存在缺陷,以及缺陷的类型、尺寸及程度。 4 CN 111579591 A 说 明 书 2/5 页 优选地,步骤S5中,所述标准缺陷样品数据库在建立时,其中的各类标准缺陷样本 通过步骤S1至步骤S4进行动态热成像云图数据采集,并通过分析提取各温度梯度缺陷特 征。各类标准缺陷样本通过上述步骤进行测试后,形成缺陷动态热成像云图数据,根据待检 叶片的动态加热红外无损检测结果,通过图像计算对比分析进行缺陷归集,进行缺陷识别 判断。此外,对待检叶片进行动态加热红外无损检测时,应保证与标准缺陷样品的加热条 件,例如内外部激励热源选用的功率、加热温度、加热时间等,以及红外热成像设备的数据 采集频率、红外检测的检查距离、检测角度,均应保持一致或相当,以便于动态缺陷图形的 计算分析判断。 优选地,各类标准缺陷样本包括空胶、开裂和分层、褶皱、壳体贫胶、芯材缺失、间 隙标准缺陷样本,且每类标准缺陷样本均包括不同缺陷等级的样品。 优选地,步骤S5中,所述温度梯度特征、温度梯度缺陷特征的提取通过显著性检测 算法及图像形态学算法实现。 优选地,所述红外热成像设备使用30万像素以上,温度精度≤±2℃。 优选地,所述热风设备包括热风机和热风输出管路,所述热风机与热风输出管路 连接,所述热风输出管路延伸至所述风电叶片待检区域所对应的叶片内腔位置。 优选地,所述热风机带有温度调节装置,用以调节出口热风温度的大小。 优选地,步骤S3中,所述风电叶片待检区域的外部还设置有热辐射设备,所述热风 设备向所述叶片内腔输入热风的同时,所述热辐射设备对所述风电叶片待检区域的外表面 进行辐照加热,且所述辐照加热的温度不低于所述叶片内腔中热风的预设温度。 优选地,所述热辐射设备为闪光灯、卤素灯、激光设备或其他热源,所述热风设备 的出口热风温度以及所述热辐射设备的辐照加热温度的上限值均应保证不得对叶片的产 品质量造成影响。热辐射设备可根据检测的需要,对叶片的局部区域进行加热,加热时,调 整功率输出,在动态加热的情况下,通过红外热成像设备记录温度场变化情况。 优选地,在进行风电叶片的快速检测时,关闭所述热风设备,仅开启所述热辐射设 备对所述风电叶片待检区域的外表面进行辐照加热。 优选地,当所述风电叶片悬在空中时,利用吊舱携带所述红外热成像设备对所述 风电叶片进行近距离检查,或使用带有长焦镜头的红外热成像设备在地面对所述风电叶片 进行拍照检查。 本发明还提供了一种风电叶片的红外无损检测系统,其特征在于,包括激励热源、 红外热成像设备、计算机分析终端, 所述激励热源用于对风电叶片的内腔和/或表面进行加热; 所述红外热成像设备用于在所述激励热源加热过程中,使用红外热成像设备对风 电叶片进行动态检测,利用叶片不同结构,以及带有缺陷的结构在热传导过程中差异得到 动态云图; 所述计算机分析终端用于通过对热成像的动态云图温度梯度特征及标准缺陷样 品库温度梯度缺陷特征的对比分析,确定缺陷的类型、尺寸。 与现有技术相比,本发明的有益效果为,本发明的风电叶片的无损检测方法以及 系统结合红外热成像检测技术,使用激励热源对风电叶片的内腔及表面进行加热,在加热 过程中,使用红外热成像设备对风电叶片进行动态检测,利用叶片不同结构,以及带有缺陷 5 CN 111579591 A 说 明 书 3/5 页 的结构在热传导过程中差异得到动态云图,通过对热成像的动态云图及标准缺陷样品库温 度梯度缺陷特征的对比分析,确定缺陷的类型、尺寸;本发明的风电叶片的无损检测方法结 合红外热成像检测技术,基于风电叶片待检区域的动态热成像云图数据以及标准缺陷样品 数据库进行缺陷的识别和判断,较之现有热成像云图数据的判断识别方法,不仅检测速度 快,且检测结果的精度及准确性大大提高。 附图说明 图1所示为本发明的风电叶片红外无损检测系统的一种实施例示意图。