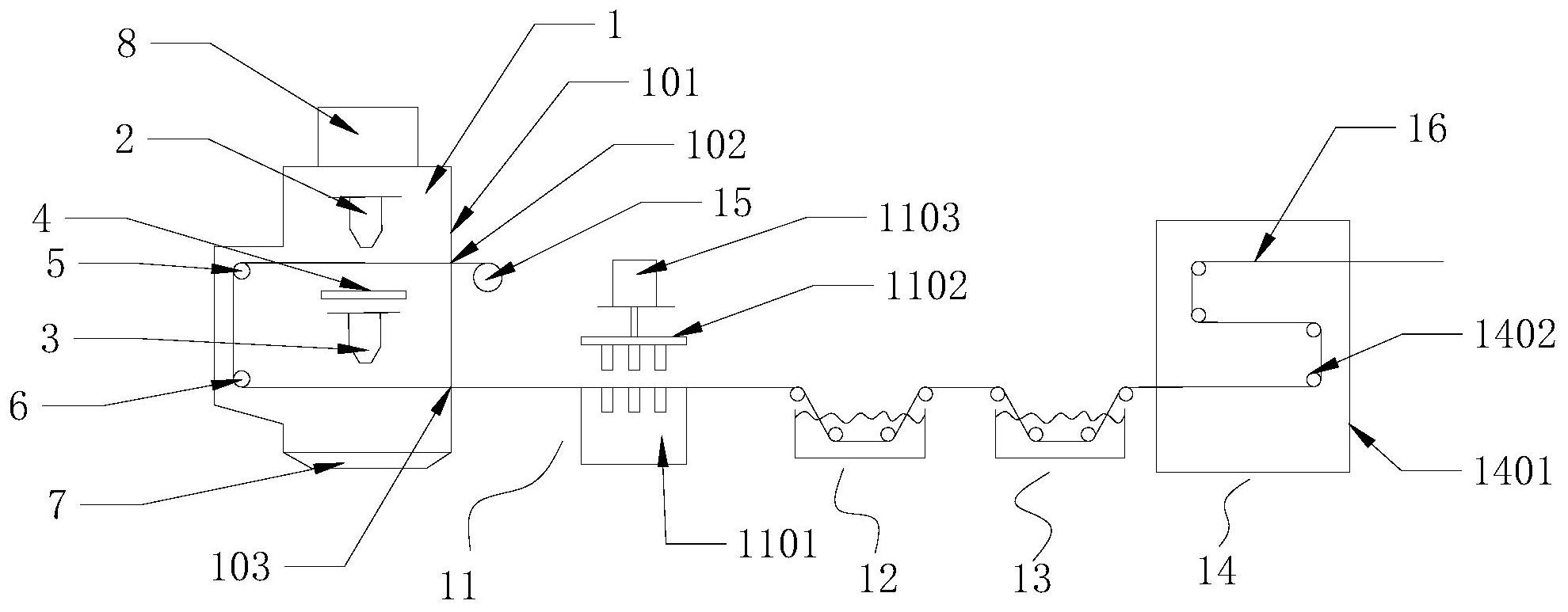
技术摘要:
本发明属于电极材料的技术领域,具体是涉及到一种粗糙度大的高比表面积的金属薄带制作装置,包括依次设置的喷砂室和电镀机构,所述喷砂室内设置有分别对金属薄带两面进行粗糙度处理的第一喷枪和第二喷枪,所述喷砂室上设置有入料口和出料口,喷砂室内位于入料口和出料 全部
背景技术:
目前制作电池正、负极片采用电镀金属薄带,尤其是钢带,其具有低成本、耐大电 流充放电等突出的优点,正在迅速取代发泡镍,成为动力电池的首选极板材料。 在用金属薄带制作电池时,需要将金属薄带上涂浆,将浆料固定在金属薄带表面, 目前采用的是光滑型金属薄带和毛刺型金属薄带,光滑型的金属薄带在涂浆附着时及其容 易打滑,成功率低,而通过机械冲孔人工制造毛刺的毛刺型金属薄带,通过冲模的形式人工 模拟,毛刺长短,控制不均一,在电镀过程中有可能造成金属毛刺上沉积球状金属或者毛刺 被碾压导致金属薄带表面未完全电镀金属层等其他缺陷,导致金属薄带进行热处理后,毛 刺边缘没有镍层附着或者毛刺形态不合格。在电池制造过程或者使用过程中,金属薄带人 为制造的毛刺在电池制造过程或者电池使用中也有可能会刺穿电池的隔膜,导致不良率增 加,两种金属薄带均有利有弊,但是又不能同时满足现有电池市场的需求。 目前在生产流水线中,很难既保证对金属薄带表面粗糙度进行均匀加粗,同时有 可以连续不断进行加工生产。部分会通过金属腐蚀的方式获取粗糙的金属薄带表面,但是 这个并不适用于电池用的金属薄带,因为金属薄带的基带如果没有电镀金属进行保护,对 其电池的电阻及相关反应会造成负效应,且其腐蚀的表面坑坑洼洼,与浆料的结合力并没 有得到有效的改善。如果金属薄带在电镀前的表面粗糙度过大会影响电镀沉积,不利于金 属沉积的均匀性,也不利于沉积金属与金属薄带的结合,可能会出现经过金属热处理后,电 镀金属与金属薄带脱离,粗糙度过小的话与光滑型金属薄带无异。
技术实现要素:
本发明要解决的技术问题是提供一种生产效率高,喷砂处理密封性好的粗糙度大 的高比表面积的金属薄带制作装置。 本发明的内容包括依次设置的喷砂室和电镀机构,所述喷砂室内设置有分别对金 属薄带两面进行粗糙度处理的第一喷枪和第二喷枪,所述喷砂室上设置有入料口和出料 口,喷砂室内位于入料口和出料口处设置有清扫机构,清扫机构包括第一隔离盒和设置在 第一隔离盒内位于金属薄带上方的驱动辊筒,驱动辊筒轴线与金属薄带移动方向平行。 更进一步地,所述第一隔离盒内位于金属薄带下方设置有滚刷,滚刷轴线与金属 薄带宽度方向平行。 更进一步地,所述第一隔离盒底部设置有回收通道,所述回收通道为迷宫通道。 更进一步地,所述喷砂室外位于出料口处设置有砂砾回收机构,金属薄带穿过砂 砾回收机构设置,所述砂砾回收机构包括第二隔离盒和设置在第二隔离盒且朝向金属薄带 两面的气嘴,所述第二隔离盒底部设置有回收孔。 3 CN 111590468 A 说 明 书 2/4 页 更进一步地,所述第二隔离盒内还设置有导向轮,导向轮高于出料口,所述出料口 靠近砂砾回收机构一侧设置有刷毛。 更进一步地,所述入料口和出料口设置在喷砂室同一侧,喷砂室另一侧设置有入 料口和出料口对应的第一导向辊和第二导向辊,第一喷枪设置在入料口和第一导向辊上 端,第二喷枪设置在入料口和第二导向辊上端。 更进一步地,所述第一喷枪和第二喷枪之间设置有分隔板。 本发明还包括设置在电镀机构与喷砂室之间的冲孔机构。 本发明还包括设置在电镀机构与喷砂室之间的水洗机构。 本发明还包括设置在电镀机构后的退火还原机构,所述退火还原机构包括退火炉 和导向组件,所述退火炉内设置有还原气体。 本发明的有益效果是,本发明设置喷砂室,对金属薄带的两面的表面粗糙度进行 均匀的加粗处理,表面在通过喷枪加粗后,再经过电镀机构进行表面电镀,使得电镀金属沉 积的时候形成一个特定的凸起形态,提高金属薄带表面粗糙度,增加其比表面积,喷砂室内 部侧壁上位于入料口和出料口位置设置有清扫机构,位于入料口侧的清扫机构对通过入料 口表面的金属薄带表面进行清扫,以避免影响表面粗糙度处理,位于出料口侧的清扫机构 对已经经过表面粗糙度处理的金属薄带的表面进行清扫,扫除位于表面的碎屑和喷砂的砂 砾,两个清扫机构同时保证喷砂室的相对密封度,保证工作环境的干净整洁,防止喷砂室内 引发的灰尘以及避免高速运动的喷砂通过入料口和出料口飞溅至喷砂室外。 附图说明 图1为本发明的结构示意图。 图2为本发明中清理机构和砂砾回收机构的结构示意图。 图3为本发明中清理机构和砂砾回收机构的立体剖视图。 图4为本发明中砂砾回收机构的部分结构示意图。 图5为本发明中清理机构和砂砾回收机构的正剖视图。 图6为通过本发明的电镀机构后金属薄带的SEM图。 图7为通过本发明的退火还原机构后金属薄带的SEM图。 图8为通过本发明的退火还原机构后金属薄带的SEM图。 图9为现有技术中常规金属薄带退火还原后的SEM图。 在图中,1-喷砂室;101-侧壁;102-入料口;103-出料口;104-刷毛;2-第一喷枪;3- 第二喷枪;4-分隔板;5-第一导向辊;6-第二导向辊;7-回收室;8-喷枪系统;9-清理机构; 901-第一隔离盒;902-滚刷;903-驱动辊筒;904-电机;905-入口;906-回收通道;9061-挡 板;10-砂砾回收机构;1001-第二隔离盒;1002-导向轮;1003-气嘴;1004-出口;1005-回收 孔;11-冲孔机构;1101-下模具;1102-下压模具;1103-动力机构;12-水洗机构;13-电镀机 构;14-退火还原机构;1401-退火炉;1402-导向组件;15-原料辊;16-金属薄带。