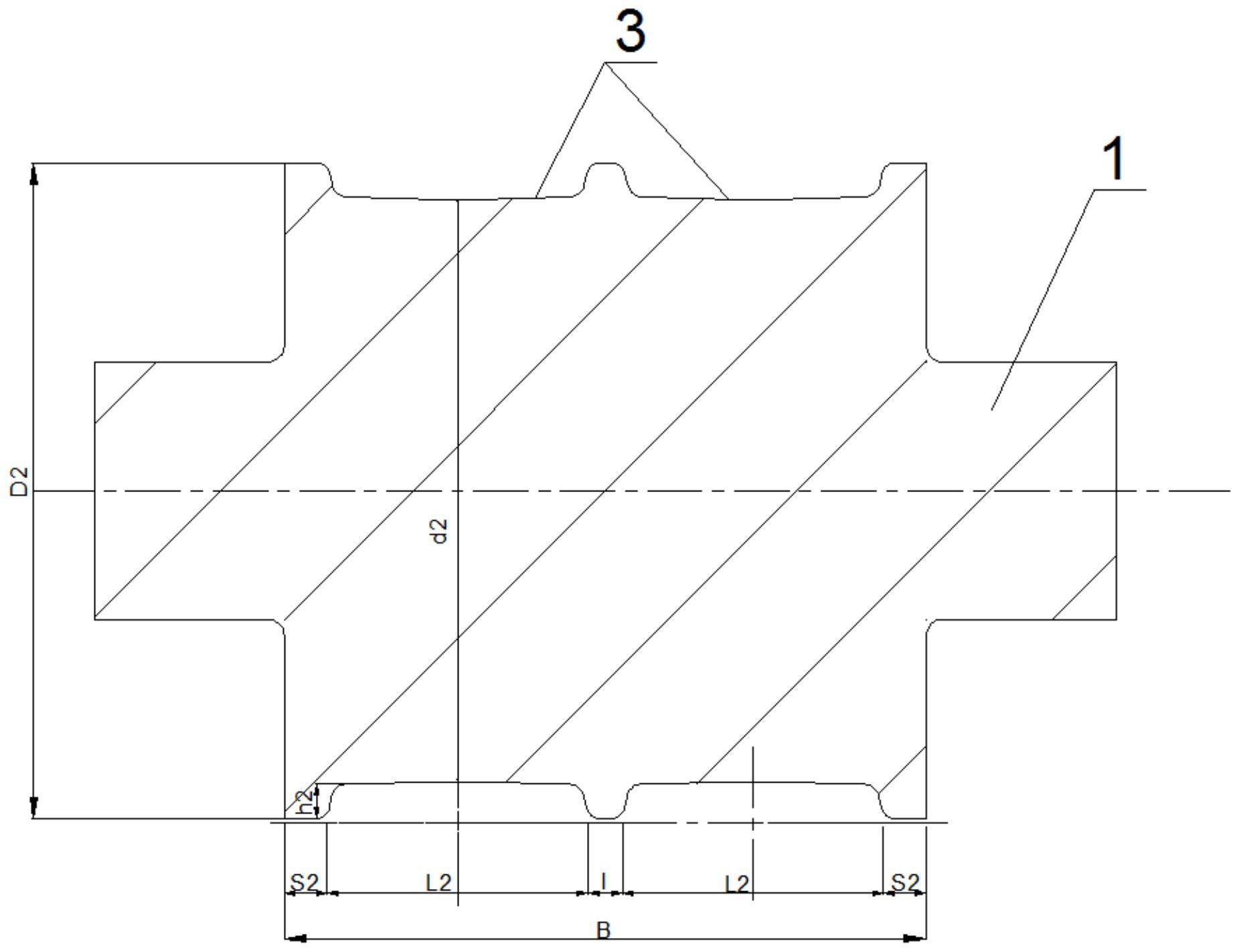
技术摘要:
本发明公开了一种在连轧机上使用的初轧潜孔型设计方法,属于轧钢技术领域,是针对现有轧辊辊身利用率低的现状所提出的,其具体步骤包括在不改变现有孔型侧壁斜度的情况下,减小现有孔型的刻槽深度;根据潜孔型的刻槽深度和潜孔型的数量,得出轧辊边缘的辊环宽度;在轧 全部
背景技术:
: 在轧钢长材生产领域,各生产企业为降低轧辊消耗,在孔型设计上运用了很多创 新方法,比较典型的是采用平辊无孔型轧制,取代连轧机初轧的箱型—箱型—椭圆型—圆 型孔型系统轧制,有效地降低了轧辊的吨钢消耗。但是,由于平辊无孔型轧制在变形过程 中,使轧件角部形成尖角,在后续过渡到圆形的过程中易形成表面折叠缺陷,因此,平辊无 孔型轧制仅适用于对表面质量要求不高的建筑材料使用,不适合特殊钢产品生产。在原料 使用上,平辊无孔型轧制仅适用于方形形状的连铸坯。 在特殊钢材生产领域,棒、线材连轧机所采用的初轧孔型多数为箱型—箱型—椭 圆型—圆型孔型系统,该孔型系统在生产中存在如下问题: (1)轧辊硬度层浪费 目前,特殊钢棒、线材连轧机所采用的的坯料规格较大,尤其是大规格棒材,坯料 规格更为突出,因此,对1、2架连轧机均采用箱型孔型的设计方式。由于箱型孔型的设计刻 槽较深,导致轧辊在车削孔型时,离表面层较近的高硬度层被车削掉,使轧辊高硬度层没有 得到充分利用。表面高硬度层被车削掉的轧辊,不仅降低了轧辊轧制的过钢量,增加轧辊吨 钢消耗,而且使孔型加工量大,增加车削工时。 (2)辊身利用率低 箱型孔型由于刻槽深,因此在孔型侧壁斜度固定的情况下,孔型外口的宽度大,在 布置孔型时,占用轧辊辊身的长度多,导致轧辊的辊身利用率低。 (3)轧辊重量大 由于箱型孔型刻槽较深,轧辊的辊身直径与工作直径差值大,因此,在保证轧辊工 作直径的前提下,轧辊的辊身直径也相应较大,增加了轧辊的重量。
技术实现要素:
: 本发明为克服现有连轧机初轧孔型在设计上存在的缺陷,提供了一种在连轧机上 使用的初轧潜孔型设计方法,该设计方将孔型刻槽深度减小,充分利用轧辊辊身的有效长 度,有效降低了轧辊重量。 本发明采用的技术方案在于:一种在连轧机上使用的初轧潜孔型设计方法,包括: 在轧辊的表面上加工有箱型状的孔型,所述孔型的侧壁为倾斜设置,具体包括以下步骤: 步骤1:根据现有孔型的刻槽深度,通过以下公式,确定潜孔型的刻槽深度,潜孔型 的侧壁斜度与现有孔型侧壁斜度相同, h2=1/2h1 式中:h2为潜孔型的刻槽深度,h1为现有孔型的刻槽深度; 3 CN 111581751 A 说 明 书 2/4 页 步骤2:根据潜孔型的刻槽深度和潜孔型的数量,得出应用潜孔型时轧辊边缘的辊 环宽度S2; 步骤3:在轧辊上布设潜孔型的数量,需满足S2≥h2要求; 步骤4:在轧辊工作直径相同的情况下,根据潜孔型的刻槽深度h2,通过以下公式, 确定轧辊直径; D2=d2 2h2 式中:D2为潜孔型的轧辊直径,d2为轧辊工作直径,h2为潜孔型的刻槽深度。 优选地,所述步骤1中,潜孔型的槽底为凹形底。 优选地,所述凹形底的设计方法为将两条直线与平直槽底倾斜设置,且直线平直 槽底间的夹角为α,在潜孔型的中间位置相交,将两条相交线用圆角过渡,形成潜孔型的凹 形底,所述潜孔型的凹形底与平直槽底的间距为N,过渡圆角半径R为孔型外口宽度的I倍, 即:R=I*L2。 优选地,所述α的取值范围为1~2°,N的取值范围为2~3mm,所述I的取值为3。 优选地,所述步骤5:在轧辊长度和轧辊工作直径不变的情况下,应用潜孔型后通 过以下公式可得出减少的轧辊重量 W=π*(D 2 21 /4-D2 /4)*B*k 式中:W为减少的轧辊重量,D1为应用现有孔型的轧辊辊身直径,D2为应该潜孔型的 轧辊辊身直径,B为轧辊辊身长度,k为金属比重。 本发明的有益效果是: 1、本发明在保证特殊钢产品轧制质量的前提下,将现有孔型设计成潜孔型,使轧 辊上孔型的刻槽深度减少一半,进而使孔型槽底处在硬度层较高的位置,保证了轧辊的过 钢量要求,降低轧辊的使用成本,有效减少轧辊硬度层浪费。 2、由于潜孔型的刻槽深度减小,在孔型侧壁斜度固定的情况下,潜孔型的孔型外 口宽度也随之减小,同时,潜孔型刻槽深度的减小,可以减少轧辊的辊身直径与工作直径的 差值,轧辊在轧辊工作直径相同的情况下,轧辊直径减少了,降低了轧辊重量,节省了轧辊 购置成本。 3、由于潜孔型的外口宽度减少,在布置孔型时,原设计的轧辊辊身只能布设一个 孔型,而按潜孔型设计方法可以布置两个孔型,使轧辊辊身得到了充分利用,提高了轧辊辊 身的利用率,孔型数量的增加,使轧辊的过钢量也随之增加,降低了轧辊的使用成本。 4、本发明将平直型孔型槽底改变成凹型孔型槽底,通过改变孔型槽底形状,解决 氧化铁皮压入轧件上表面所造成的表面质量问题,节省了钢材表面修磨的清理成本。 附图说明: 图1为本发明的结构示意图; 图2为现有轧辊结构示意图; 图3为潜孔型的结构示意图; 图4为现有孔型的结构示意图; 图5为潜孔型在轧辊上的结构示意图; 其中:1轧辊、2现有孔型、3潜孔型。 4 CN 111581751 A 说 明 书 3/4 页